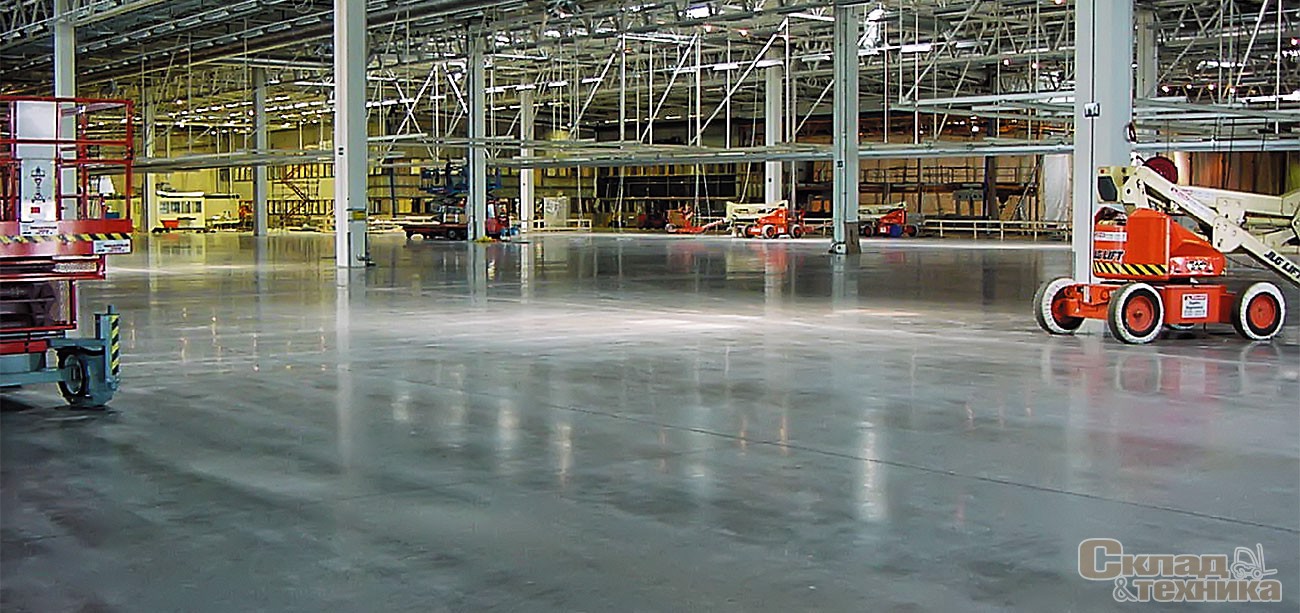
Вопросы обеспечения качества бетона для изготовления промышленных полов
Конструкции промышленных полов из армированного бетона с упрочнением поверхности специальными составами на основе полимеров, полимерцементов и полимербетонов, как известно, являются наиболее долговечными и получили наибольшее распространение в практике строительства промышленных зданий, что обусловливается их невысокой стоимостью, технологичностью и отличными эксплуатационными показателями. В настоящее время при устройстве полов в производственных зданиях применяется бетон классов В22,5–В30, приготовленный на портландцементе.
![[b]А. Горб,[/b] директор ЗАО «СК Конкрит Инжиниринг», советник РАЕ, член международного союза экспертов по строительным материалам, системам и конструкциям RILEM, Американского института бетона ACI и Британской ассоциации бетона CS](/article/13574-voprosy-obespecheniya-kachestva-betona-dlya-izgotovleniya-promyshlennyh-polov/Images/01.jpg)
![[b]И. Войлоков,[/b] доцент кафедры ТОЭС Санкт-Петербургского государственного политехнического университета](/article/13574-voprosy-obespecheniya-kachestva-betona-dlya-izgotovleniya-promyshlennyh-polov/Images/02.jpg)
Уровень развития технологий проектирования и строительства, достигнутый в настоящее время, позволяет обеспечить необходимую долговечность и эксплуатационную надежность конструкций полов. Для обеспечения этого в числе прочего необходимо выполнять следующие основные требования к бетону, указанные в таблице 1.
