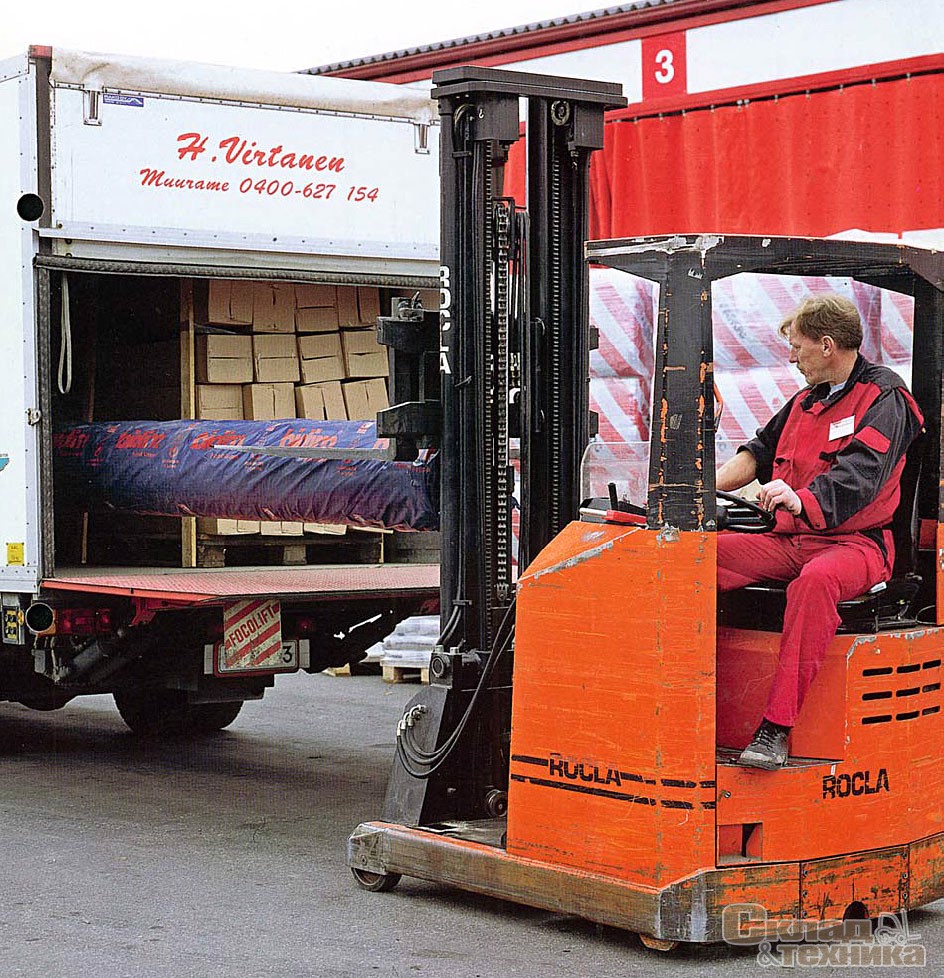
Стандартизация хранения: миф или реальность?
В последнее время все больше говорится о необходимости унификации и последующей стандартизации процессов в различных областях деятельности компаний, относящихся к разным отраслям. Где-то дело уже пошло дальше разговоров – стандартизированы процедуры обмена таможенными документами (проект TEDIM/CUSTCOM), подходы к описанию бизнес-процессов (ISO 9000), ведутся работы по универсализации правил оценки успешности того или иного проекта. Действительно ли существует такая потребность в единых форматах и единых стандартах?
Позволю себе отвлечься и привести простой пример, иллюстрирующий возможные проблемы, возникающие из-за отсутствия универсальных стандартов.
Какие проблемы у российского автомобилиста в Англии? Правильно – все едут не по той стороне и крутят руль, расположенный на том месте, где у нас сидит пассажир. Какие проблемы у автомобилиста из России и Англии на Ямайке? Вы сильно удивитесь, узнав, что на Ямайке право преимущественного проезда у того, чья машина дороже… Зачем я это все это рассказал? Чтобы продемонстрировать, как непросто бывает разобраться в общем-то знакомых вещах (водить машину умеют почти все!) в том случае, когда набор правил не универсален. В этом случае единственное возможное условие безаварийной езды – это услуги регулировщика и наличие у каждого участника движения, как минимум, базовых знаний о специфике движения транспорта в каждом регионе мира.
