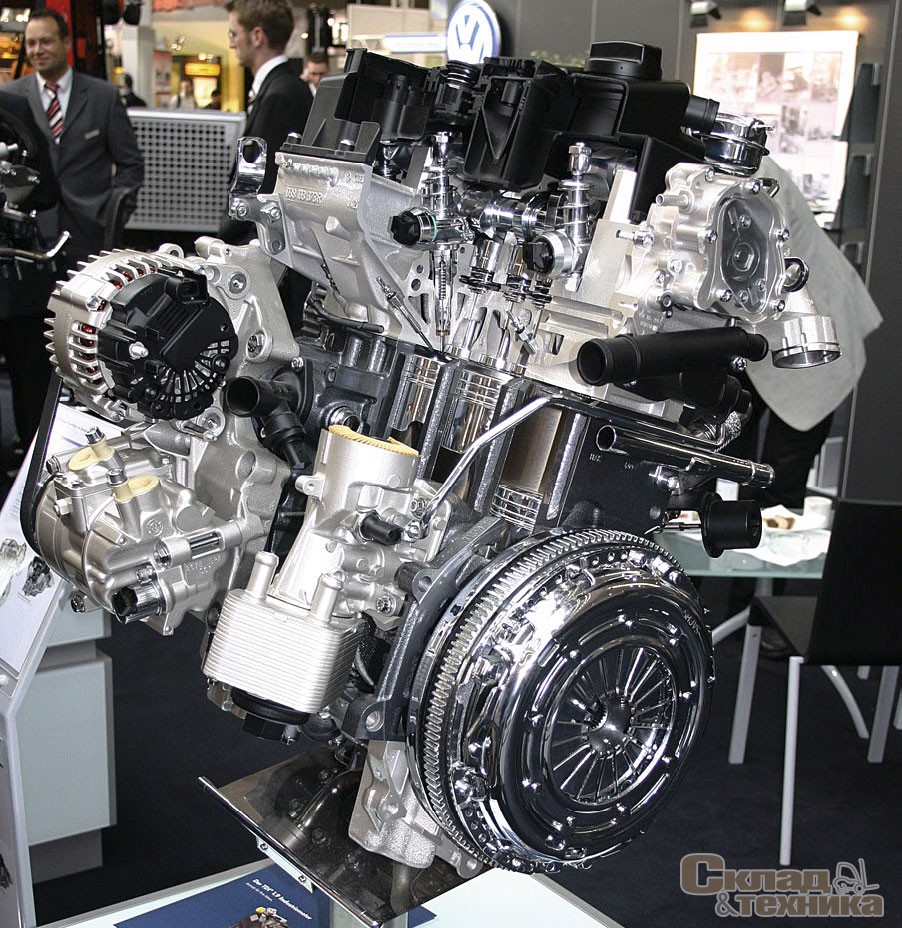
Компоненты погрузчиков (Часть 1)
Продолжаем публикацию перевода отдельных глав из книги «100 лет вилочному погрузчику», выпущенной бельгийской компанией TVH (100 Years Forklift Trucks. Belgium: TVH Forklift Parts N.V., 2005). Настоящая статья посвящена некоторым наиболее важным компонентам погрузчиков разных типов.
Двигатель внутреннего сгорания
Бензиновые и дизельные двигатели основательно менялись не только внешне. В процессе технического совершенствования они становились все более мощными, экономичными, безопасными для окружающей среды и менее шумными. С момента появления и примерно до 1960 г. большинство вилочных погрузчиков оснащали двигателями, заимствованными от автомобилей.
Так продолжалось до тех пор, пока фирма Toyotа первой, по ее собственному заявлению, не создала исключительно экономичные промышленные двигатели с меньшей частотой вращения. Первые дизели для погрузчиков были шестицилиндровыми рабочим объемом 4000 м3, позже их заменили трех- или четырехцилиндровыми объемом 2000 см3 и меньше, при этом мощность их была такой же. За двигателями с воздушным охлаждением последовали двигатели с водяным охлаждением, которые могут быть лучше изолированы и благодаря этому производят меньшее звуковое давление. В дальнейшем во всем мире стали придавать все большее значение безопасности и комфорту при работе с техникой. Эмиссию двигателей внутреннего сгорания, как и уровень создаваемого ими шума, стали регулировать строгими предписаниями. В Европе дизельный привод все больше вытеснялся бензиновым.