Технические обследования бетонных полов на ряде промышленных объектов, проведенные совместно специалистами компании ЗАО «СК Конкрит Инжиниринг», ОАО «ЦНИИПромзданий» и Санкт-Петербургского государственного политехнического университета, подтверждают, что при соблюдении всех вышеизложенных требований, как правило, в бетоне отсутствуют признаки разрушения в течение проектного срока эксплуатации.
Однако с развитием химической промышленности и появлением на рынке различных пластифицирующих и водоредуцирующих химических добавок производители товарного бетона (ЦБЗ) стали активно применять их с целью снижения расхода цемента и себестоимости товарного бетона при одновременном обеспечении требуемой проектной (марочной) прочности бетона и заданной подвижности. Ввиду различных технологических особенностей, присущих процессу устройства бетонных полов, применение большинства добавок является недопустимым, а разрешенные добавки должны вводиться в бетонную смесь строго дозированно.
№ п/п | Показатель | Величина показателя |
---|---|---|
1 | Класс бетона по прочности на сжатие | B22,5–В30 |
2 | Марка бетона по морозостойкости | F150–F200 (ГОСТ 10060.0–95) |
3 | Марка бетона по водонепроницаемости | W4 (ГОСТ 10060–95) |
3 | Водоцементное отношение | Не более 0,55 |
4 | Качество цемента | Портландцемент ПЦ 500-Д0 нормированного химико-минералогического и вещественного состава; без технологических добавок (типа триэтаноламина). |
5 | Наличие в бетоне воздухововлекающих добавок | Недопустимо |
6 | Наличие пластифицирующих и водоредуцирующих добавок, %, не более | 0,4 |
7 | Объем вовлеченного в бетонную смесь воздуха, %, не более | 4 |
8 | Качество заполнителей | По ГОСТ 26633–91 |
9 | Подвижность бетонной смеси | Пластичность (осадка конуса) П3–П4 (на месте укладки бетона) |
10 | Уход за свежеуложенным бетоном | С помощью полимерных пленкообразующих составов и полимерных пленок |
Важно подчеркнуть, что преимущества (больший фактический и проектный срок службы, меньшие эксплуатационные и приведенные затраты и др.), обусловливаемые применением при устройстве бетонных полов бетонной смеси с рассмотренными выше параметрами, реализуются только при обеспечении требуемого качества строительства.
В общей проблеме обеспечения требующихся при устройстве промышленных полов параметров бетона центральное место занимает задача сохранения свойств приготовленной бетонной смеси в период ее транспортировки от завода-изготовителя (ЦБЗ) до места укладки (стройплощадки). Очевидно, что все требуемые свойства бетонной смеси должны быть обеспечены именно на месте укладки бетона.
Если не принимать специальных мер, приготовленная бетонная смесь при доставке на стройплощадку может существенно отличаться по качеству от смеси, отгружаемой на цементобетонном заводе. Главным образом это касается показателя удобоукладываемости (подвижности), который меняется в зависимости от продолжительности и условий транспортировки бетонной смеси. Соответственно будут различаться величины прочности изготовленного из нее бетона. Для того чтобы завод-изготовитель мог обеспечить требуемые свойства бетонной смеси на момент ее укладки, он должен заранее, на стадии подбора (по ГОСТ 27006–86), по заданию потребителя предусмотреть необходимые изменения в составе бетона, соответствующие конкретным условиям строительства, в частности условиям транспортировки, например увеличение содержания в нем воды и цемента.
Качество бетонной смеси в настоящее время регламентируется требованиями ГОСТов 7473–94, 26633–91, 18105–86, 10181–2000, 10180–90, 10060–95 и др., а также договором между потребителем товарной бетонной смеси и ее изготовителем. При этом интересы потребителя бетонной смеси (производителя работ на стройплощадке) защищает только ГОСТ 7473–94, которым предусмотрена возможность указать в договоре поставки (п. 4.4) необходимые требования к смеси с учетом конкретных условий транспортировки.
