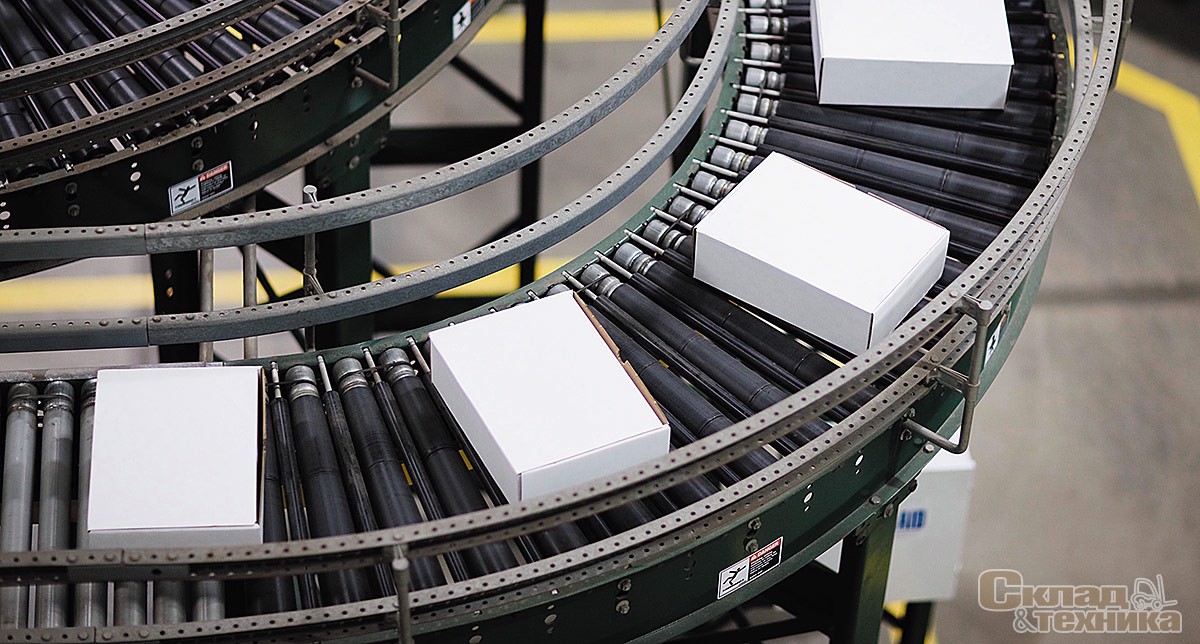
LEAD WMS
Cовременные технологии автоматизации складских комплексов
Информационные технологии завоевывают все большую популярность в России и в мире, становясь практически неотъемлемой частью любого бизнеса. Связано это прежде всего с тем, что на протяжении последних лет в развитии индустрии высоких технологий произошли революционные изменения. Уже сегодня решения в этой области способны поднять на новый уровень эффективность любых предприятий, начиная от небольших компаний и заканчивая крупнейшими мировыми корпорациями, работающими в различных отраслях, в том числе и в логистике.
Если говорить о России, то сегодня практически все торговые и производственные компании, которые имеют собственные складские площадки, а также поставщики услуг ответственного хранения уделяют большое внимание эффективности своей работы, сокращению издержек и повышению конкурентоспособности. Для достижения целей все чаще применяются современные решения, одним из которых являются автоматизированные системы управления складом, или сокращенно WMS (Warehouse Management System).
Что такое WMS?
WMS представляют собой информационные решения, которые можно разделить на две базовые категории – системы основного и детального планирования и системы контроля исполнения.
Одним из важнейших факторов успешной работы складского комплекса является соблюдение разработанной технологии и слаженная деятельность всех участников процесса от момента поступления грузов на склад до их отгрузки. Как раз эту задачу и позволяет решить система управления складом. WMS, являясь классической системой уровня контроля исполнения, стала эффективным инструментом, который даже в своем базовом функционале позволяет добиться ощутимых и впечатляющих результатов.