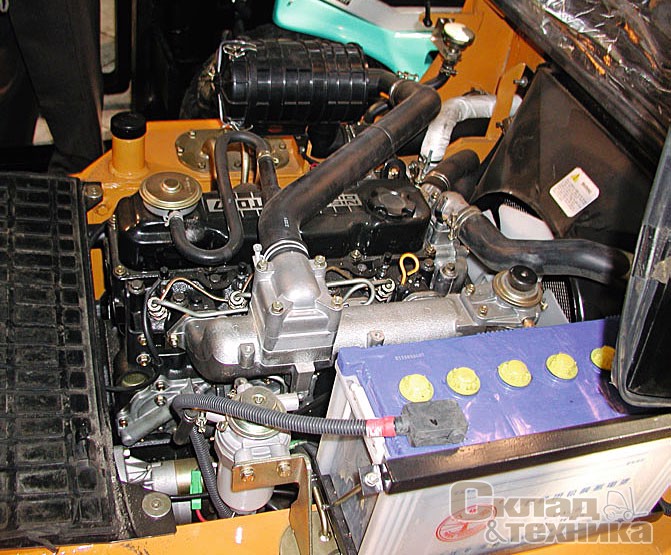
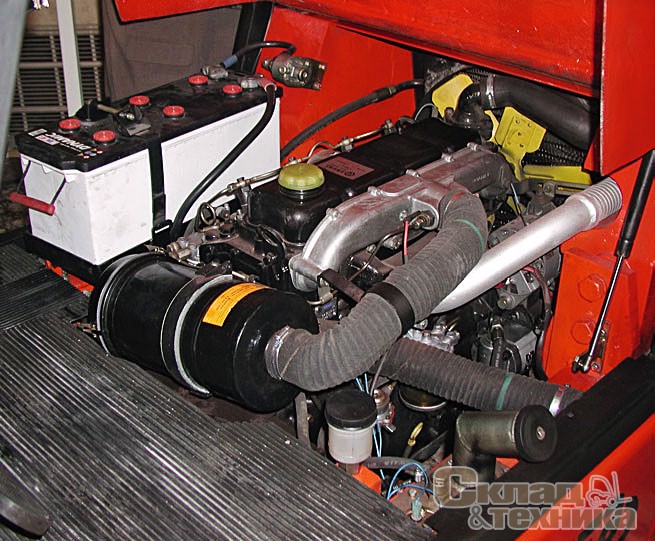
Наконец немецкая фирма Still создала вместо чадящего дизеля очень экономичные гибридные дизель-электрические агрегаты. Техника с двигателями внутреннего сгорания теряет позиции на рынке не только из-за более строгих норм по защите окружающей среды, сколько вследствие интенсивного развития и роста сбыта внутрискладского напольного транспорта, который питается исключительно электроэнергией.
Тем не менее дизельные двигатели все еще продолжают применять на погрузчиках, которые выпускаются для европейского рынка, и причин тому несколько. Во-первых, из-за стоимости, так как дизельный силовой агрегат требует меньших инвестиций при покупке, потреблении энергоносителя и обслуживании, чем электрический. Во-вторых, дизель все еще остается надежным, удобным в обслуживании, мощным и эффективным источником энергии. Конечно, большой его недостаток – выброс сажи, который еще сильнее возрастает при изменении частоты вращения двигателя и применении серосодержащего (прямогонного) дизельного топлива. В некоторой степени эту проблему решает сажевый фильтр: в зависимости от качества и типа он снижает вредные выбросы на 70...98%, но и сегодня такими фильтрами снабжено самое большее от 4 до 5% всех дизельных двигателей, прежде всего из-за их очень высокой продажной цены – от 2 до 4 тыс. евро.
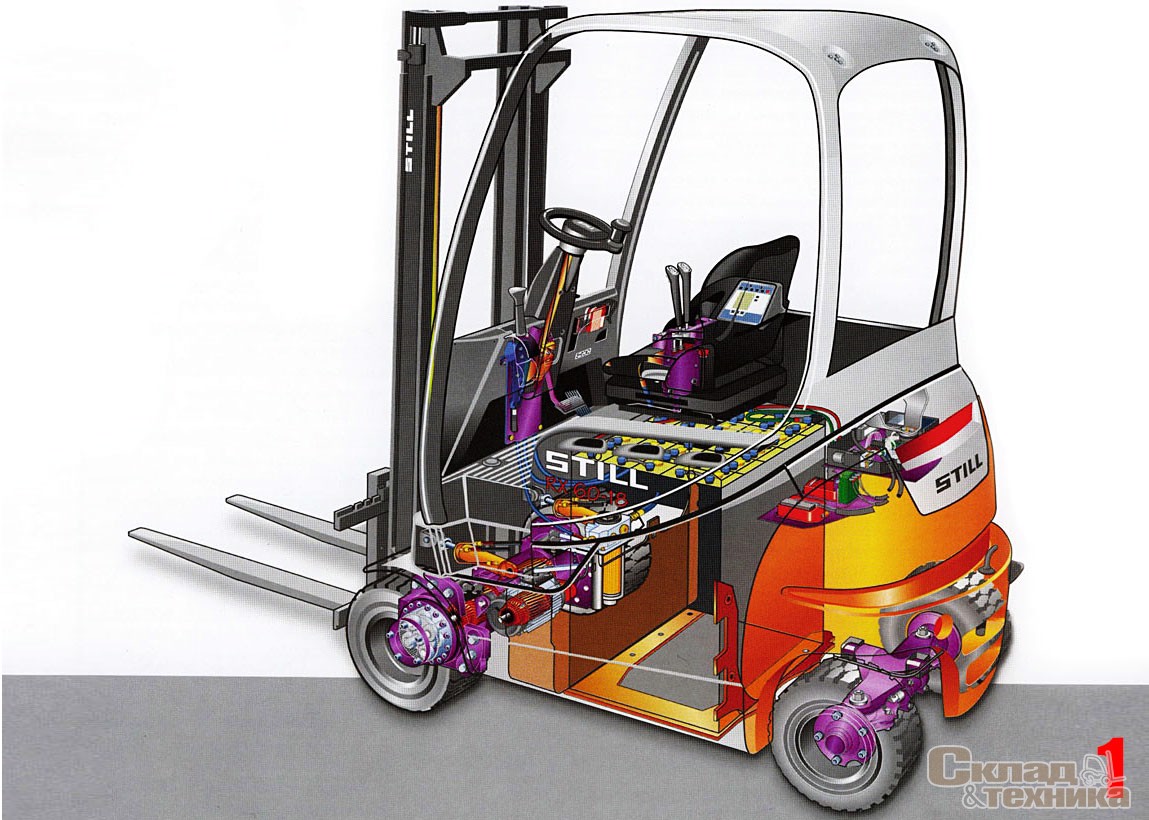
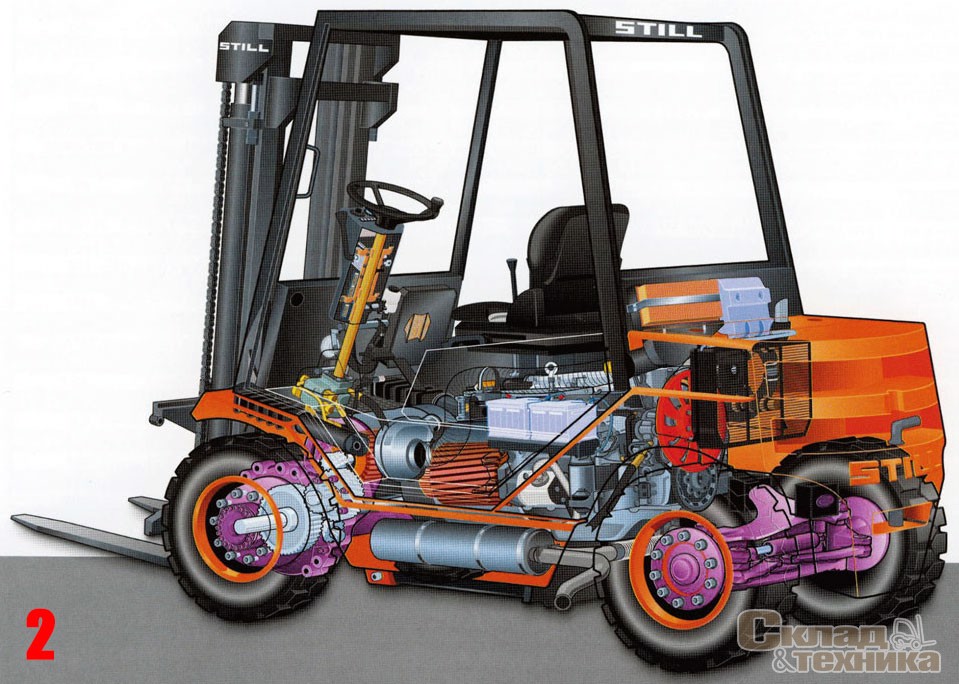
