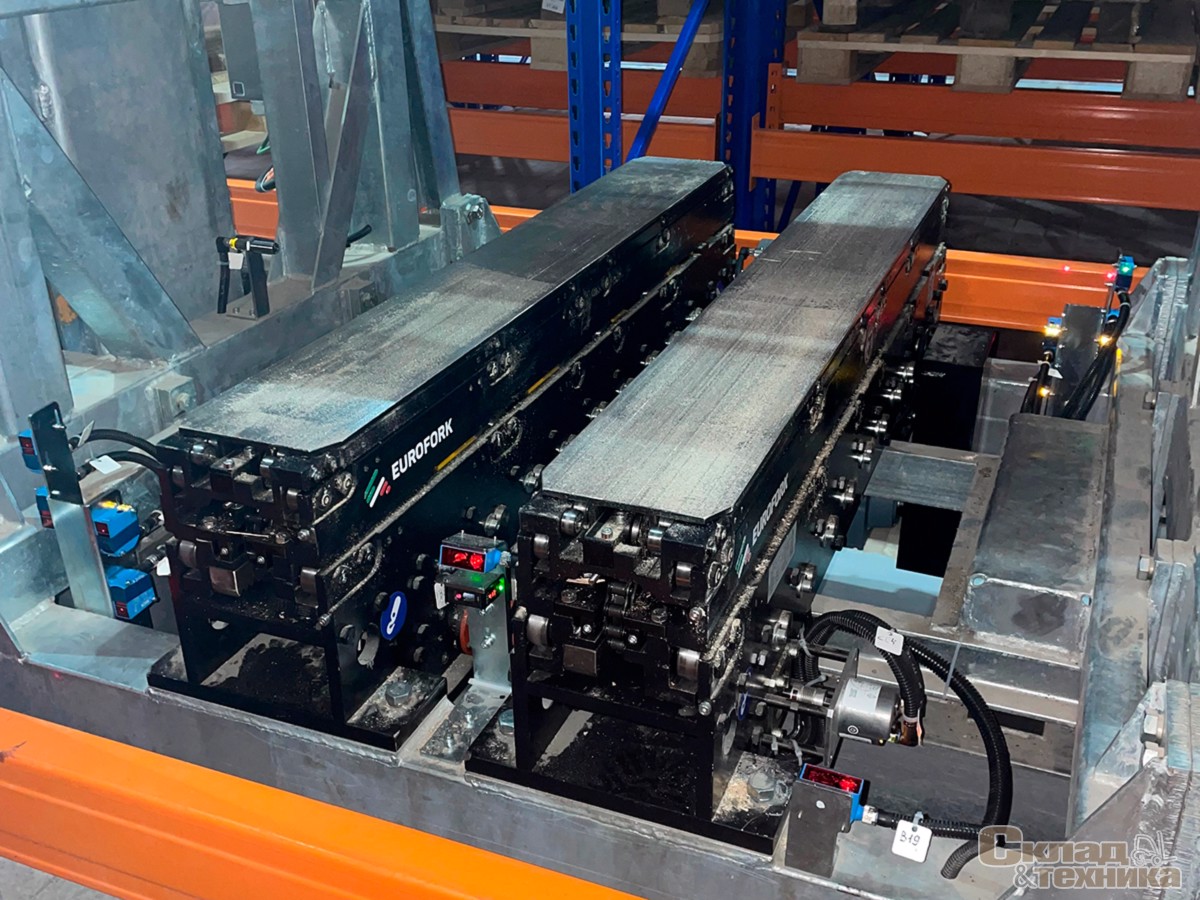
На базе робота штабелёра с технологией Double-Deep
Реализация в проекте: Останкинский мясоперерабатывающий комбинат
Принцип работы ASRS описывается фразой «Товар к человеку» и предполагает полную автоматизацию процесса. Мы хотели разобраться в данной технологии на базе конкретного примера, из нашего опыта, применённого в московской области на одном крупном мясоперерабатывающем комбинате.
