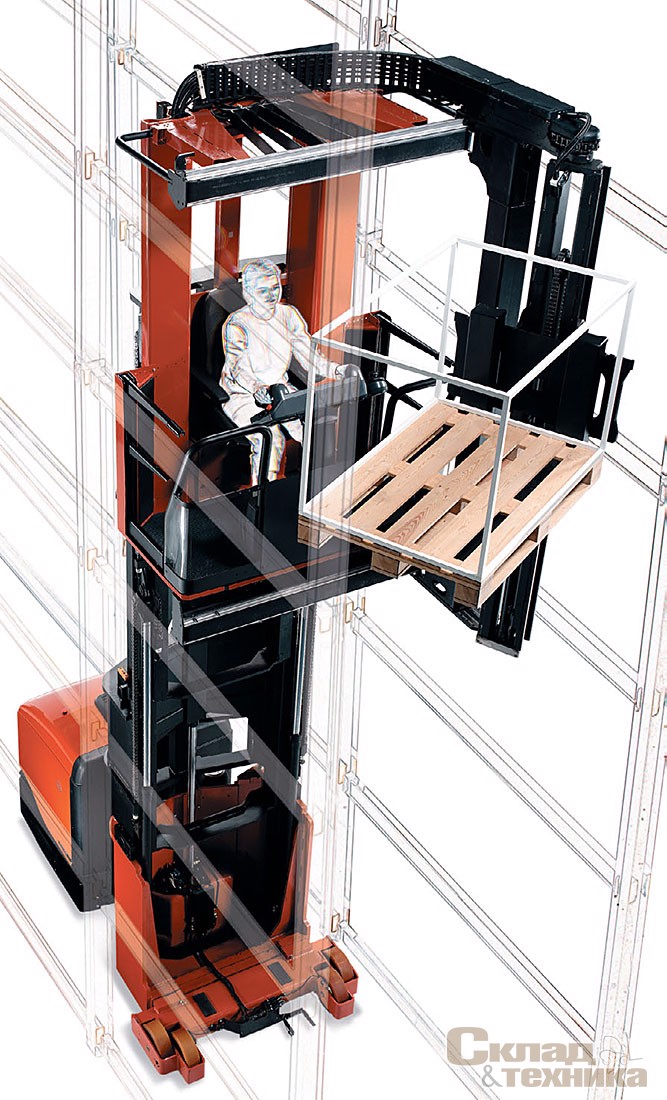
Узкопроходные высотные штабелеры и погрузчики
(Часть 2)
Несмотря на важность грузовысотных, динамических и других технических параметров, их изучение при покупке высотных VNA-штабелеров чаще всего занимает немного времени. Более подробно покупатель и поставщик обсуждают конкретные условия применения техники, и здесь на первый план выходят такие критерии, как ширина проезда и особенно характеристики и состояние напольного покрытия в зоне движения оборудования.
Ширина аллеи и качество напольного покрытия трассы
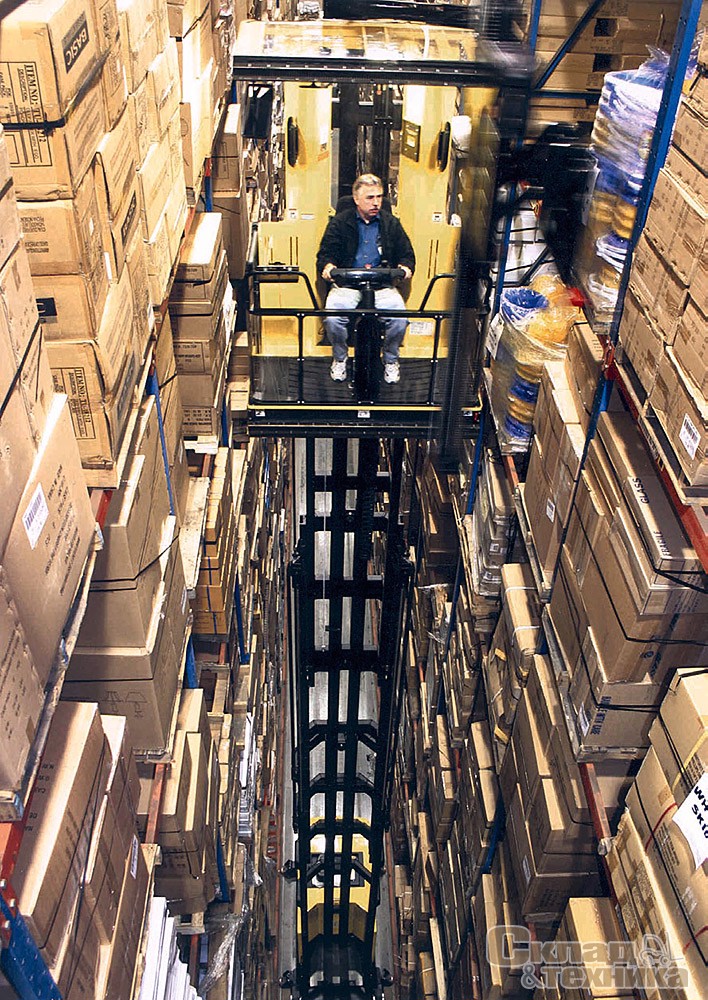
У любого владельца склада всегда есть искушение максимально увеличить зоны хранения и уплотнить проходы между стеллажами, однако при этом нельзя упускать из виду вопросы безопасности работ, особенно актуальные, если их проводят на большой высоте. Ширина аллеи для проезда высотного штабелера должна быть такой, чтобы выдержать оптимальный баланс между производительностью и безопасностью. Еще в 1999 г. Британская Ассоциация индустриального транспорта (British Industrial Truck Association, BITA) ввела в действие директиву Guidance Note 9 (GN9), определившую минимальное расстояние между стеллажами, которое требуется для проезда, исходя из типов и комбинации используемого напольного транспорта. Директива первоначально была утверждена для участков, где использовались противовесные погрузчики и ричтраки, лишь несколько позже она установила идеальную ширину аллеи для работы высотной VNA-техники.