К примеру, применение системы управления на складском комплексе компании «Велес Групп», дистрибьютора продуктов питания и напитков в г. Чехове Московской области, привело к увеличению производительности его работы на 22% в сравнении с ранее существующими показателями. В ходе проекта была внедрена российская система управления складом LEAD WMS компании LogistiX.
«Даже с учетом того, что мы запустили LEAD WMS в первую же неделю сезона пиковых нагрузок, мы сразу получили увеличение производительности на 5% практически на всех операциях. В результате пропускная способность склада выросла на 22%, а на отдельных операциях мы получили многократное увеличение производительности», – сообщил Юрий Сырцов, директор по логистике компании «Велес-Групп».
Процесс | Среднее увеличение производительности, % |
---|---|
Приемка | 70 |
Размещение грузов с помощью подъемно-транспортного оборудования | 25 |
Размещение грузов с ручной выкладкой на полки | 40 |
Набор упаковок | 30 |
Набор штук | 200 |
Что касается увеличения пропускной способности складских комплексов, то WMS-системы также способны сыграть немаловажную роль в решении этого вопроса. В России и странах СНГ уже есть конкретные примеры, когда применение подобных решений позволило увеличить пропускную способность складов в два раза. К ним можно отнести одного из крупнейших в Казахстане дистрибьюторов фармацевтической продукции компанию «Аманат» и группу компаний «Рогнеда», одного из лидеров в России по производству материалов для строительства и ремонта. В результате применения систем LEAD WMS пропускная способность комплексов выросла на 50% по отношению к ранее существующим показателям.
На складах разной площади и сферы деятельности, где LEAD WMS используется на протяжении нескольких лет, повышение эффективности при выполнении отдельных операций также составляет от 25 до 200%, как показано в таблице.
Кроме того, как отметил Дмитрий Блинов, технический директор компании LogistiX, на одном из проектов была сформирована независимая комиссия, которая установила, что на приемку грузов без использования средств автоматической идентификации и системы управления складом у кладовщика уходило 2,5 ч, а с использованием радиотерминала и WMS – менее 50 мин. Таким образом, скорость выполнения данной операции возросла более чем на 35%.
Внедрение системы управления складом обычно производится параллельно с внедрением технологий автоматической идентификации, что подразумевает возможность использования каких-либо меток (радиометки, штрихкоды) для обеспечения возможности автоматического определения свойств груза. Чаще всего применяется технология штрихового кодирования, что обусловлено низкой стоимостью оборудования и расходных материалов (этикеток), хотя очевидно, что использование радиометок намного более перспективно, но пока мало распространено из-за их относительно высокой стоимости и некоторых особенностей, ограничивающих применение технологии RFID для определенных групп товаров.
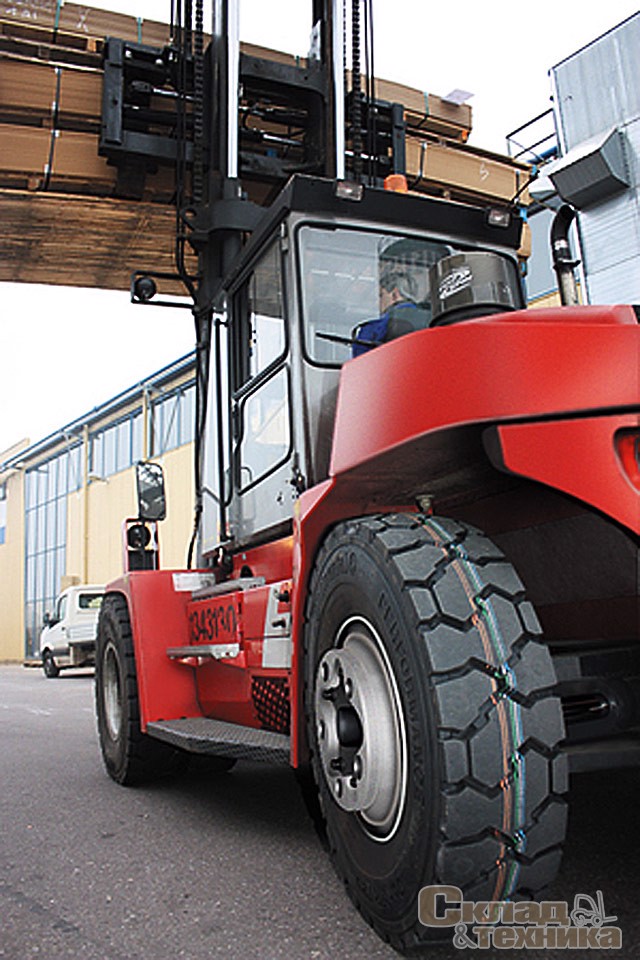