От заказчика поступило техническое задание, которое содержало в себе следующие задачи:
- Должна быть максимальная вместимость склада в объемном выражении;
- Размеры используемых паллет 800х1200х и 1000х1200 мм Высотой до 2 метров;
- Масса паллет – от 700 до 1000кг;
- Температура в помещении: -18°С
- Оборот паллет в сутки примерно 450 – 500;
- Приемка паллет осуществляется на 1-м этаже;
- Выгрузка со склада проходит на 0-м этаже;
- Устанавливаемая система должна считывать информацию о продукте с этикетки;
- Интегрировать оборудование с существующей программой 1С;
Компанией АО ПКБ «Техноприбор» в соответствие с поступившим запросом было спроектировано и предложено следующее техническое решение. В качестве основного решения - организовать хранение замороженного мясо сырья по принципу автоматизированного паллетного склада на основе трех роботов-штабелёров с телескопическими захватами (по технологии Double-Deep), позволяющими работать со стеллажами двойной глубины, а также одним штабелером со стандартным захватом (по технологии single-deep). Загрузка паллет в склад и выдача паллет на отгрузку будет производиться на двух уровнях. Все процессы управляются автоматизированной системой класса WMS – LEAD WMS. Идентификация организована с помощью штрих-кодирования.
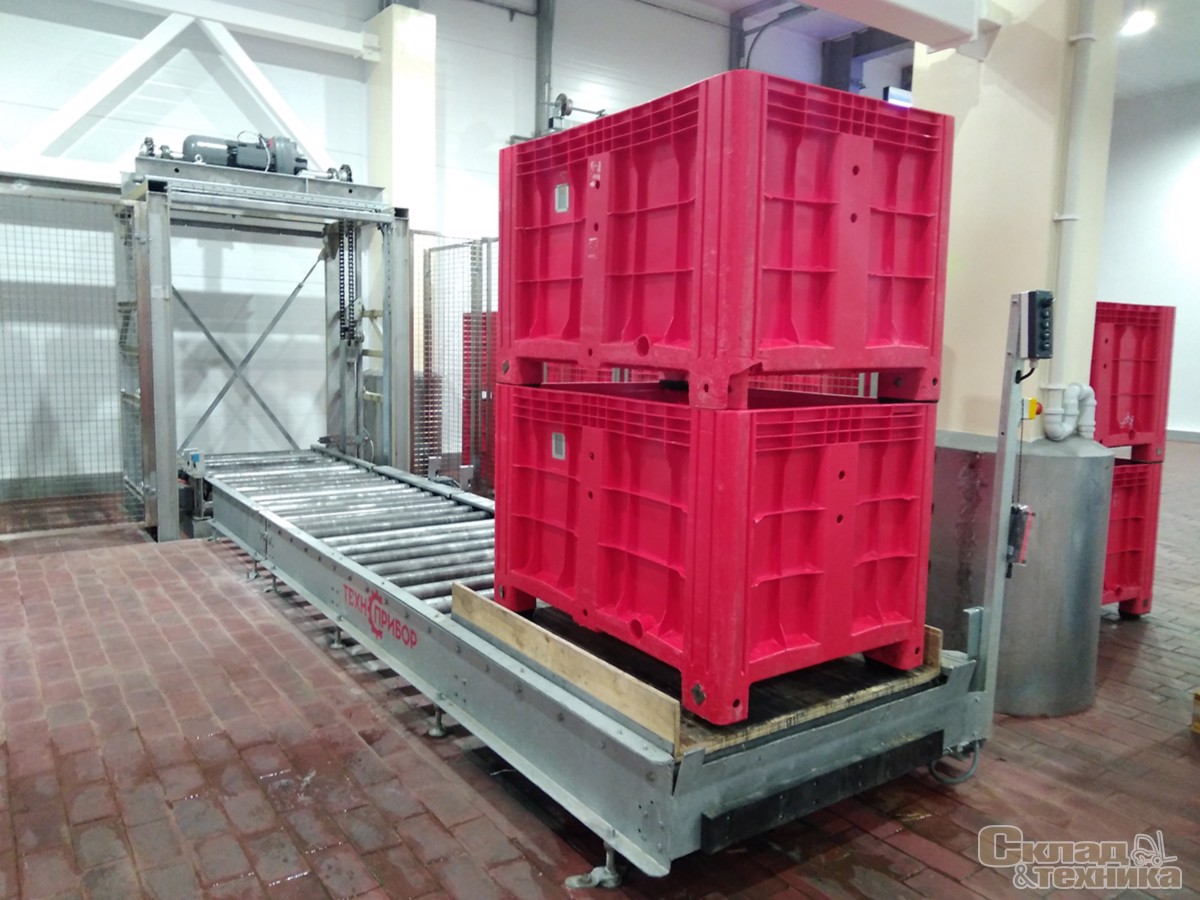
Параметры единиц хранения: деревянные поддоны 800х1200х1700 мм/ 1000х1200х1700мм (включая высоту поддона), вес с продукцией – от 700 до 1000 кг.