В рамках данной статьи хотелось бы показать актуальность стремления к универсализации на самом нижнем уровне применяемых в складской логистике процессов и заложить «первый кирпичик» универсальности в фундамент работы одного из складских комплексов.
Начнем с простого и кратко опишем, какими параметрами можно оперировать для определения конкретного места хранения для прибывшего товара, подразумевающего паллетное хранение. Используем для наглядности следующие характеристики поставки.
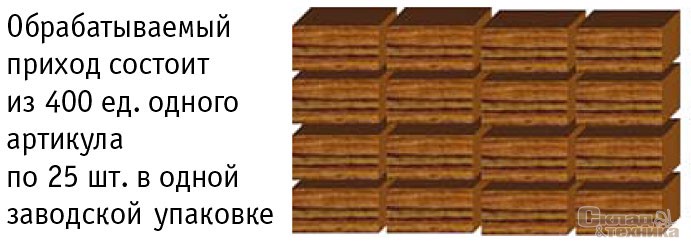
![[b]Грузовые характеристики товара[/b]](/article/10171-standartizatsiya-hraneniya-mif-ili-realnost/Images/02.jpg)
Условия размещения данного товара на складе подразумевают размещение в зоне хранения со следующими характеристиками ячеек.
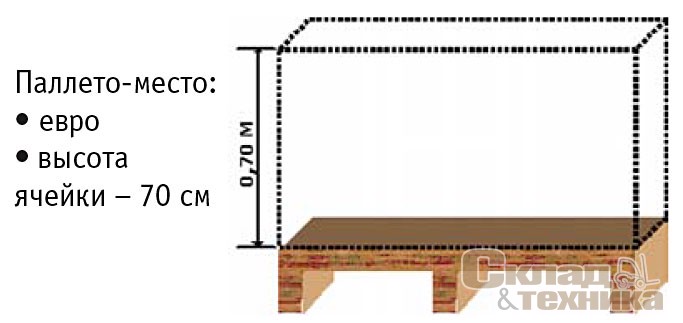
В данном случае система управления складом может предложить нам два варианта размещения прибывшего товара в местах хранения.

Алгоритм определения необходимого для размещения места, приведенный выше, используется во многих системах управления складом и позволяет достаточно эффективно управлять процессом размещения на складе. Но что же будет в том случае, когда при приемке товара необходимо размещать товар не только паллетного хранения, но, например, еще и рулонного? Причем в ситуации, когда в одной ячейке может размещаться несколько рулонов разной номенклатуры, длины и ширины?
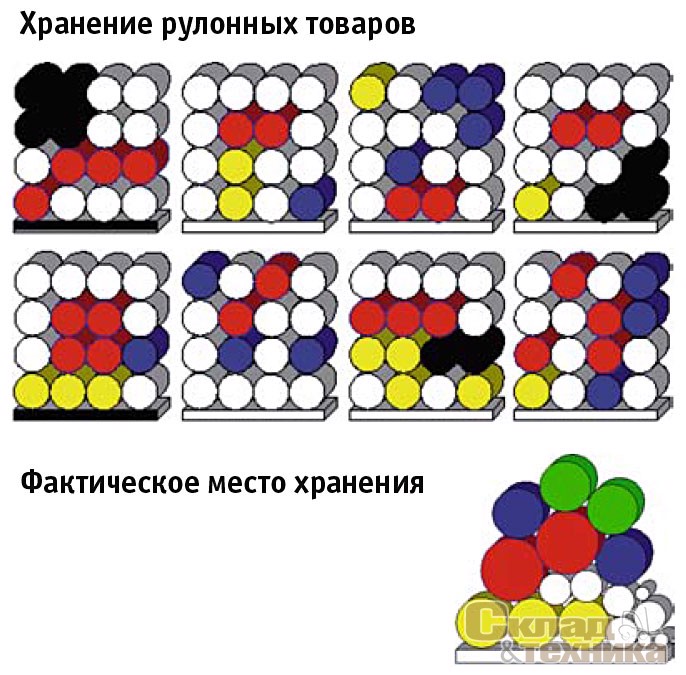
В этом случае можно пойти двумя путями: или разработать собственный алгоритм определения доступных для размещения ячеек хранения, или попытаться унифицировать правила размещения рулонного и паллетного товара. Первый способ приведет либо к необходимости расширить штат за счет появления единицы «строгий регулировщик», либо к необходимости написать достаточно сложные процедуры, на основании которых «регулировщиком» будет становиться каждый сотрудник склада, задействованный в процессе приемки. Нужен ли такой сотрудник на складе? Хотим ли мы доверить управление складскими потоками пусть и квалифицированному, но человеческому ресурсу? По нашему мнению, такой путь далек от оптимального, а поэтому попробуем в качестве руководства к действию все-таки выбрать второй способ.