По утверждению Джона Магвайра (John Maguire), директора по продажам и маркетингу компании Narrow Aisle, при оценке минимальной ширины проезда в соответствии с GN9 самым важным параметром стали габариты поддонов. Если VNA-техника должна вращать паллету в проходе, то необходимо гарантировать, что при движении она не будет задевать грузы, стоящие на поддонах в стеллажных ячейках и обычно выступающие за их габариты. Таким образом, определять ширину прохода, которая по существу представляет собой «чистое» расстояние между поддонами с обеих сторон аллеи, следует очень точно, учитывая в том числе и возможные свесы груза за пределы поддона. Поэтому уже на нижних ярусах к величине диагонали поддона надо добавить еще 25...30 см, так как углы поддона при развороте описывают дугу, т. е. зазор между поддоном и стеллажом с обеих сторон должен быть не менее 10 см.
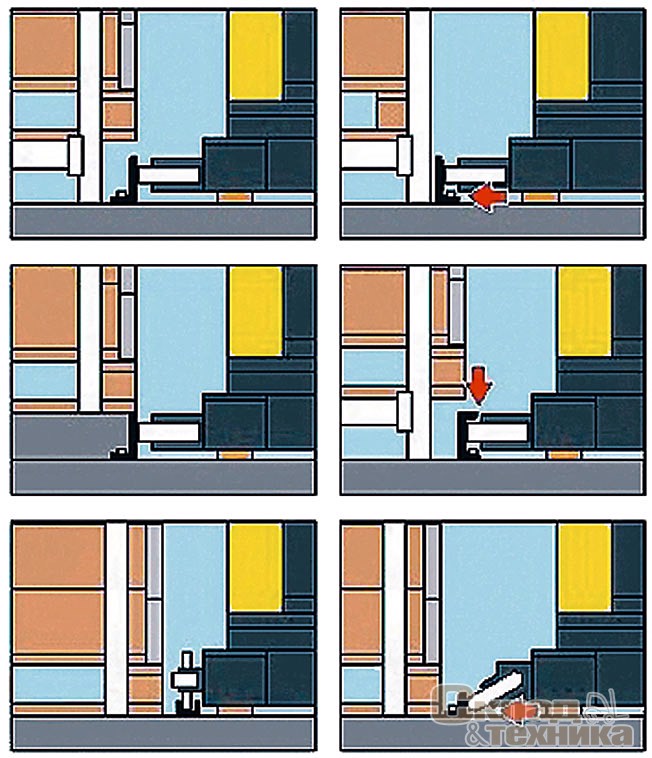
Если штабелер работает на высоте свыше 6 м, этот зазор необходимо еще увеличить. Магвайр рекомендует, чтобы ширина прохода там, где используются стандартные британские поддоны, была по крайней мере не меньше 1,762 м, тогда она будет соответствовать нормам GN9. Хотя эта величина значительно меньше, чем требуется для работы VNA-штабелера, но при этом не ставится под угрозу безопасность людей и грузов. Если поддон не требуется поворачивать, ширина аллеи может быть меньше. В этом случае к размеру поддона – поперек или вдоль – также добавляют ширину дополнительной грузоподъемной мачты и зазор безопасности 20 см. В целом для разных моделей VNA-техники минимальная ширина аллеи может составлять от 1,4 до 1,8 м.
Решающее влияние на работу всего узкопроходного склада в конечном счете оказывают не динамические параметры машин, а состояние трассы в аллее. Как уже было отмечено в первой части статьи, благополучно передвигаться по узким проходам на высоких скоростях без вмешательства оператора VNA-штабелерам помогают направляющие – механические (рельсы и ролики) или индуктивные (электромагнитное поле). Однако эффективному использованию этих систем чаще всего мешает плохое качество полов. Себастьян Ридмайер (Sebastian Riedmaier), руководитель производственного управления складской и системной техники компании Jungheinrich, говорит, что, когда клиенты компании собираются покупать VNA-штабелеры, их информируют о том, как необходимо выполнить пол на складе согласно немецкому промышленному стандарту DIN 15185. При использовании VNA-штабелера с высотой подъема более 6 м предельно допустимое отклонение поверхности напольного покрытия (на трассе) от горизонтали составляет всего 2,0...2,5 мм на длине 2 м. Чуть большее отклонение полотна проезжей части от горизонтали вызывает заметный наклон выдвинутой мачты. Это ухудшает устойчивость машины, как следствие сказывается на скорости перемещения груза и практически не позволяет максимально использовать технику (скорость движения 12 км/ ч, высота подъема 15 м).
![Узкопроходные штабелеры типа «man-up», сделанные в США: [b]Raymond[/b]](/article/10584-uzkoprohodnye-vysotnye-shtabelery-i-pogruzchiki/Images/04.jpg)
![Узкопроходные штабелеры типа «man-up», сделанные в США: [b]Raymond[/b]](/article/10584-uzkoprohodnye-vysotnye-shtabelery-i-pogruzchiki/Images/03.jpg)
Вместо 10…11 км/ч узкопроходная техника развивает скорость вдвое меньше, а значит, производительность склада снижается. Кроме того, отмечает Ридмайер, поскольку зазор между машиной и стеллажом составляет только 10 см, при неровном напольном покрытии есть вероятность того, что на большой высоте кабина может задеть стеллаж, а это приведет к несчастным случаям. Поэтому на практике перед применением погрузчика в узких проездах пол помещения выполняют особым образом – идеально ровная поверхность достигается при использовании особо прочных наливных покрытий с последующим их шлифованием. Тем не менее, согласно оценкам Ридмайера, «в большинстве случаев максимальная скорость VNA-штабелеров так и не была востребована, очень часто из-за плохих полов они были вынуждены замедлять движение во всех проходах». Среди прочего стандарт DIN 15185 говорит, что стеллажи в проезде под действием груза не должны геометрически отклоняться от первоначального положения, а шахты, каналы или другие полости в полу должны быть устроены с минимальным расстоянием 20 см от возможной трассы движения машины. Подобных сооружений в рабочей аллее нормативы вообще рекомендуют избегать.