Автоматизированная система включает в себя следующее оборудование:
- 3 робота-штабелера с захватами двойной глубины г/п 1000 кг;
- один робот-штабелер со стандартными захватами г/п 1000 кг;
- стеллажную конструкцию из оцинкованной стали на базе фронтальных стеллажей общей емкостью 2340 п/м;
- автоматизированная двухуровневая транспортная система приема/выдачи паллет на базе цепных и роликовых приводных транспортеров;
- два полуавтоматических паллетных подъемника г/п 1000 кг с системой загрузки/выгрузки;
- стеллажи фронтального типа (зона неавтоматизированного склада);
- оборудование системы управления, в т. ч. программное обеспечение верхнего уровня LEAD WMS. 2
В состав оборудования на складе вошли:
- Робот-штабелер со стандартными захватами г/п 1000 кг.
- Штабелер передвигается в меж стеллажном пространстве по верхнему и нижнему направляющим путям, и предназначен для перемещения грузовых единиц из зоны хранения (из ячеек стеллажного блока) в зону приема/выдачи и обратно.
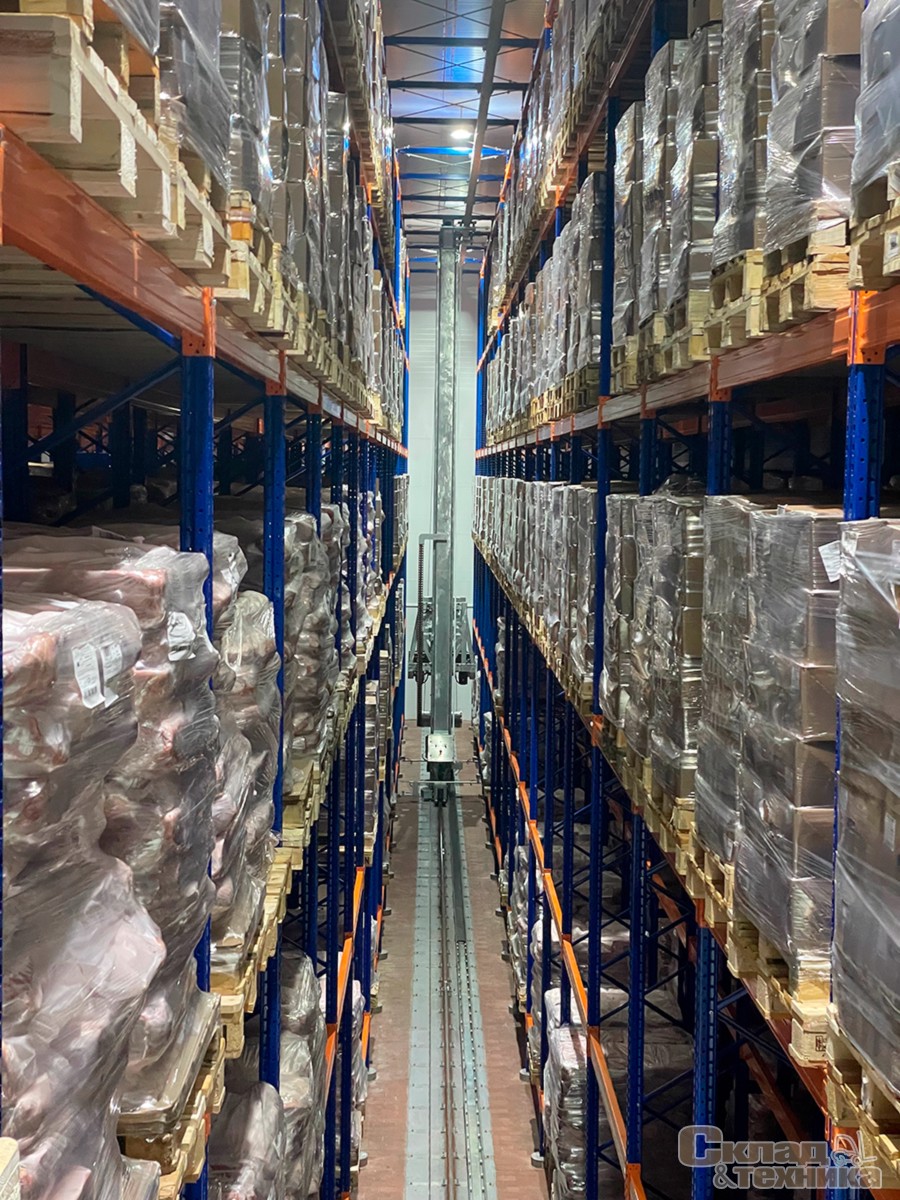
Штабелер имеет современную систему позиционирования на основе энкодеров, блокировки от перегруза, контроль габаритов грузовой единицы, контроль занятости ячейки (установка поддона на занятое место не возможна).
С учетом ограничения помещения по ширине на складе было предусмотрено комбинированное сочетание фронтальных стеллажей с двойной глубиной и одинарного стеллажа.
Масса одной паллеты с сырьем – не более 1 тонны. Высота паллеты с сырьем – не более 1700 мм. Общая емкость хранения в складе – 2340 п\м.
Подача паллет на вход склада и выгрузка со склада осуществляется поводковыми электро-штабелерами.