Наряду с дизельными применяют также двигатели на газообразном топливе, которые чаще всего представляют собой соответствующим образом реконструированные бензиновые двигатели. Покупатель может выбирать между гибридным агрегатом или агрегатом на чистом газообразном топливе. В случае гибридной системы водитель может «переключить» машину с газа на бензин. Это целесообразно, когда нет возможности непосредственно заправить машину газом и водитель ориентирован на использование запасных баллонов. В этом случае бензин используют, пока со склада не доставят полный баллон (о времени, когда водитель должен подключить запасной баллон, сигнализирует индикаторная лампа). Однако мощность двигателя при работе на бензине и на газовом топливе не одинакова, поэтому она используется не оптимально, и покупатель в большинстве случаев делает выбор в пользу газового двигателя. Чисто бензиновые двигатели на вилочных погрузчиках едва ли еще встречаются в Европе: более 95% всех бензиновых двигателей на погрузчиках уже переработано для использования газообразного топлива.
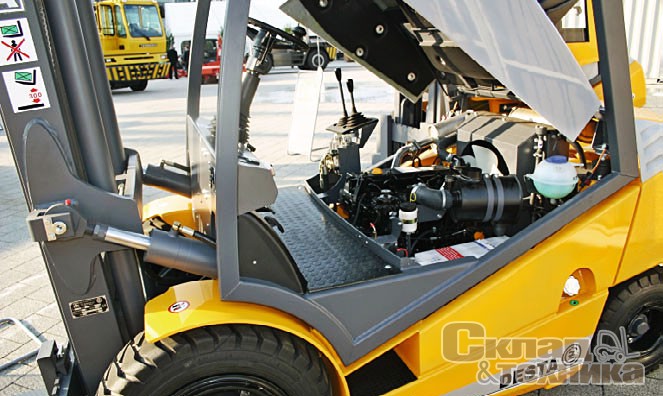
Грузоподъемное устройство
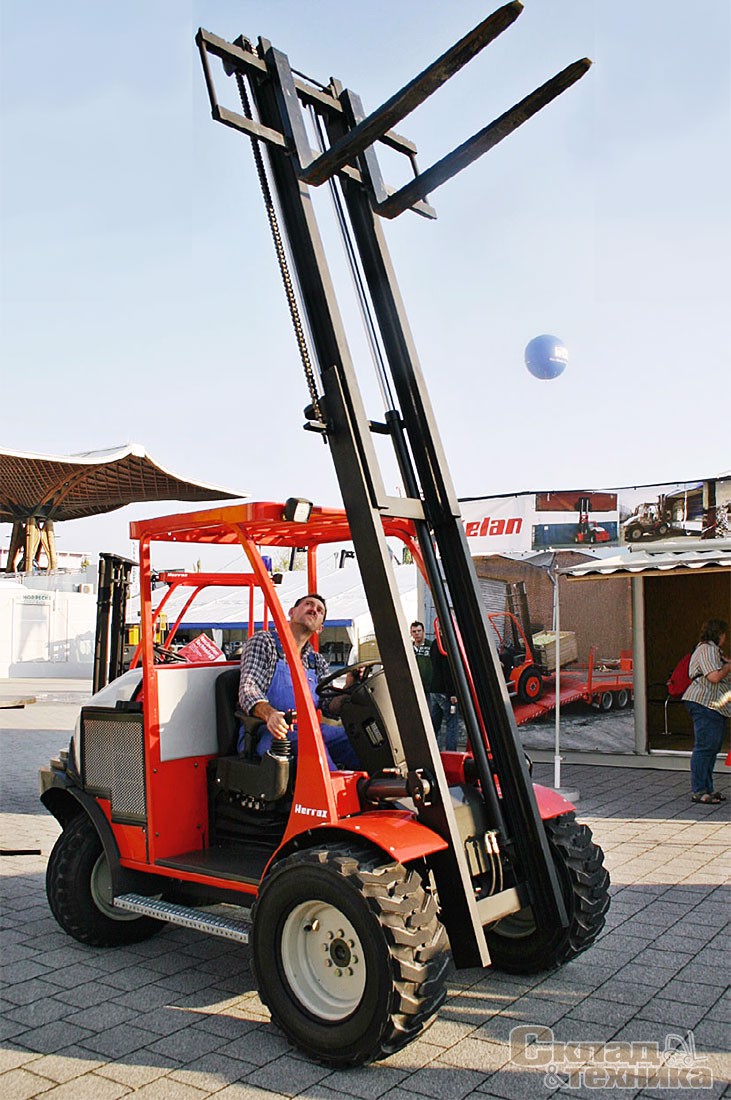
Применяя новые материалы и создавая более жесткие конструкции с увеличенной прочностью на изгиб, изготовителям удалось уменьшить массу мачты погрузчика и одновременно повысить ее способность устанавливать или захватывать тяжелые грузы на большей высоте. К началу XXI в. максимальная высота мачты обычных вилочных погрузчиков с противовесом составляет около 8 м, примерно 10 м – у высотных штабелеров-ричтраков, и свыше 12 м – у некоторых моделей комбинированных погрузчиков и штабелеров для трехсторонней обработки грузов.
На автоматизированных складах не являются редкостью высотные краны с высотой подъема грузов от 15 до 18 м (!), что еще недавно трудно было представить. Чтобы дополнительно обезопасить движение груза на таких высотах, транспортное оборудование оснащают специальной защитой от вибрации и системами компенсации толчков от неровностей пола.