В то же время нормативными документами не оговорен (и не прописан) процесс возможности корректировки потребителем параметров выпускаемой бетонной смеси, необходимость которой вызывается результатами определения фактической однородности бетона в конструкции или на стройплощадке и согласуется с ними. Необходимость такой корректировки очевидна, так как величина фактической однородности напрямую влияет на требования к отпускной прочности бетонной смеси и соответственно на величину расхода цемента.
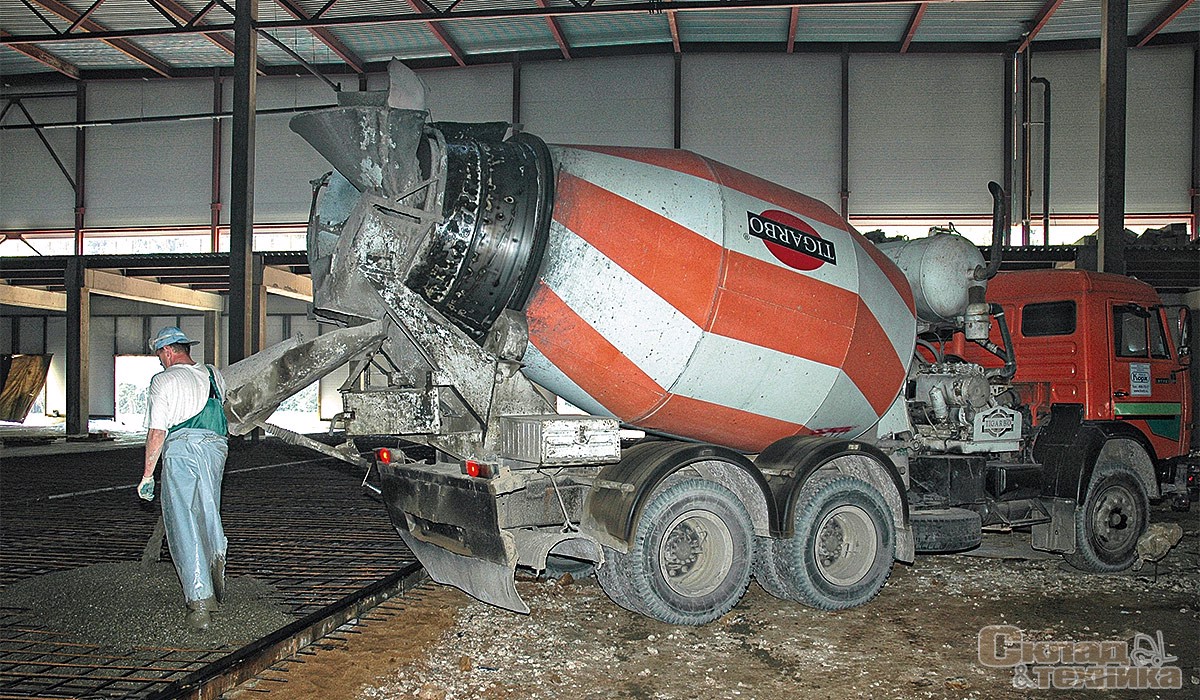
Действующий ГОСТ 7473–94 дает право потребителю проводить контрольную проверку качества только бетонной смеси и технологических свойств, но не указывать в договоре поставки свой коэффициент вариации прочности бетона. В лучшем случае по заданию потребителя поставщик товарной бетонной смеси на момент укладки обеспечит требуемую подвижность смеси и содержание в ней вовлеченного воздуха, но никак не такую же однородность смеси и такой же коэффициент вариации прочности получаемого из нее бетона, как у смеси на момент ее отпуска с ЦБЗ. Завод-изготовитель в соответствии с ГОСТ 18105–86 (п. 3.6) при подборе и корректировке состава бетона использует свой заводской коэффициент вариации прочности бетона. Именно его величина указывается в документе о качестве бетонной смеси по ГОСТ 7473–94 (в паспорте на бетонную смесь). Более того, согласно нормативным документам заводской коэффициент вариации прочности бетона должен использоваться даже в том случае, когда контроль прочности производился не только на ЦБЗ, но и на стройплощадке. То есть и при определении среднего уровня прочности бетона (Ry) при подборе состава бетона, и при ее контроле на стадии определения величины требуемой прочности (RT) по ГОСТ 18105–86 используется заводской коэффициент вариации прочности бетона, который может существенно отличаться от показателя однородности бетона на стройплощадке.