В зоне загрузки предусмотрены ответвления (роликовые конвейеры) для отбраковки паллет, не прошедших контроль по весо-габаритным параметрам. Далее паллета по конвейерной распределительной системе поступает к назначенному проезду, где ее забирает робот-штабелер.
Отгрузка происходит по запросу из системы 1С, далее WMS обрабатывая запрос предоставляет материал по принципу FIFO, далее робот-штабелер изымает изымает соответствующий материал и передает его на транспортную систему отгрузки, находящуюся на нулевом этаже.
Система умеет выполнять параллельно задания на приемку и отгрузку, так называемый смешанный цикл.
Для перемещения паллет с мясосырьем между этажами предусмотрены два полуавтоматических подъемника с роликовыми столами, и конвейерная система на базе приводных рольгангов для подачи/выдачи паллет.
Управляет работой этого оборудования - Программное обеспечение промышленного уровня LEAD WMS. Которое позволяет управлять трудовыми ресурсами, техникой, производственным оборудованием. А также минимизирует
накладные расходы повышает уровень сервиса, увеличивает производительность склада.
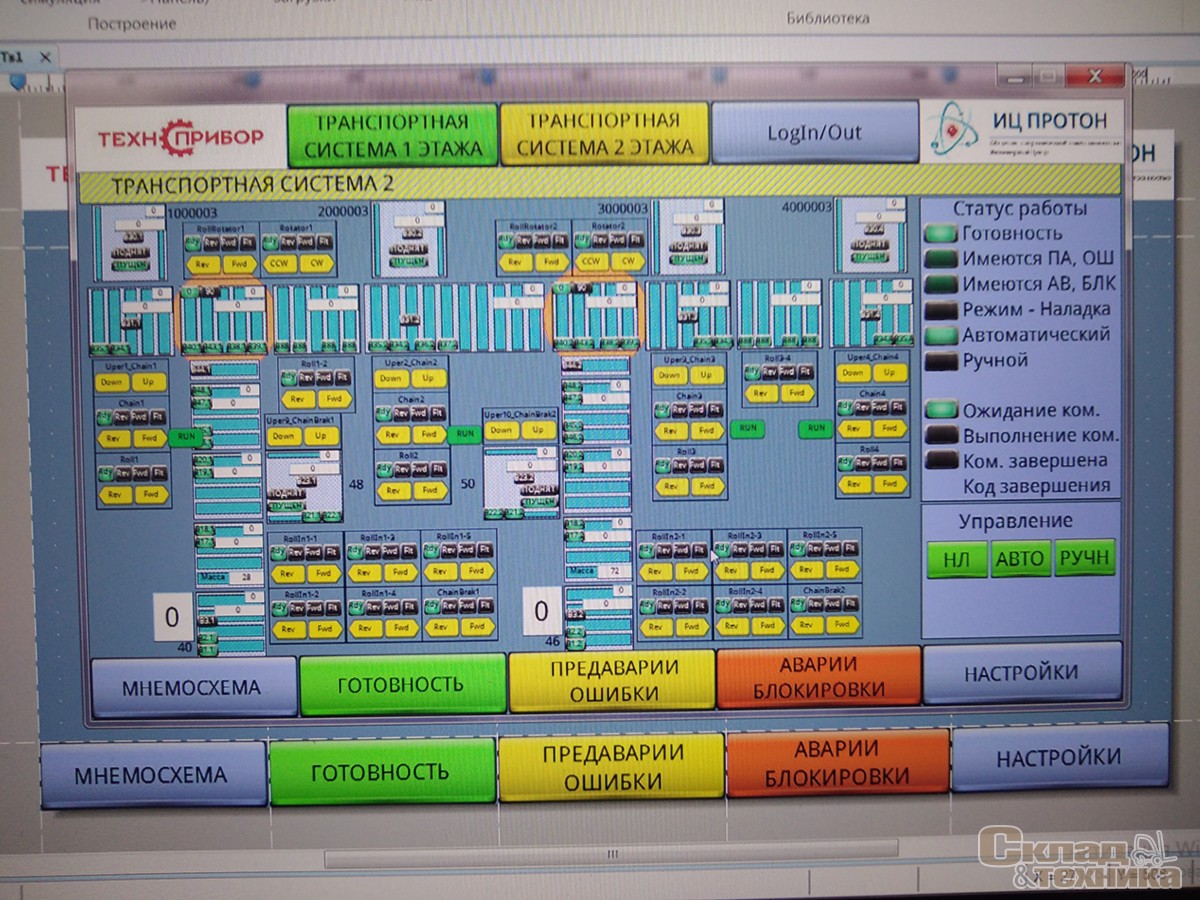
В функционал программы заложено быстродействие, которое позволяет справляется с пиковыми нагрузками на высокоинтенсивных складах. Производительность стандартных процессов или сложные технологические решения – система адаптирована под конкретные требования.
Удобная интеграция с любыми корпоративными системами и специализированным оборудованием: роботами-штабелёрами, автоматизированными шкафами, конвейерами и др.