На самых первых вилочных погрузчиках наклон мачты выполнялся с помощью механической системы с зубчатой рейкой, и только позднее для этих целей стали применять отдельный или, в исключительных случаях, сдвоенный цилиндр наклона. В настоящее время мачта погрузчика, как правило, наклоняется с помощью двух гидроцилиндров, которые одним концом крепятся к середине мачты, а другим – к нижней части шасси (исключением являются, например, последние модели компании Linde, на которых цилиндр наклона прикреплен одним концом к верхней половине мачты, а другим – к верху кабины). Это не только повышает жесткость мачты, но и обеспечивает беспрепятственный проход в кабину водителя, что одновременно повышает безопасность работ. У погрузчиков (штабелеров) с выдвижной мачтой, которые устанавливают груз или принимают его на большой высоте, наклоняются только вилы. При наклоне мачты на такой высоте центр тяжести груза находился бы настолько далеко вынесенным вперед, что транспортное оборудование могло просто опрокинуться или его остаточная грузоподъемность была бы слишком низкой.
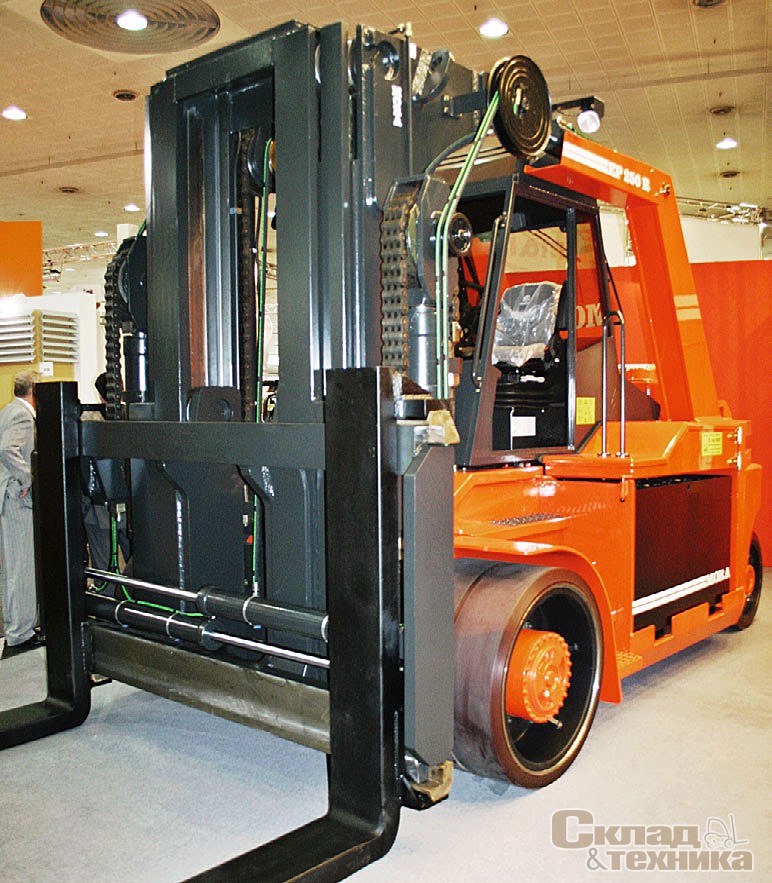
Гидравлика
С середины 1930-х годов расположенный посредине мачты гидравлический цилиндр работал от гидравлического насоса, который в свою очередь приводился в действие двигателем. Таким образом, можно было поднимать мачту и каретку с вилами с помощью роликовой цепи, а не как раньше – стальными канатами. Первыми изготовителями таких мачт второго поколения были Towomotor (модель L) и Clark (модели Tructier). Погрузчик Tructier B имел даже телескопически выдвигаемую подъемную мачту.