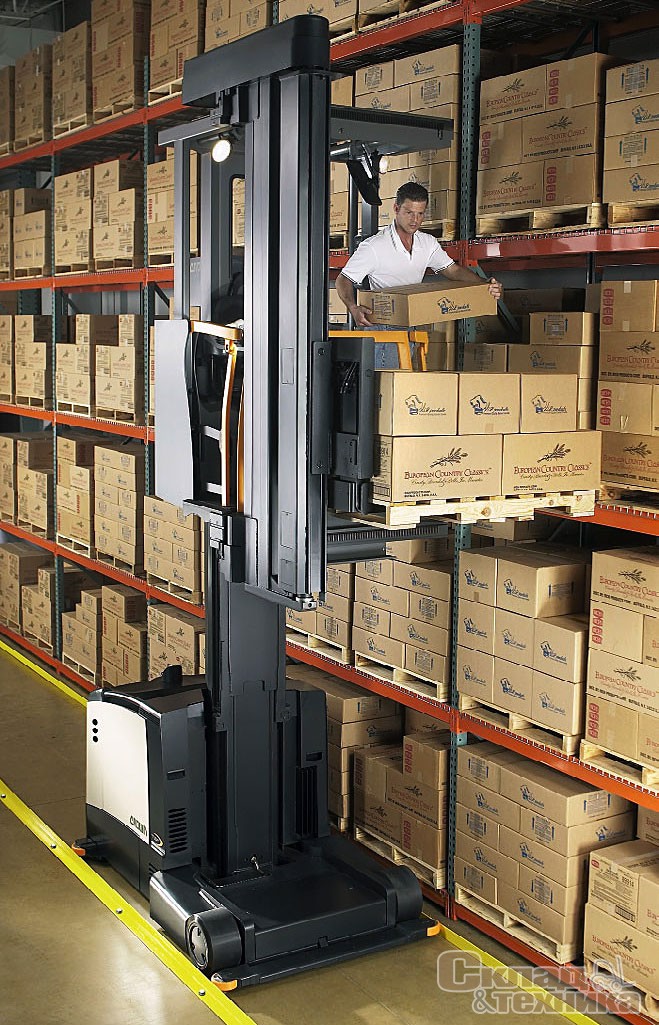
VNA-рынок и новые технические решения
Мировой рынок высотной узкопроходной техники остается пока довольно закрытым: производители напольного транспорта предоставляют данные о своем обороте по разным видам техники в региональные отраслевые ассоциации и союзы, но данные эти конфиденциальные и не публикуются в открытой печати. Тем не менее некоторые качественные оценки более популярного сегмента высотных VNA-штабелеров привести можно.
Прежде всего, как отмечают эксперты рынка, в последнее время сегмент машин «mаn-uр» развивается достаточно активно, тогда как спрос в сегменте «man-down» остается примерно на одном уровне и по общим объемам несколько уступает первому. Основной спрос на европейском рынке приходится на штабелеры с подъемной кабиной и высотой подъема груза менее 10 м: объем производства этих моделей составляет около 80...85% всех выпускаемых узкопроходных машин.
![Узкопроходные штабелеры типа «man-up», сделанные в Европе: [b]Magaziner[/b]](/article/10584-uzkoprohodnye-vysotnye-shtabelery-i-pogruzchiki/Images/12.jpg)
![Узкопроходные штабелеры типа «man-up», сделанные в Европе: [b]Still[/b]](/article/10584-uzkoprohodnye-vysotnye-shtabelery-i-pogruzchiki/Images/13.jpg)
Вряд ли мы ошибемся, если скажем, что в пятерку наиболее крупных поставщиков высотных VNA-штабелеров входят Jungheinrich, Kion Group (узкопроходные высотные штабелеры для трех входящих в группу компаний изготавливает фирма Still), BT, Crown, NACCO (модели марок Hyster и Yale по конструкции практически аналогичны). В Европе популярно также оборудование марок Atlet, Magaziner и Dambach. Последняя компания в нашей стране пока мало известна. Она не была упомянута нами в первой части статьи, и совершенно незаслуженно: до 1998 г. Dambach являлась контрактным производителем таких машин для Jungheinrich, а сама Jungheinrich начала изготавливать высотные VNA-штабелеры самостоятельно только после приобретения фирмы Boss и на ее заводе. В настоящее время Dambach разрабатывает VNA-штабелеры «man-up», а также автоматизированные решения на их основе и краны-штабелеры по индивидуальным заказам. Кроме того, она серийно изготавливает некоторые модели типа «man-up» для Atlet и BT (из серии Vector). В нашей стране оборудование марки Dambach представляет компания «Картрейд». Не так давно она успешно осуществила поставку и монтаж высотного штабелера на склад фармацевтической компании и планирует установить туда еще одну такую же машину.
![Узкопроходные штабелеры типа «man-up», сделанные в Европе: [b]Om[/b]](/article/10584-uzkoprohodnye-vysotnye-shtabelery-i-pogruzchiki/Images/06.jpg)
![Узкопроходные штабелеры типа «man-up», сделанные в Европе: [b]Jungheinrich[/b]](/article/10584-uzkoprohodnye-vysotnye-shtabelery-i-pogruzchiki/Images/07.jpg)
![Узкопроходные штабелеры типа «man-up», сделанные в Европе: [b]Linde[/b]](/article/10584-uzkoprohodnye-vysotnye-shtabelery-i-pogruzchiki/Images/08.jpg)
![Узкопроходные штабелеры типа «man-up», сделанные в Европе: [b]Atlet[/b]](/article/10584-uzkoprohodnye-vysotnye-shtabelery-i-pogruzchiki/Images/09.jpg)
![Узкопроходные штабелеры типа «man-up», сделанные в Европе: [b]BT[/b]](/article/10584-uzkoprohodnye-vysotnye-shtabelery-i-pogruzchiki/Images/10.jpg)
![Узкопроходные штабелеры типа «man-up», сделанные в Европе: [b]Hyster[/b]](/article/10584-uzkoprohodnye-vysotnye-shtabelery-i-pogruzchiki/Images/11.jpg)
Теперь перейдем к новинкам. Готовя эту статью и просматривая зарубежные специализированные издания, к своему удивлению и удовольствию мы обнаружили, что практически обо всех новейших высотных штабелерах в нашем издании так или иначе уже рассказывали. Последним достижениям в этой области – моделям Linde, Hyster C1.0, C1.3 и C1.5, TSP 6000 Crown, Magaziner – были посвящены отдельные статьи, поэтому тех из читателей, кто заинтересован получить более подобную информацию о них, отсылаем к этим номерам журнала. Замечательно, что каждая из моделей при высочайшем уровне совершенства имеет свои «ноу-хау», наборы функций и особенности, отличающие их от аналогов. Однако на двух технических решениях, которые, на наш взгляд, открывают для узкопроходной техники новые возможности, остановимся более подробно.