Очевидно, что при размещении рулонного товара возникают определенные трудности с расчетом занятого и свободного места в ячейке. Это связано с тем, что товар хранится свернутым в рулоны и при размещении в ячейке образуются пустоты между рулонами, которые практически невозможно учесть в случае хранения в одной ячейке и рулонов разного диаметра.
Шаг первый. Представим данные рулоны размотанными и уложенными слоями в ячейку. Поскольку товар, уложенный в рулонах, занимает больший объем по сравнению с тем объемом, который получился бы при размещении того же количества товара слоями, требуется применять некий поправочный коэффициент.
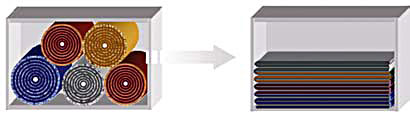
Для целей пересчета разницы размещения размотанного и смотанного рулонного товара было принято решение использовать коэффициент пересчета смотанного рулонного товара Q:
где Тпi – толщина полосы i-го рулона;
Li – длина полосы i-го рулона;
Аяч – ширина ячейки.
Заметим, что для размотанного рулона параметром «количество в слое» из примеров, описывающих размещение паллетного товара, может как раз выступать ширина ячейки, однако для использования данной величины в качестве параметра мы должны разобраться с дополнительным ограничением, накладываемым складской топологией: ячейки, используемые для хранения товаров на складе, имеют различные габаритные характеристики, и величина Аяч , приведенная в формуле, для каждого конкретного места хранения будет разной. В этом случае при переборе возможных мест хранения с целью определения свободного места невозможно использовать для размещаемого рулона постоянной величины параметр «количество в слое».
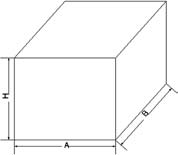
Шаг второй. Одним из способов обхода данного ограничения, связанного с разными габаритными характеристиками мест хранения, является принятие для всех ячеек склада одной приведенной ширины, которая может быть либо выведена на основании наиболее часто встречающихся значений ширины, либо определена, исходя из соображений удобства расчетов, например, 1 м. В этом случае приведенная высота всех ячеек, учитываемая в системе, будет рассчитана как
Таким образом, мы смогли определить значение параметра «количество в слое» для каждого принимаемого на склад рулона, и это значение является постоянной величиной – равной приведенной шириной Асист .
Шаг третий. Вернемся еще раз к размотанным и уложенным слоями рулонам. Для данного «способа размещения» рулона в ячейке параметром «высота слоя» является не что иное, как толщина покрытия размещаемого рулона.
Шаг четвертый. Очевидно, что в любом случае аналогом неделимого кванта из примера с товаром паллетного хранения будет являться длина полосы размещаемого рулона. Таким образом, квант равен длине рулона.
Шаг пятый. Пытаясь провести аналогию между правилами определения свободного места для размещения товаров паллетного хранения и рулонного товара, мы можем зафиксировать следующие подходы к определению ключевых параметров:
Параметр | Паллетное хранение | Рулонные товары |
---|---|---|
Высота слоя | Высота неделимого кванта | Толщина покрытия Тп |
Количество в слое | Число штук товара в одном слое на паллете без нарушения целостности упаковки кванта | Приведенная ширина ячейки Асист |
Неделимый квант | Количество товара в одной упаковке | Длина полосы рулона L |
Паллето-место | Тип паллеты (евро, финская) | Приведенная ширина ячейки Асист |
Высота ячейки | Приведенная высота ячейки Hсист |
При расчете доступной высоты ячейки учитывают такие параметры, как:
- заполненная высота ячейки – это высота, которую занимают рулоны, находящиеся в данной ячейке;
- зарезервированная высота – это высота, которая зарезервирована системой под планируемое размещение в нее рулонов в процессе выполнения приемки или перемещения;
- технологический зазор – минимально допустимая незаполненная высота ячейки, которая учитывает прогиб рулона и необходима для свободного размещения и извлечения рулона из ячейки. Параметры технологического зазора и коэффициента пересчета были вынесены в форму «зона хранения» для их свободной корректировки при необходимости.