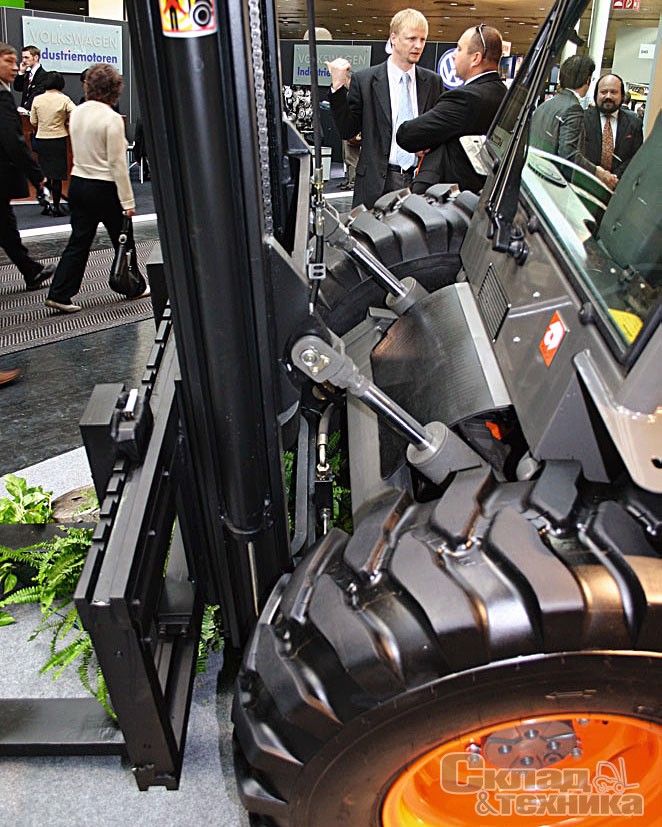
В конце 1930-х гг. появилось устройство наклона мачты. Чтобы иметь возможность регулировать угол наклона, сначала применяли зубчатую передачу с тормозом, что позволяло также изменять скорость наклона. В 1937 г. фирма Towomotor для регулирования угла наклона телескопической мачты нового модельного ряда CU применила гидравлику. Цилиндры наклона – сначала один, а затем два – управлялись через гидравлический клапанный блок. Следующим шагом в развитии этой техники стала замена гидравлических управляющих клапанов пропорциональными клапанами, что позволило очень точно менять угол наклона с помощью небольших рычагов, а позднее и джойстиков, которые располагались рядом с водителем или даже в правом подлокотнике его кресла. Благодаря этому управление стало более эргономичным, безопасным и компактным. Длинные рычаги гидравлических клапанов исчезли вовсе, а гидравлические клапаны, сначала расположенные на внутренней стороне передней стенки погрузчика, обрели место под полом кабины. В 1990-е гг. гидравлические системы превратились в системы высокого давления, рассчитанные примерно на 200 бар (вместо прежних 140 бар). Благодаря этому появилась возможность не только сделать цилиндры подъема и наклона компактнее, но и повысить скорость подъема вил, а водитель получил лучший обзор между стойками мачты.
Только в середине 1950-х гг. тяжелое механическое рулевое управление (с рейками и зубчатыми колесами) заменили изобретенным Фрэнсисом В. Дэвисом (Francis W. Davis) гидравлическим сервоуправлением. Речь идет о гидравлической приводной системе с клапанами, которая сначала встраивалась в боковой управляющий цилиндр, а позднее под рулевую колонку, при этом управляющий цилиндр располагался сбоку погрузчика. В 1990-е гг. управляющий цилиндр двухстороннего действия был, наконец, интегрирован в заднюю ось, благодаря чему появилось так называемое гидростатическое управление. Позднее, уже в конце 1990-х, электронное управление вытесняет преимущественно гидравлическое или гидростатическое, прежде всего на электропо-грузчиках и тяжелых погрузчиках. При электронном управлении датчик регистрирует, на сколько и в каком направлении водитель поворачивает штурвал, после чего посылает сигнал об этом в систему управления, которая и выдает электродвигателю команду, в какую сторону и на какой угол должны быть повернуты управляемые колеса.