Параметр | Atlet | BT | Crown | Hyster | Jungheinrich | Magaziner | Still |
---|---|---|---|---|---|---|---|
Тип | DCR 160 | VCE 150A | 1.5 TSP*** | C 1.5 M | EKX 515 | EK 15 | MX-X |
Грузоподъемность, кг | 1600 | 1500 | 1500 | 1500 | 1500 | 1500 | 1500 |
Концепция привода | Переменного тока | Постоянного тока | Постоянного тока | Переменного тока | Переменного тока | Переменного тока | Переменного тока |
Масса, кг | 10 000 | 7600 | 5430 | 5400 | 8083 | 7400 | н. д. |
Высота подъема*, мм | 7500 | 6980 | 6780 | 7990 | 6750 | 6000 | 5050 |
Скорость движения с грузом/ без груза, км/ч | 10,5/ 10,0 | 12,0/ 10,0 | 9,6/ 9,6 | 8,0/ 9,0 | 10,5/ 10,5 | 11,0/ 11,0 | н. д. |
Скорость подъема с грузом/ без груза, м/с | 0,45/ 0,42 | 0,40/ 0,40 | 0,32/ 0,39 | 0,35/ 0,43 | 0,42/ 0,47 | 0,41/ 0,49 | н. д. |
Скорость опускания с грузом/без груза, м/с | 0,45/ 0,45 | 0,40/ 0,40 | 0,41/ 0,41 | 0,40/ 0,40 | 0,40/ 0,40 | 0,40/ 0,40 | н. д. |
Аккумуляторная батарея** | 80 В; 840 А·ч | 48 В; 1200 А·ч | 72 В; 800 А·ч | 80 В; 560 А·ч | 80 В; 840 А·ч | 80 В; 775 А·ч | 80 В; 930 А·ч |
Ширина, мм | 1300 | 1270 | 1320 | 1210 | 1210 | 1200 | 1160 |
**Поставляются батареи и другой емкости.
***Данная модель может поставляться и с батареей 40 В.
Источник: DVZ.
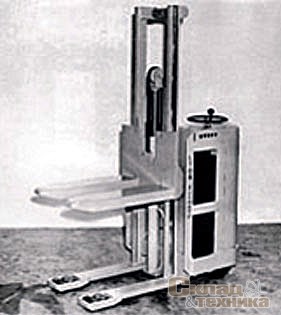
Вероятно, мало кто знает, что изобретателем первого узкопроходного устройства для штабелирования пакетированных грузов был талантливый американский инженер Кристиан Д. Гибсон (Christian D. Gibson). Основатель компании Raymond Corporation Джордж Г. Раймонд-старший (George G. Raymond-Sr.) нанял его на фирму в 1943 г. как первого высокопрофессионального конструктора. Глубокие знания по специальности, накопленный опыт и большой инженерный талант, поддержка Раймонда позволили Гибсону разработать первое узкопроходное устройство для штабелирования поддонов, которое и было изготовлено в Северной Америке в 1949 г.
Концепция машины произвела революцию в технологии складирования: ее применение позволяло значительно сузить межстеллажные проходы и увеличить площади для хранения грузов. В 1951-м Гибсон и Раймонд получили патент на приводное узкопроходное устройство, получившее название модель 700 Spacemaker. К 1953 г. Raymond Corporation произвела уже тысячу этих машин. За 36 лет работы в компании Гибсон продолжал проектировать для нее технику для перемещения и складирования грузов на поддонах и получил более 200 патентов. Талантливый изобретатель ушел из Raymond Corporation в 1983 г., но продолжал сотрудничать с ней в качестве консультанта до тех пор, пока в октябре 2002 г. не переехал в Хьюстон (шт. Техас). Кристиан Гибсон ушел из жизни 22 января 2004 г. в возрасте 89 лет. Коллеги по Raymond Corporation, для которых он был просто Крис, отмечают, что вклад, который изобретатель внес в промышленность производства напольного транспорта, уникален. Как отметил президент и CEO Raymond Corporation Джеймс Дж. Малвазо (James J. Malvaso), «именно его технические идеи сформировали основу для успеха компании и изменили сам ход развития ее коммерческой деятельности в области разработки техники для складирования грузов».
Still: опыт автоматизации высотных стеллажных складов DSV с помощью штабелеров MX-X
В тесной кооперации с компанией DSV, оказывающей услуги в области логистики, фирма Still GmbH (ФРГ) разработала типовой проект автоматизации складов, основой которого впервые стали высотные стеллажные штабелеры типа МХ-Х, работающие без оператора. Об этой новинке мы уже немного рассказывали, ее представили общественности в 2005 г. на Международной выставке по интралогистике CeMAT в Ганновере (ФРГ). Благодаря такой модернизации значительно улучшилась система управления материальными потоками и снизились эксплуатационные расходы на центральном складе гранулированных пластмасс фирмы Generаl Еlеctric Plastics в голландском городе Bergen op Zoom, расположенном между Роттердамом и Антверпеном. Необходимость в таком высоком уровне автоматизации предприятия была вызвана тем, что в Голландии трудно найти временных рабочих и операторов для напольного транспорта, чтобы обеспечить функционирование склада в условиях регулярно возникающих в конце каждого квартала пиковых нагрузок.
Фирма Still GmbH получила задание полностью пересмотреть и оптимизировать схему движения материальных потоков на складе, работающем под управлением логистической компании DSV. Проект оказался очень сложным, так как его реализация не должна была останавливать работу, которая велась круглосуточно и предусматривала одновременную и полную замену всех полов в помещении. Хитроумно организованное взаимодействие между управляемыми операторами фронтальными погрузчиками, полностью автоматическими высотными стеллажными штабелерами и системой управления материальными потоками фирмы Still не только значительно улучшило технологические процессы, но одновременно настолько сократило расходы, что инвестиции в проект стало возможно окупить менее чем за два года.