В результате решения задачи выделения ячеек система находит множество ячеек, подходящих для размещения товара в требуемом количестве. Доступная высота ячейки рассчитывается каждый раз при рассмотрении этой ячейки в качестве кандидата для размещения в ней товара.
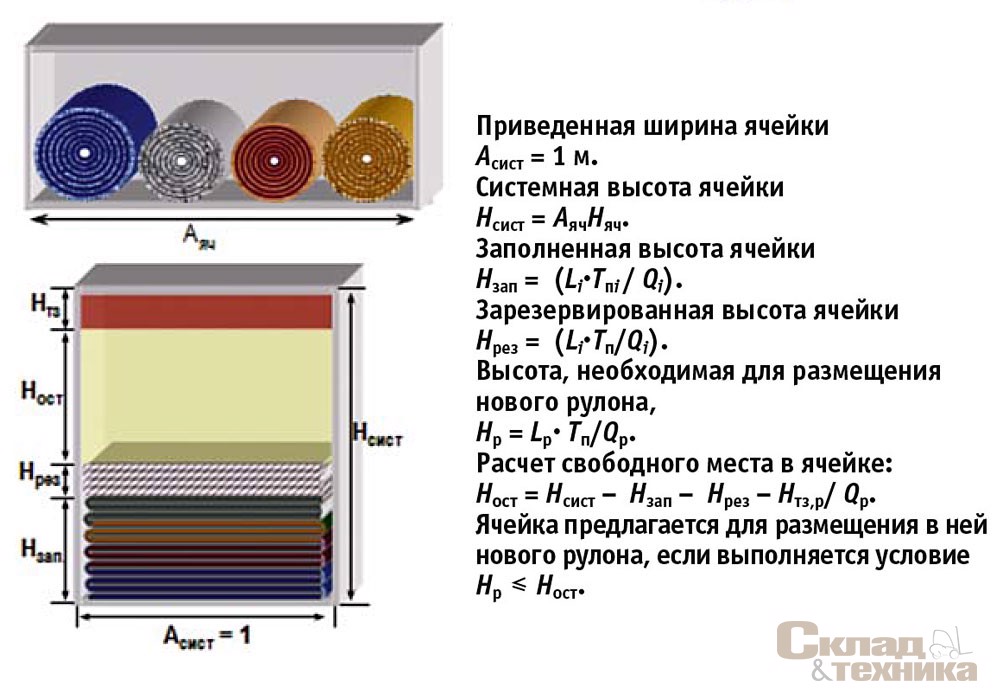
Шаг шестой, заключительный. Внимательный читатель скорее всего уже задается вопросом – каким же образом можно получить значение поправочного коэффициента Q? Вариантов, как всегда, несколько – это и математическое моделирование, и усреднение габаритных характеристик остатков, и, конечно, практический эксперимент. Один из этих способов представлен на рисунке.
Используемые в данном случае значения Q находятся в диапазоне 0,55…0,71.