Другими словами, ГОСТ 18105–86 предполагает, что однородность бетона как на ЦБЗ, так и на стройплощадке (через 30–90 мин. после транспортировки бетонной смеси и присущих строительному процессу технологических перерывов) должна быть одинаковой, что, как правило, не соответствует действительности.
Требования ГОСТ 18105–86 предусматривают контроль однородности бетона по прочности и на строительной площадке (п. 2.2). Однако на практике статистический контроль прочности в условиях стройплощадки не ведется, поскольку от него можно отказаться при согласовании с проектной организацией (допускается ГОСТ 18105–86) и поскольку такие результаты определения характеристик однородности бетона нигде не будут учтены.
Кроме этого существенным фактором неоднородности достигнутой прочности бетона являются неодинаковые температурные условия его твердения на месте бетонирования. При этом отсутствует разработанная методология статистического контроля прочности бетона по образцам, твердеющим в реальных условиях строительной площадки (при фактической температуре воздуха в условиях твердения конструкции).
Фактические показатели однородности бетона на стройплощадке по сравнению с показателем при контроле на ЦБЗ, как правило, хуже (коэффициент вариации выше) из-за осуществления, как минимум, еще одной технологической операции – транспортировки. В результате, учитывая измененную процессом транспортировки отпускную однородность бетона (т. е. фактическую на площадке), потребитель, чтобы получить требуемые проектом характеристики бетона в конструкции (обеспечить проектный класс по прочности), должен заказывать производителю состав бетона с более высоким расходом цемента, чем в случае выполнения бетонных работ непосредственно на ЦБЗ (без транспортировки).
Таким образом, следует сделать вывод, что бетон на стройплощадке в отличие от бетона на ЦБЗ, как правило, в силу более низкой однородности должен иметь более высокую величину среднего уровня прочности и соответственно более высокий показатель расхода цемента.
Чтобы создать некоторый запас прочности бетона, учитывающий указанную выше очевидную разницу в однородности бетона на стройплощадке и на ЦБЗ и не нарушить при этом требования действующих стандартов, можно воспользоваться двумя следующими возможностями, предоставляемыми ГОСТ 18105–86 и ГОСТ 27006–86.
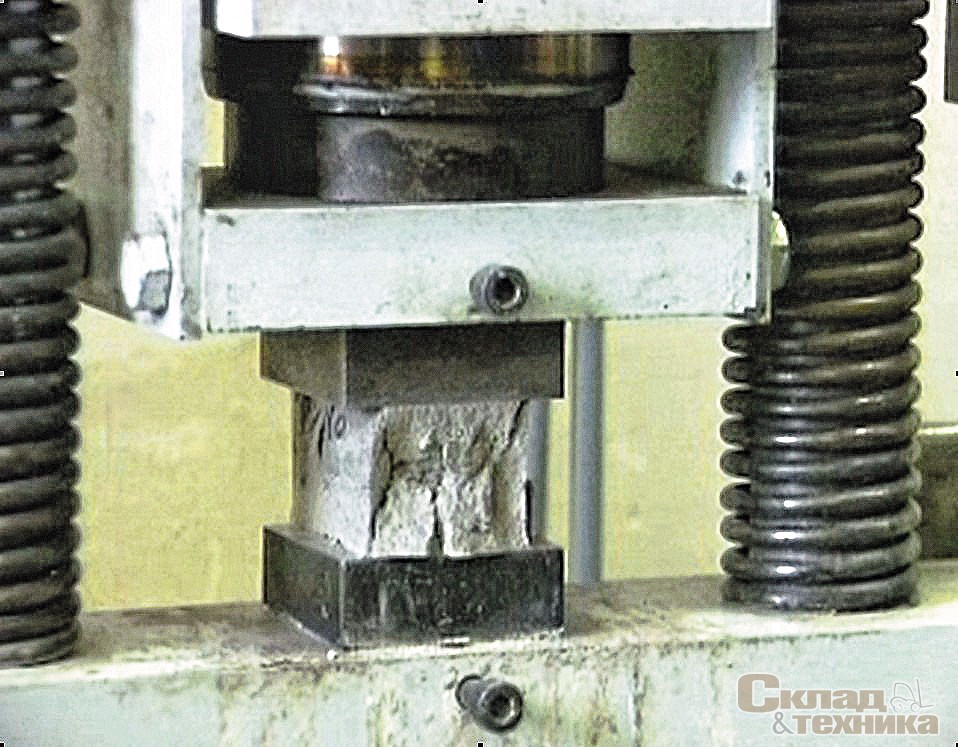
Реально потребитель бетонной смеси не располагает данными о фактической однородности бетона по прочности (по образцам, отформованным и твердеющим в условиях конструкции), а у изготовителя, как правило, нет заранее подготовленного состава бетона, учитывающего этот предполагаемый коэффициент вариации прочности и конкретные условия строительства. В этом случае для обеспечения гарантированного качества товарного бетона на месте укладки целесообразно воспользоваться п. 4.4 ГОСТ 18105–86 и п. 2.3 ГОСТ 27006–86, которые предоставляют возможность определять средний уровень прочности бетона при подборе его состава без учета каких-либо фактических данных о его однородности. При этом коэффициент вариации прочности не определяют экспериментально, величину уровня прочности бетона и величину требуемой прочности назначают:
То есть, другими словами, в этом случае следует применять бетон с прочностью на 10% выше его марки (требуемой прочности при среднем партионном коэффициенте вариации 13%), указав это в договоре поставки бетонной смеси. Это создаст некоторый необходимый запас прочности бетона уже на стадии подбора или корректировки его состава.
Помимо этого потребитель может заранее предположить худший с точки зрения однородности бетона вариант развития событий, когда средний партионный коэффициент вариации прочности бетона достигнет максимально допустимой ГОСТом 18105–86 величины, равной 16%. При этом значение требуемой прочности составит Rm=1,43Bнорм. (ГОСТ 18105–86, п. 4.1), а значение среднего уровня прочности будет больше еще на величину коэффициента Км.п.=1,1 (ГОСТ 18105–86, п. 6.1, ГОСТ 27006–86, п. 2.3) и составит Ry=1,1·1,43=1,57Bнорм. То есть во втором из рассмотренных вариантов создаваемый запас прочности бетона будет выше, чем в первом.
Таким образом, при использовании статистических методов контроля прочности монолитного бетона шагом вперед в обеспечении его качества на стройплощадке будет назначение заранее величин Ry=Rm=1,41Bнорм. или Ry=1,57Bнорм. и Rm=1,43Bнорм. Потребитель бетонной смеси должен уведомить заранее производителя об этих требованиях к готовой бетонной смеси и согласовать их с проектировщиком и заказчиком.
О правильности указанного подхода свидетельствуют также результаты испытания на прочность образцов-кернов, выбуренных их бетонных плит готовых промышленных полов и бетонных оснований. Получаемый при этом коэффициент вариации прочности бетона, как правило, на 5–10% (абсолютных) выше, чем по результатам испытания контрольных образцов (кубиков). Это также подтверждает целесообразность приблизить используемый в расчетах коэффициент вариации прочности бетона к реальным значениям этой величины в конструкциях, применять величины Ry=1,41Bнорм. или Ry=1,57Bнорм. и поднять среднюю прочность.
Аргументом в пользу необходимости пересмотра ГОСТ 18105–86 является также использование такого нестатистического приема при ведении статистического контроля прочности, как отбраковка заранее из серии (выборки) полученных результатов наихудших значений (ГОСТ 10180–90, п. 6.4). Другими словами, при статистическом контроле некорректно использовать параметры нормального распределения прочности бетона, одновременно искусственно ограничивая разброс ее значений в серии и тем самым завышая среднее значение прочности.