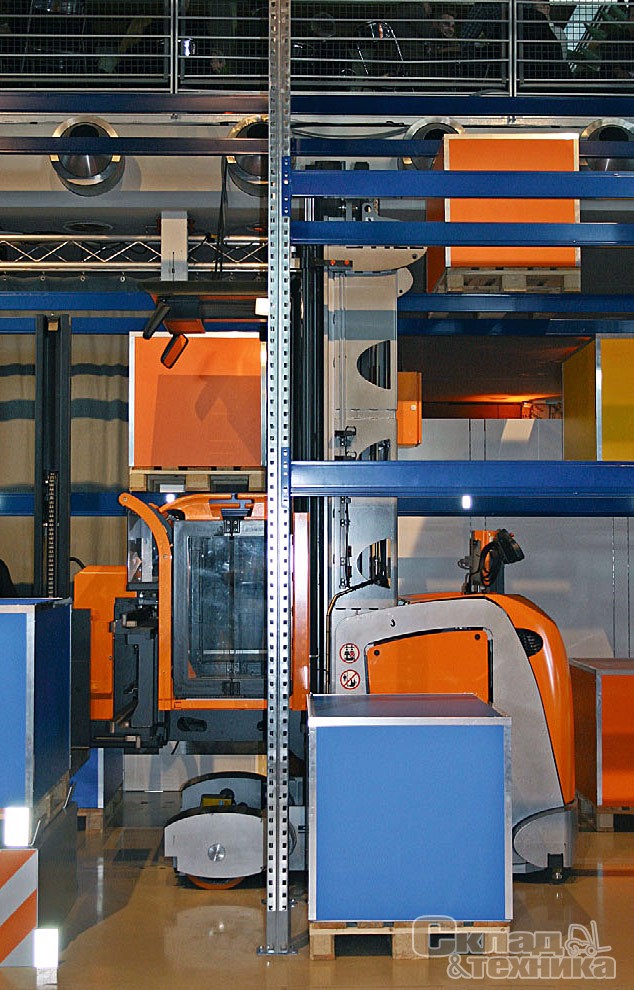
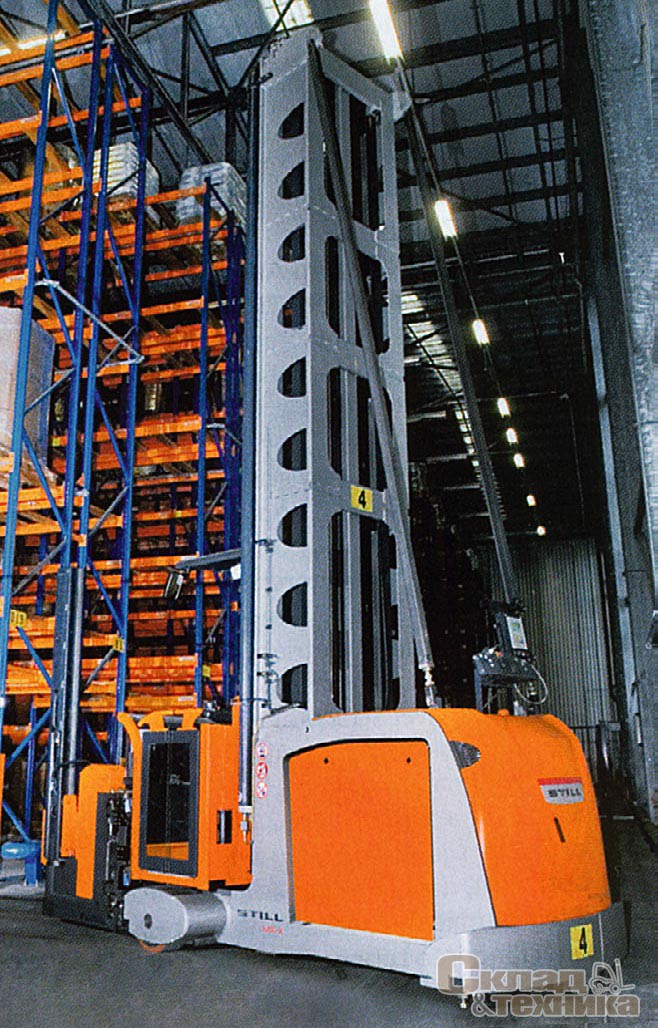
Концерн транспорта и логистики DSV возник в результате объединения компаний DFDS Transроrt (Дания) и Frans-Maas Gruppe (Голландия). Совместная работа с фирмой Still осуществляется с 1989 г., т. е. с момента постройки старого склада, который изначально не предусматривал использование автоматизированного оборудования. Спустя три года здесь была смонтирована первая система направляющих для узкопроходных штабелеров Still, передача информации в которой осуществлялась по индуктивному шлейфу, а в 1995-м все ранее использовавшиеся машины заменили на новые модели Still MX 16. Изучение опыта функционирования первой навигационной системы для штабелеров дало ценный материал для планирования и организации нового склада, проект которого предусматривал 24 аллеи длиной 107 м и 25 тыс. паллето-мест. С помощью четырех автоматизированных высотных стеллажных штабелеров МХ-Х обслуживаются 18 межстеллажных проездов, причем независимо от установленного разделения по зонам все машины по соответствующей команде могут работать также в аллеях, расположенных в непосредственной близости к ним. В остальных шести проездах высотные стеллажные штабелеры управляются операторами вручную, что позволяет складировать в этих зонах поддоны нестандарных размеров, которые часто используются в промышленности производства пластмасс. Автономные модели МХ-Х представляют собой оборудование в стандартной комплектации, которое на определенных участках склада может управляться и вручную. Таким образом, была дополнительно повышена и без того исключительная гибкость склада.
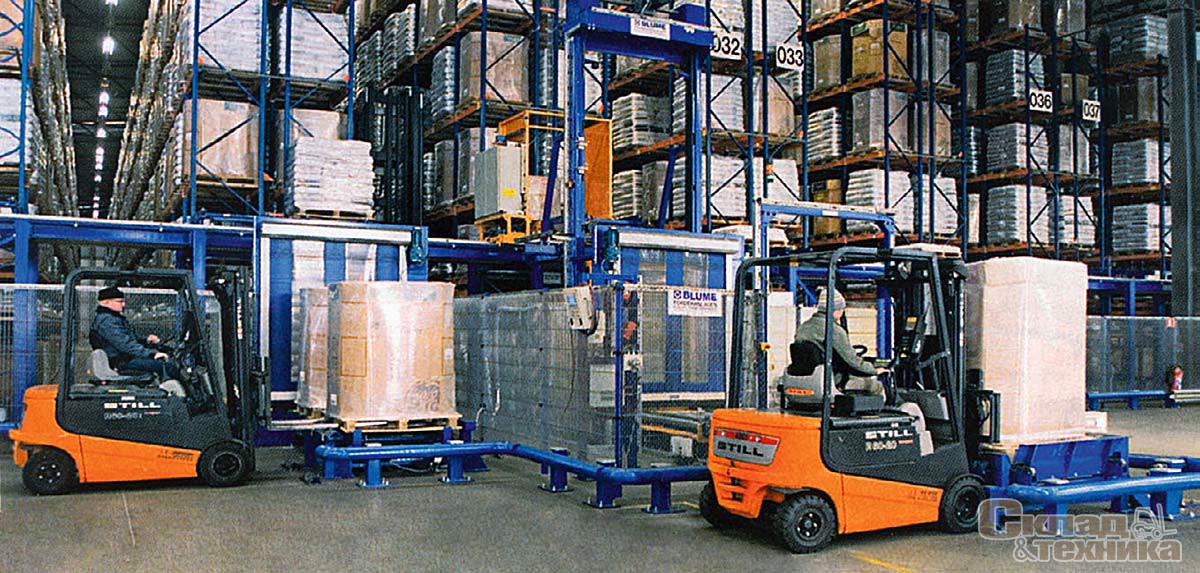
После утверждения концепции проекта в форме бюджетного предложения специалистам Still было поручено составить перечень мероприятий по его реализации. Окончательный заказ, который был составлен на основе этого перечня, поступил в компанию в конце 2003 г. Анализ прежних данных позволил определить, на какие дни и часы работы склада приходятся экстремально пиковые нагрузки. Это привело к решению сначала провести имитационное компьютерное моделирование процессов для определения наиболее узких мест производственной цепочки. В течение всего года склад функционирует непрерывно: семь дней в неделю и 24 часа в день, включая рождественские праздники.