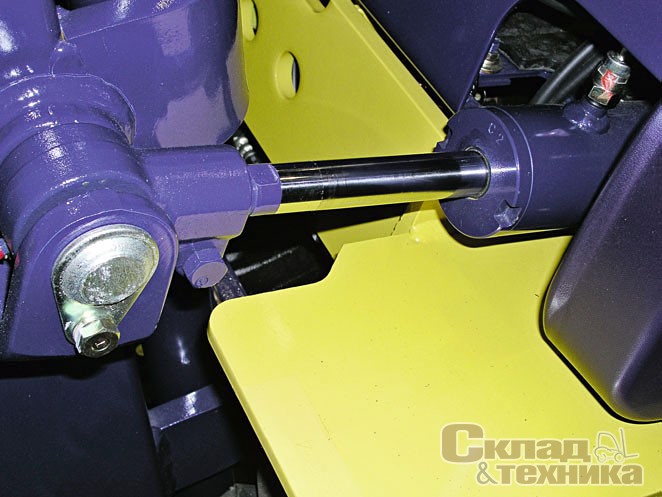
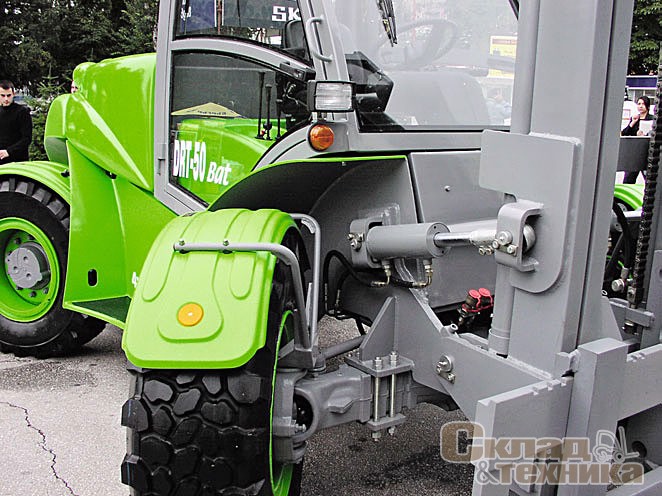
Гидравлика значительно повышает комфорт и безопасность и при торможении погрузчика. Если первые серийные модели еще имели механический тормоз, то вскоре его заменил тормоз с главным тормозным гидроцилиндром. Вскоре повсеместно стал стандартным оснащением тормозной гидроусилитель, по крайней мере, на погрузчиках средней и большой грузоподъемности. С его помощью водитель может легким нажатием на педаль получить большое тормозное усилие. Как мы отмечали выше, в моделях корейских вилочных погрузчиков и на погрузчиках большой грузоподъемности стали применять работающие в масляной ванне дисковые тормоза, которые значительно снизили расходы на техническое обслуживание.
Не менее активно гидравлика прокладывает дорогу новому навесному оборудованию. Уже в конце 1920-х гг. Yale впервые предложил в качестве навесного оборудования для вилочных погрузчиков гидравлический захват и наклоняющиеся вилы. C 1950-х гг. стали применять гидравлические механизмы бокового смещения вил, а уже в 1990-е встроенные механизмы бокового смещения и другое навесное оборудование, прежде всего на вилочных погрузчиках грузоподъемностью 5 т и выше, даже стало считаться стандартным вариантом комплектации. Это позволило не только сократить габаритные размеры машин, но и улучшить обзор через мачту и тем самым повысить безопасность.
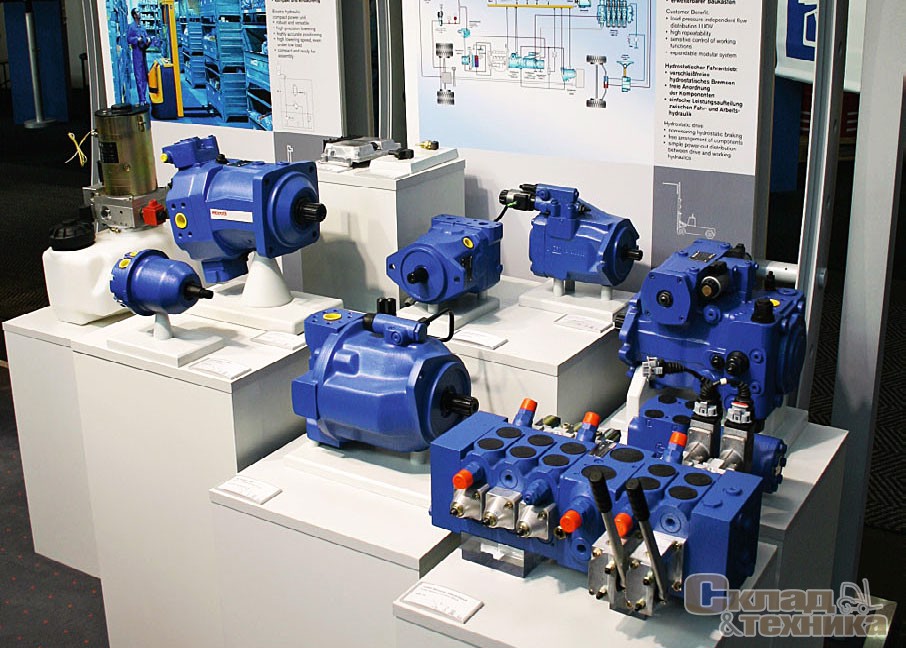
Навесное оборудование
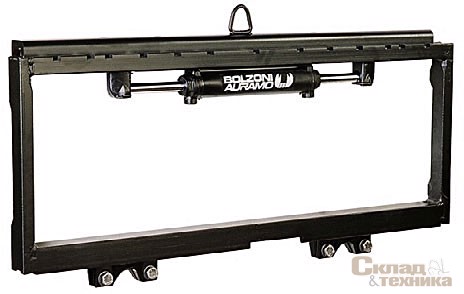
Одним их наиболее распространенных рабочих органов для погрузчиков является механизм бокового смещения вил, облегчающий позиционирование груза на стеллаже или в кузове автотранспортного средства. Первые механизмы бокового смещения вил появились примерно в годы Второй мировой войны и крепились впереди на траверсе несущей вилы. Это снижало грузоподъемность примерно на 10%. B настоящее время механизм бокового смещения обычно встраивают в каретку, так что потери грузоподъемности почти не происходит. Допустимая величина бокового смещения регулируется нормативами Eвросоюза: так, у вилочных погрузчиков максимальной грузоподъемностью менее 5 т она может составлять максимум 100 мм в обе стороны – при этом условии остаточная грузоподъемность не снижается. Интегрированный механизм бокового смещения и другое современное навесное оборудование обеспечивают большую остаточную грузоподъемность, так как размеры их выступающих частей и масса постоянно уменьшаются. Новые механизмы бокового смещения имеют коробчатый профиль: при такой конструкции обеспечивается лучший обзор концов вил и груза и тем самым большая безопасность водителя.