![]() |
![]() |
Система LEAD WMS позволяет выполнять операции приема и выдачи материала в автоматизированной складской системе хранения с использованием терминалов сбора данных, а именно:
– формирование заказа на размещение;
– вызов ячейки, размещение материала;
– формирование заказа на выдачу;
– вызов ячейки, выдача материала;
– формирование заказа на размещение делового отхода с возможностью указания дополнительных характеристик (вес, размер отхода, применимость).
Система LEAD WMS имеет интеграции с системой 1С. Интеграция обеспечивается стандартными механизмами системы 1С. Предусмотрена возможность дальнейшего масштабирования системы WMS и интеграции с 1С с другими складскими зонами.
В результате реализации проекта по внедрению автоматизированной складской системы (ASRS) на базе робота штабелёра с технологией Double-Deep, Останкинский мясоперерабатывающий комбинат получил:
– максимальную эффективность использования площади складов;
– отсутствие необходимости в инвентаризации, постоянный контроль местоположения грузов;
– полную безопасность для складского персонала — отсутствие операторов в зоне хранения;
– высокую точность и скорость исполнения складских операций;
- и конечно же закрыли все свои задачи, перечисленные в техническом задании.
По мнению экспертов логистической отрасли, за средствами автоматизации будущее складской отрасли, а вот какое именно решение подойдет для вашего бизнеса, подскажут вам профессионалы своего дела, эксперты по интралогистическим решениям из АО ПКБ «Техноприбор».
АО "ПКБ "Техноприбор"
+7 (8352) 37 77 66
|