Сотрудники ежедневно работают в три смены. Измеренная производительность склада составила 67 поддонов в час при выгрузке и 47 поддонов в час при загрузке. Разница в цифрах возникла потому, что выгрузка производится только пять дней в неделю, а продукция, изготовленная фирмой GE Plastics, поступает на хранение на протяжении всей недели. Особым требованием при реализации нового проекта было то обстоятельство, что все операции в период реконструкции не должны прерываться. Поэтому перестройка производилась в пять этапов. Работы сильно осложняло и то, что верхний слой пола в помещениях должен был быть удален, так как он не соответствовал высоким механическим нагрузкам и больше не должен был иметь связь с основанием пола. Несмотря на эти трудности за время реконструкции ни один поддон не был отправлен с задержкой или неправильно адресован.
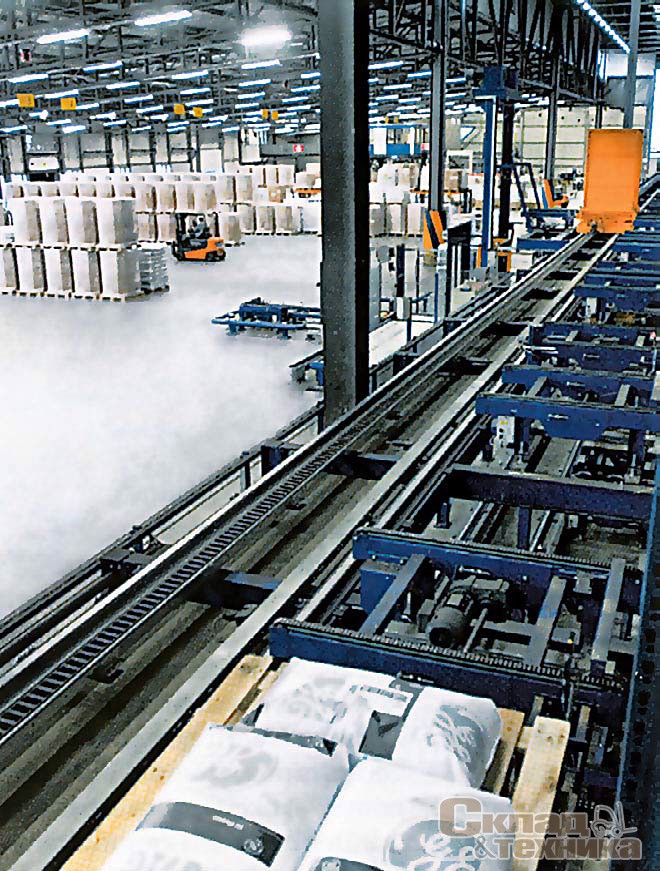
Процесс перевалки грузов на складе делится на три фазы. Разгрузку автомашин и подготовку поддонов осуществляют фронтальными погрузчиками. Передача поддонов на склад производится через станцию, которая контролирует их габариты, а затем поддоны передают на перегрузочные тележки, организованные в два уровня, причем установку паллет на второй уровень обеспечивает промежуточный вертикальный конвейер. Перегрузочные тележки доставляют поддоны к проездам между высотными стеллажами, где работают автоматические штабелеры MX-X. Выгрузка продукции со стеллажей производится в обратной последовательности, причем приоритет в этом случае отдают грузам на нижнем уровне. При такой организации перевалки на складе можно достичь максимального оборота 2565 поддонов/сутки. Проведенное имитационное моделирование показало, что при существующих условиях на складе обрабатывается 1100 поддонов при загрузке и 1600 поддонов при выгрузке, т. е. остается достаточный запас производительности, позволяя обеспечить дополнительные потребности, которые могут возникнуть в будущем.
Кроме того, внедрение проекта позволило сократить 17 рабочих мест, а предприятие стало значительно меньше зависеть от ситуации на рынке труда или уровня заболеваемости сотрудников. Настоящим «сердцем» проекта стало IT-решение компании Still. Эта система управления материальными потоками допускает совершенно разные конфигурации автоматизированного производства, которые в зависимости от потребности могут представлять собой четыре, три, две и даже одну зону. Реализованная система обеспечила очень высокую надежность функционирования склада, а значит, решила главную цель предприятия – своевременность поставок продукции клиентам DSV.
Без сомнения, модернизация склада принесла большую пользу и работникам, и владельцу склада. Во-первых, в проекте использованы существовавшие ранее здание и стеллажи. Во-вторых, благодаря значительно меньшим инвестициям обеспечена быстрая амортизация средств (затраты на принципиально новое решение были бы примерно в шесть раз больше). Значительно увеличились емкость и гибкость склада. Still также выиграла от этого проекта, доказав, что новые разработки фирмы можно реализовать даже в очень сложных условиях, достигнув тем самым более высокого уровня в разработке систем автоматизации складов. С этой точки зрения проект, внедренный в Bergen op Zoom, является отличной рекомендацией для будущих заказчиков подобных систем, но отнюдь не окончанием развития этого автоматизированного решения Still: компания уже разрабатывает новые проекты по автоматизации складов в Гамбурге.