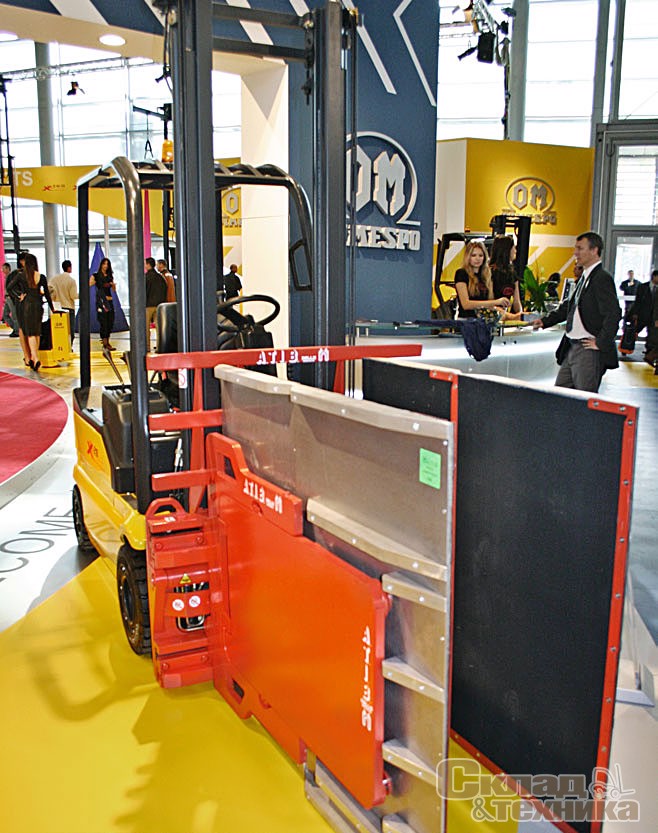
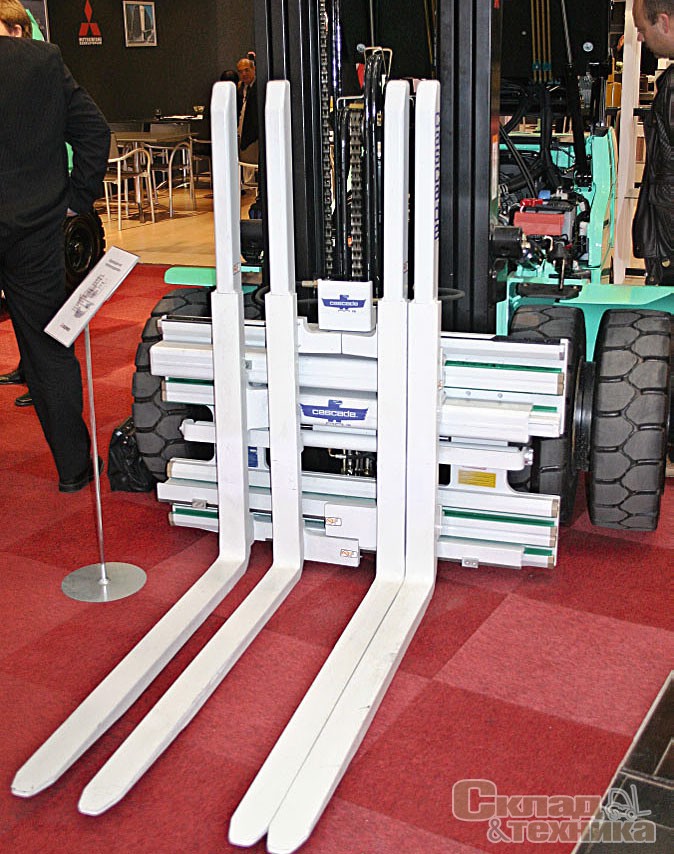
Шины
На первый взгляд может показаться странным, но маневренность и быстродействие вилочного погрузчика во многом зависят от таких его компонентов, как шины. До конца 1930-х годов колеса вилочных погрузчиков, как правило, оснащали бандажными шинами. Кольцо из плотной и износостойкой резины сначала наклеивали на стальное кольцо, а потом вместе с ним напрессовывали на цилиндрический обод колеса. Основной проблемой, которая решалась еще некоторое время, стала разработка технологии, предотвращающей соскальзывание такой шины с плоского цилиндрического обода: для этого форма обода и края шины должны были точно соответствовать друг другу. Позже стали применять пневматические шины и массивные шины из суперэластика. Для того чтобы вилочные погрузчики при торможении и повороте не оставляли следов на полу, что бывает необходимо при работе на пищевых и фармацевтических предприятиях, их оснащают так называемыми «непачкающими» шинами (non-marking).
В применении шин существуют большие различия между американским рынком и прочими рынками. В США вилочные погрузчики преимущественно комплектуют бандажными шинами, тогда как в других регионах мира используют в основном пневматические или массивные шины. Бандажные шины обеспечивают самое надежное сцепление при работе на ровных напольных или дорожных покрытиях. Оснащенные ими вилочные погрузчики при той же грузоподъемности и устойчивости, что и модели с пневматическими или массивными шинами, получаются более компактными, но, к сожалению, менее комфортными для водителя. В 1936 г. фирма Hyster выпустила первые модели тяжелых вилочных погрузчиков на пневмошинах (Jumbo 7T). В настоящее время вилочные погрузчики с пневматическими или массивными шинами успешно выполняют свои функции на грубых дорожных покрытиях, однако в этом случае, конечно, играют важную роль качество шин, давление в них и особенности трассы движения.