В задании на подбор состава бетона должны быть обязательно отражены требования к сохранности свойств бетонной смеси. Как правило, подвижность бетонной смеси уменьшается в течение 30–60 мин. на 1–4 см, что должно определяться на стадии подбора состава бетона. Высокая интенсивность изменения свойств бетонной смеси со временем косвенно свидетельствует о вероятном снижении качества бетона на месте укладки, прежде всего ее удобоукладываемости и удобообрабатываемости.
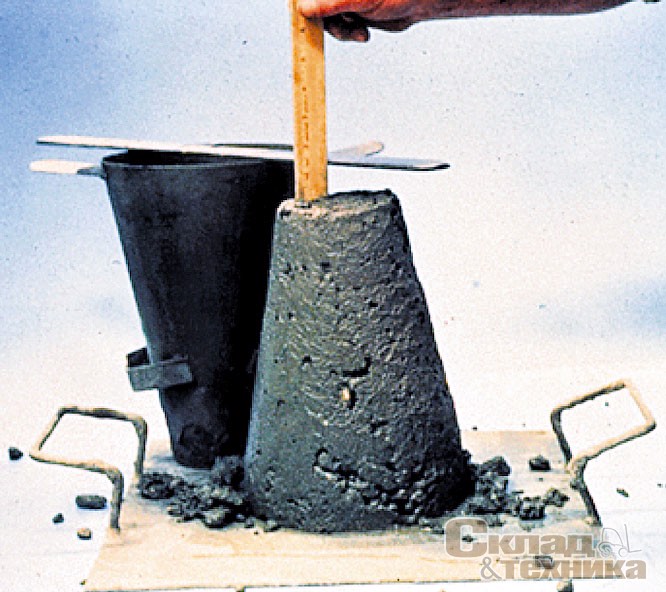
Потребитель бетонной смеси должен в соответствии с действующей нормативно-технической документацией обеспечить ее требуемые свойства на месте бетонирования и может добиться этого, по нашему мнению, только строгим приемочным контролем (при необходимости каждой поступающей с завода машины со смесью), включая отбраковку некачественной продукции. Такая помашинная приемка, в частности, предусмотрена положением СНиП 3.06.03-85 (п. 12.58), согласно которому следует контролировать свойства бетонной смеси и бетона не только раз в смену, но и при любом изменении качества смеси на месте бетонирования. В этом случае, возможно, показатели однородности прочности бетона по отформованным контрольным образцам (на стройплощадке) приблизятся к показателям, полученным при испытании выбуренных из конструкции образцов-кернов. Этот вопрос объема контроля бетонной смеси на стройплощадке требует дополнительного исследования.
Следует еще раз подчеркнуть, что качество бетона и долговечность полов в целом обеспечиваются не достижением каких-либо одного-двух проектных показателей, например прочности бетона, но и соблюдением абсолютно всех требований к другим материалам, составу бетона, свойствам бетонной смеси и технологии выполнения работ, установленных в нормативно-технических документах. То есть должно обеспечиваться соблюдение всей системы нормативных и проектных требований, которые взаимно дополняют, но не заменяют друг друга. Достижение проектной марки бетона по прочности не означает, что можно ослабить другие указанные выше требования.
На основании приведенных нами рассуждений можно сделать следующие основные выводы.
• Достигнутый в настоящее время уровень развития технологий позволяет получать высококачественный бетон гарантированной прочности.
• Для бетона, применяемого при устройстве полов, при подборе и корректировке состава следует назначать величину среднего уровня прочности в виде Ry=Rm=1,41Bнорм. или Ry=1,57Bнорм. Эти величины прочности должны быть оговорены в договоре поставки бетонной смеси и в задании на подбор состава бетона.
• На месте укладки бетона рекомендуется увеличить объем работ по контролю качества бетонной смеси, в том числе вести помашинную приемку и выбраковку бетонной смеси.
• Контроль прочности бетона следует также вести по образцам, формуемым на месте укладки бетона и твердеющим до достижения проектной прочности в построечных условиях твердения конструкции.