Комбинированный штабелер Jungheinrich ЕКХ 513-515: модульная конструкция и интеллектуальное управление
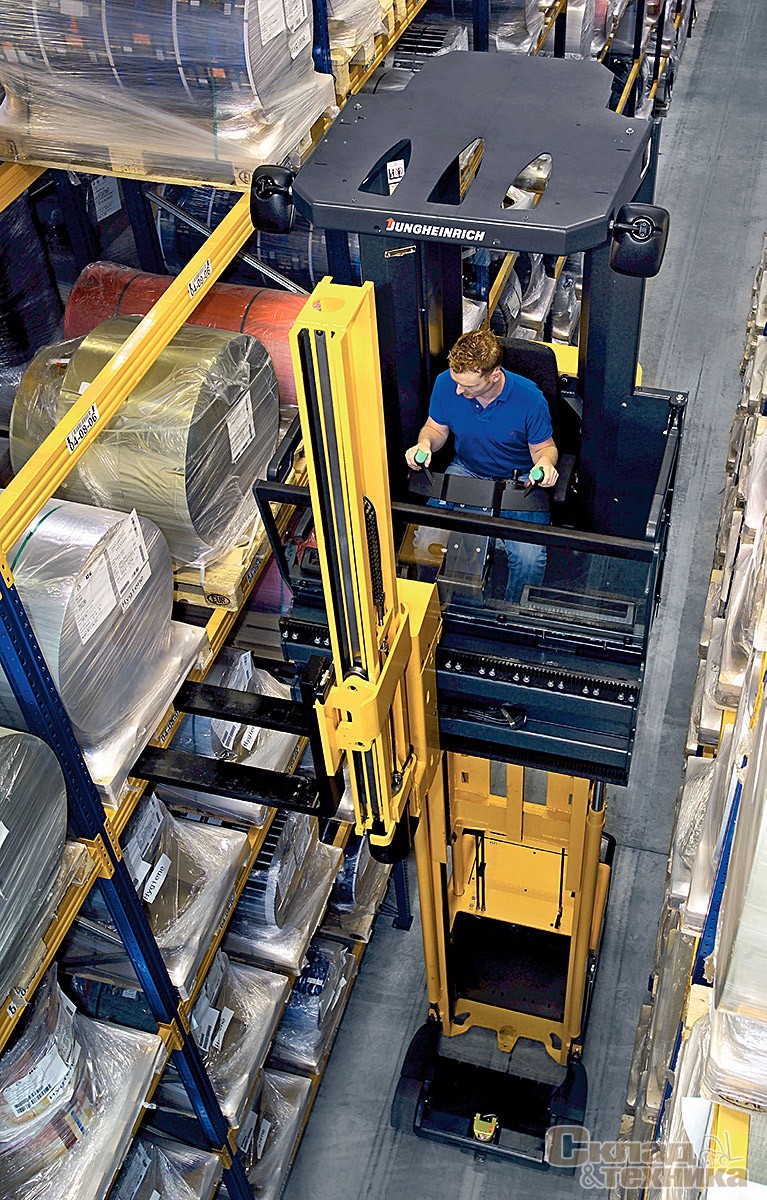
Новый узкопроходный штабелер типа «mаn-uр» ЕКХ 513-515 фирмы Jungheinrich AG был одним из основных претендентов на приз «Лучшее изделие» на Международной выставке по логистике LogiMAT (Штутгарт, март 2007 г.). Приз он не получил, поскольку не было выполнено одно из требований к номинируемым изделиям, а именно критерий «Оправдал себя на практике».
Действительно, поставка на рынок этого нового оборудования с поистине уникальным сочетанием разнообразных функций началась только в мае. Его главной особенностью является наличие системы «интеллектуального управления». Различные модули, например, «RFID-управление» или «Остаточная грузоподъемность плюс» обеспечивают модели такие важнейшие конкурентные преимущества, как высокая скорость, эффективность и безопасность.
Специальная периодическая печать имела возможность ближе познакомить потребителей с новым ЕКХ 513-515 еще в начале февраля 2007 г., когда на специальном заседании Jungheinrich были озвучены важнейшие результаты работ по его созданию. Машина г/п до 1500 кг с высотой подъема чуть более 14 м благодаря электрооборудованию переменного тока напряжением 80 В показывает наивысшую производительность для складов с узкими проездами.
Разработанная фирмой модульная конструкция с многочисленными возможностями конфигураций оправдала себя за годы успешной работы. Она обеспечивает модели ЕКХ очень хорошую способность адаптации и к любым потребностям логистики, и к вариантам применения, которые могут возникнуть в дальнейшем. Интеллектуальный менеджмент с сертифицированным по TU..V электронным управлением и системой СAN-bus обеспечивает новый уровень безопасности оборудования, оставляя его открытым для дальнейшей модернизации в соответствии с будущими требованиями складской логистики. Рабочие модули, функции которых были предварительно согласованы со всеми, даже самыми специфическими требованиями клиентов, обеспечивают ЕКХ 513-515 высокую гибкость в работе. Так, модуль «Топология пола» совместно с RFID-системой контролируют состояние пола в межстеллажном проезде. Для управления подъемно-транспортным оборудованием ставят специальные датчики, постоянно измеряющие его путь.
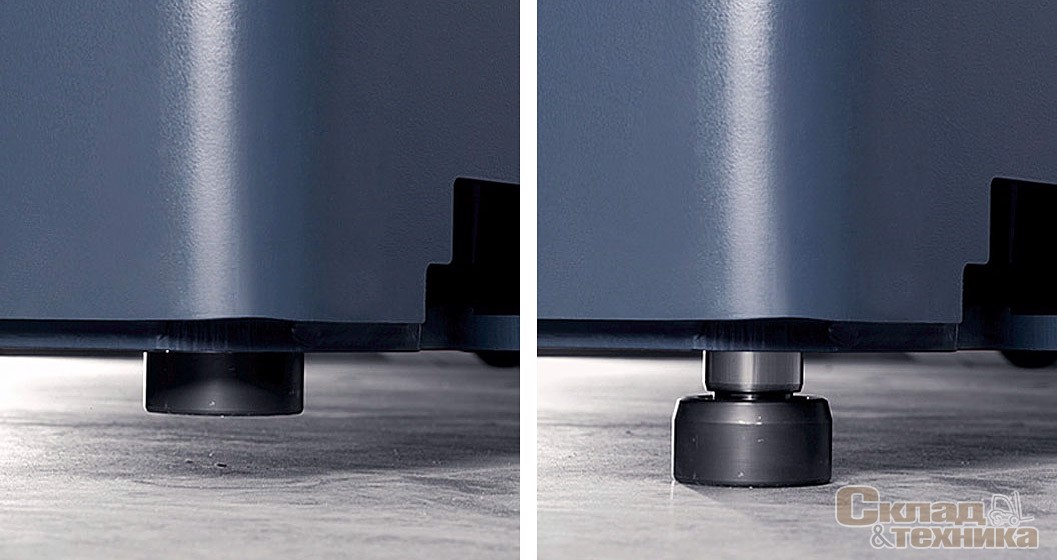
Топология пола и получаемый на ее основе график изменения скорости фиксируются в «памяти» штабелера. Такое решение обеспечивает модели ЕКХ 513-515 очень высокий уровень безопасности выполнения операций, особенно при отключении функций подъема и движения, автоматически снижает скорость на участках с плохим состоянием пола, в конце проезда или при перевозке изделий, требующих особо осторожного обращения. Через USB-порт эту информацию можно передавать от одного транспортного средства любому другому, используемому в аллеях. Наряду с адаптацией скорости с помощью RFID (в идеальном случае новый комбинированный погрузчик развивает скорость до 12 км/ч) имеются и другие варианты увеличения производительности оборудования, например, посредством модуля «Остаточная грузоподъемность плюс», который состоит из двух «активных» опор-стабилизаторов. Автоматически выдвигаясь при выполнении загрузки и выгрузки, они придают штабелеру дополнительную устойчивость и тем самым значительно (до 20%) увеличивают остаточную грузоподъемность. Благодаря модулю «Подъем» можно выбрать нужную скорость подъема груза (до 0,52 м/с) и за счет определения его массы оптимизировать выдвижение и разворот вил.