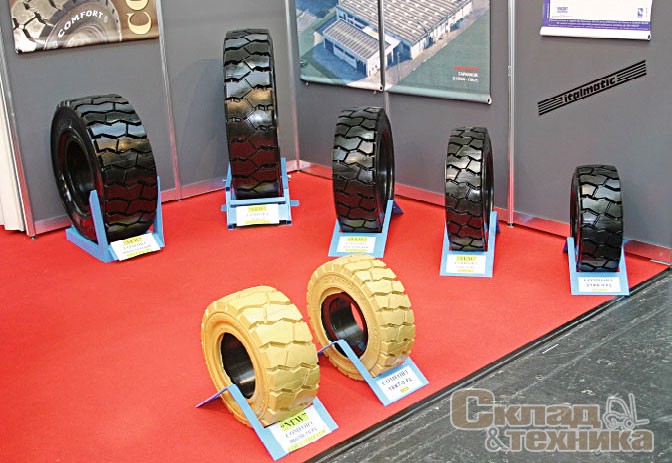
Тормоза
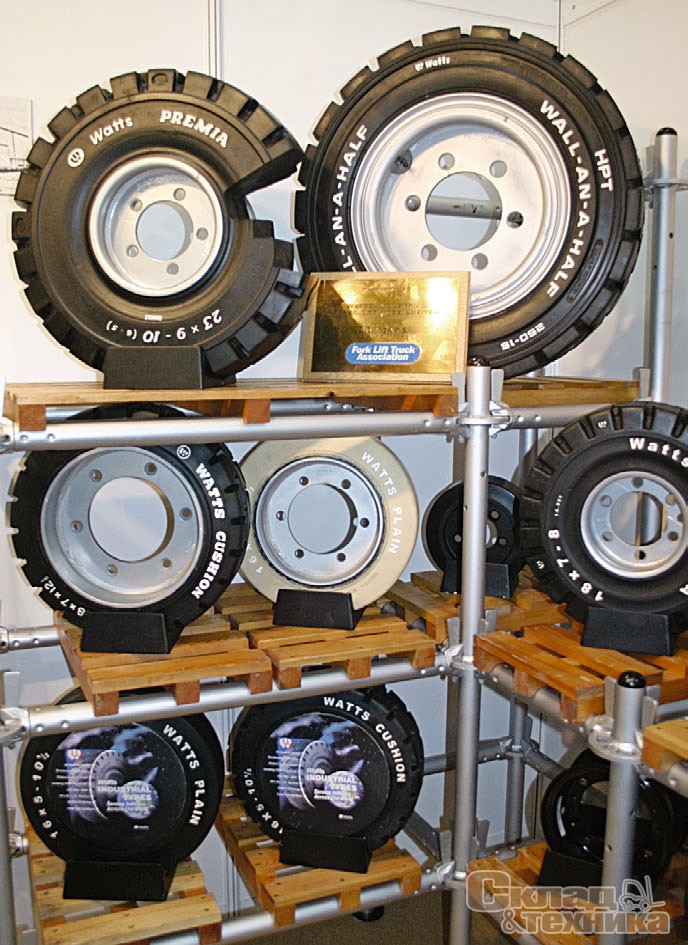
Что касается тормозной системы, то комфорт движения и безопасность работы машин здесь повышались прежде всего за счет развития гидравлических конструкций. Первая транспортная тележка марки Clark образца 1917 г. и некоторые другие образцы этой техники, выпущенные в 1920–1930-е гг., еще не имели тормозов. Только следующее поколение напольного транспортного оборудования получило механические тормоза, но очень скоро их сменила тормозная система с гидравлическим приводом. В настоящее время практически каждый погрузчик грузоподъемностью свыше 2 т имеет гидроусилитель тормозов, который даже минимальное усилие нажима на педаль может превратить в энергичный процесс торможения. Чтобы удержать расходы на обслуживание этих систем на возможно более низком уровне, большинство южнокорейских фирм, таких как Daewoo, Hyundai и Samsung (Сlаrk), в настоящее время оснащает свои вилочные погрузчики дисковыми тормозами, работающими в масляной ванне, что у других компаний являлось стандартом комплектации только для тяжелых погрузчиков. До недавнего времени эта технология считалась слишком дорогой, но опыт показывает, что многочисленные преимущества тормозов, работающих в масляной ванне, значительно перевешивают такой их «минус», как высокая стоимость. Благодаря более плавному процессу торможения, и прежде всего росту тормозного усилия без блокировки колес, значительно повысилась надежность этих узлов.
Существуют и другие разработки. После создания гидростатической трансмиссии компания Linde и в сфере тормозной техники пошла собственным путем. Через гидростатическую передачу усилия удается хорошо оперировать обеими функциями – ускорением и торможением (побочный эффект гидростатического привода) – и управлять движениями вперед-назад всего одной педалью.
В отношении ускорения и изменения направления движения погрузчики с гидростатическим приводом наиболее эффективны. Разработками в этой сфере пробовали заниматься Caterpillar, Сlаrk и под конец Jungheinrich, но до сих пор их попытки были безуспешными. Для того чтобы ездить на машине с гидростатическим приводом, требуется некоторая практика, но каждый, кто хотя бы однажды имел такую возможность, ощутил все преимущества, которых не хватает обычной трансмиссии с гидротрансформатором.