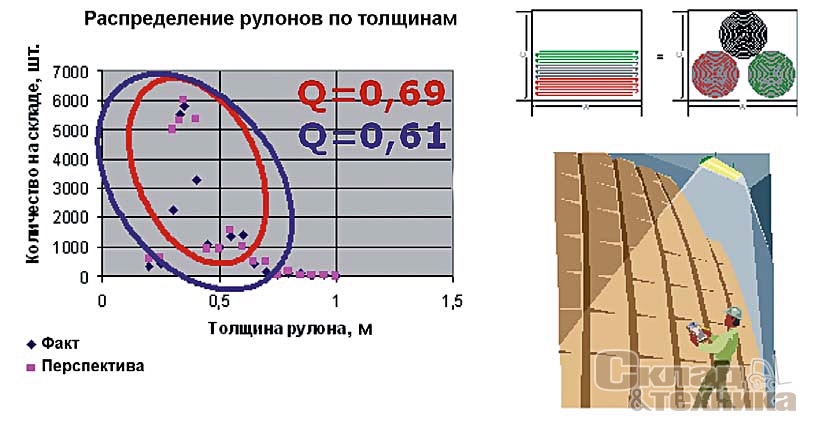
Подводя итог, можно утверждать, что, используя данный подход, мы добились унификации правил размещения товаров с разными габаритными характеристиками в рамках одной системы и одного набора сотрудников, обеспечивающих данное размещение. Достоинства этой методики трудно переоценить. Помимо решения основной задачи, стоящей во время каждого проекта по автоматизации склада, – максимально эффективно использовать складское пространство, этот подход позволил безболезненно решить проблему потребности в «регулировщике», сформулированную нами в начале статьи.
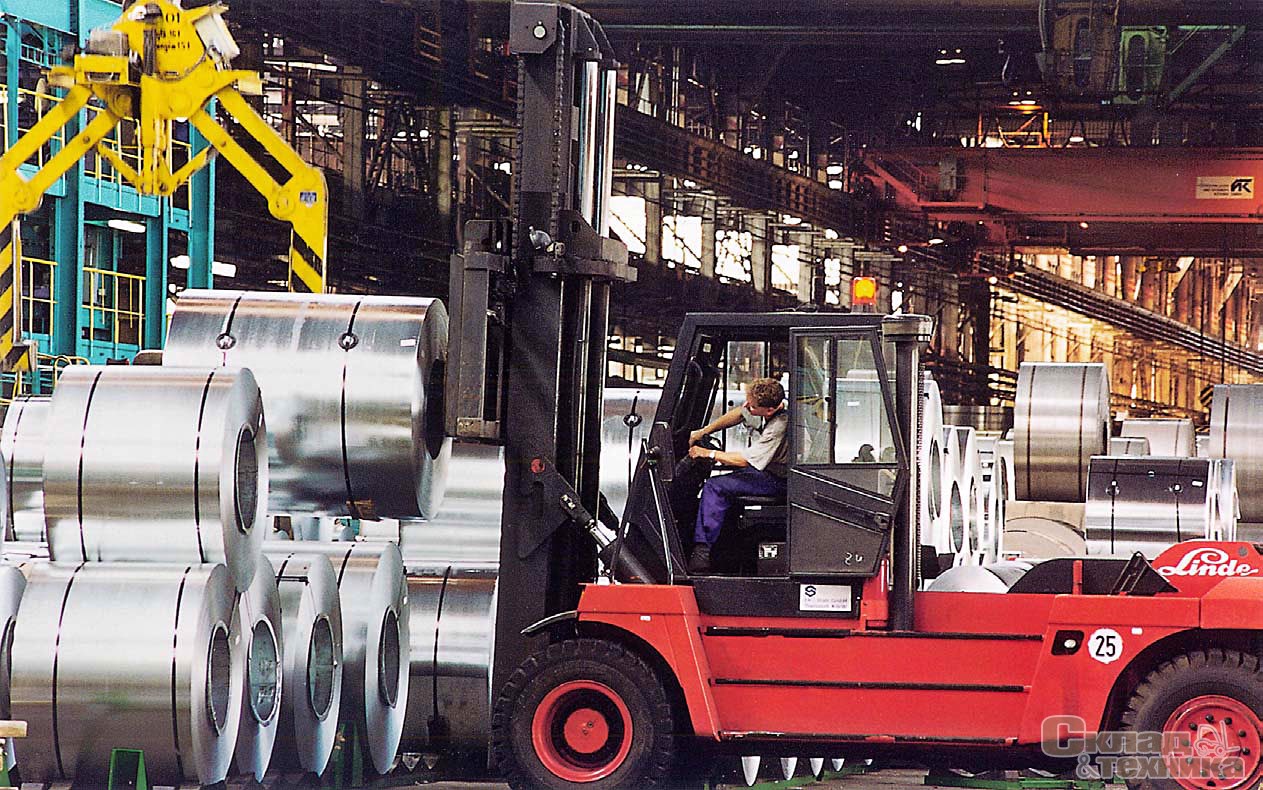