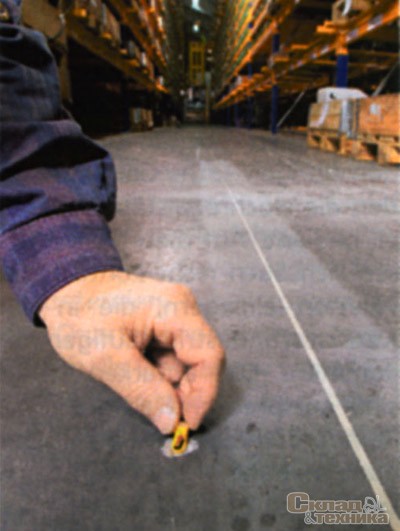
Концерн Jungheinrich известен как один из пионеров в применении техники переменного тока и за последние годы значительно усовершенствовал эту технологию. Его «ноу-хау» в технике привода и управления нашли применение, в частности, в новом комбинированном штабелере. Благодаря мощному, 80 В, приводу переменного тока третьего поколения у ЕКХ 513-515 большая производительность и высокая динамика движений при меньшем расходе энергии. Высокий крутящий момент обеспечивает эффективное ускорение, быстрый подъем, необходимую динамику выполнения вспомогательных движений.
Многие функции, в частности подъем-опускание основной и дополнительной мачт, теперь могут осуществляться одновременно. Новые приводные двигатели переменного тока расходуют до 10% меньше энергии, чем их предшественники. Время работы от одной подзарядки значительно увеличилось за счет рекуперации энергии не только при торможении штабелера, но и при опускании груза. При проведении работ в нормальном темпе время работы модели ЕКХ 513-515 без подзарядки доходит до двух смен. Мощность для каждого конкретного случая применения регулируется таким образом, чтобы исключались пиковые нагрузки на отдельные агрегаты. Наряду с более продолжительным ресурсом расходы на техобслуживание герметичных приводов переменного тока низкие.
Такие важные характеристики оборудования, как эргономика и комфорт, Jungheinrich всегда рассматривал как единое целое, поэтому в модели ЕКХ 513-515 оператору созданы все условия для длительной работы без напряжения и усталости и максимальные удобства. Кабина машины очень просторная, посадка в нее производится через большой проем. Благодаря низко расположенным направляющим разворота и сдвига вил, а также особой конструкции механизма свободного подъема у водителя очень хороший обзор трассы и зоны обработки груза. Чтобы работа меньше утомляла, складное комфортное сиденье выполнено подрессоренным, с регулировками по высоте и по желанию может быть оборудовано обогревом и специальной опорой для позвоночника.
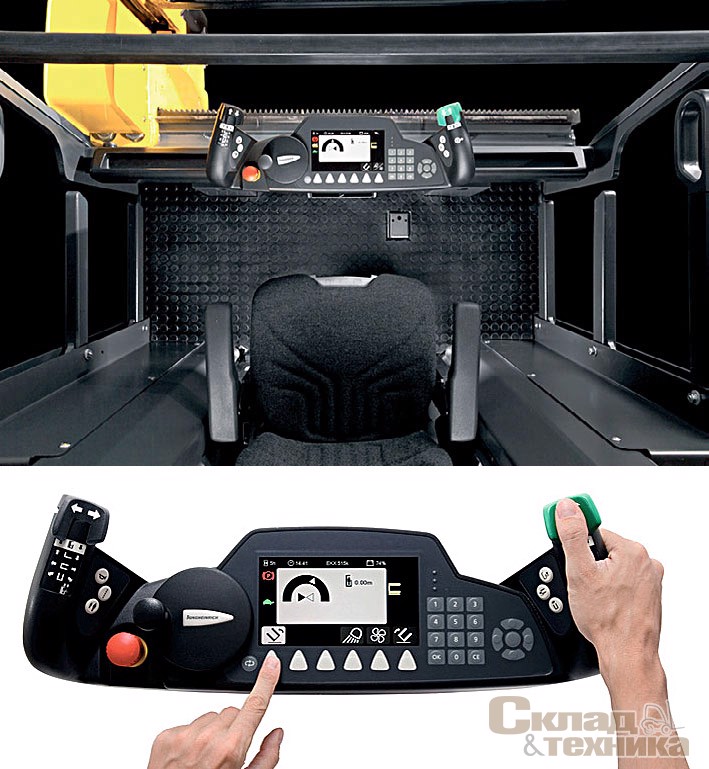
Концепция управления обеими руками без механических переключателей обеспечивает значительно больший комфорт и безопасность. В центре рабочего места располагается пульт управления с цветным дисплеем и сенсорной клавиатурой, на который выводится основная информация о работе машины. Оператор, используя код доступа, может вызвать наиболее подходящую для него программу движения.
Функции машины активируются с помощью сенсорных датчиков, которые регистрируют прикосновения водителя и передают эту информацию в бортовой компьютер. Управление движением и гидравликой производится движениями большого пальца. Встроенная система диагностики обеспечивает эффективный ремонт и обслуживание штабелера. Возможно также дистанционное обслуживание машины через модем.