Несмотря на тот факт, что уже использование только базовых функций WMS может дать существенный результат, функции профессиональной системы управления позволяют увеличить эффект от ее использования еще в несколько раз. Применение механизмов сбора и анализа статистической информации, использование разных технологий для выполнения различных операций, а также учет имеющихся ограничений при оперативном планировании и распределении заданий дают возможность выстроить задания в наиболее оптимальной последовательности и обеспечить эффективную загрузку имеющегося ресурса. Фактически возможности современной профессиональной WMS позволяют ей адаптироваться под изменяющиеся условия работы складского комплекса. Наиболее важным инструментом для настройки в этом случае является гибкая система правил, позволяющая формировать перечни условий, при выполнении которых с грузами совершаются определенные действия. Особое внимание следует обратить на используемые алгоритмы: наиболее зрелые и функциональные системы предлагают не только простую «арифметику», но и дают возможность быстро решать N-полные задачи (задачи перебора). Например, при штучном наборе, когда один человек может собирать несколько заказов в несколько единиц тары, LEAD WMS не только планирует, в какие типоразмеры тары будут собраны требуемые товары, но и подбирает наиболее оптимальную их комбинацию, что обеспечивается блоком планирования конфигураций оборудования.
Если говорить об архитектуре решений, то независимо от способа реализации тех или иных механизмов ее все равно можно свести к трехзвенной либо N-звенной, так как производители программного обеспечения все больше обращают внимание на SOA (Service-Oriented Architecture – сервис-ориентированная архитектура) и стараются применять эту технологию если не для распределения функционала, то для обеспечения большей гибкости при интеграции с различным оборудованием и внешним ПО. Основными компонентами WMS являются следующие.
1. Клиентская часть, которая работает на радиотерминалах, – ее можно отнести к мобильным автоматизированным рабочим местам (АРМ).
2. Мобильные АРМ участников рабочего процесса (передвижные тележки с весами, мобильные модули сортировки и распределения грузов и т. п.).
3. Стационарные АРМ участников рабочего процесса (операторы, контролеры, сотрудники зоны фасовки и т. п.).
4. Сервер приложений, который иногда может быть объединен на уровне используемой платформы с сервером управления базами данных.
5. Сервер управления базами данных.
Если говорить о пунктах 4 и 5, то на примере одного из несомненных лидеров рынка – продукта Microsoft SQL Server – можно отметить, что CLR integration, которая присутствует с версии 2005, фактически обеспечивает возможность интеграции средств СУБД и сервера приложений.
Принцип работы WMS
Обязательной частью любой WMS является работа с адресованным пространством, где каждая ячейка имеет ряд свойств, позволяющих системе принять решение о возможности ее использования в каких-либо процессах. Возможностей и вариантов адресации довольно много, и только об этом можно написать отдельную книгу. В самом простом варианте можно выделить три типа адресации мест: адресация палетных ячеек, полок и штабельного пространства. Каждая ячейка при этом получает свой код, идентификация которого (сканирование, произнесение контрольных цифр и т. п.) дает системе управления понять, что контакт исполнителя с конкретным местом состоялся. Как раз этот функционал и является одним из наиболее важных с точки зрения контроля исполнения, так как позволяет оценить производительность исполнителей не только на операциях грузоперевалки, но и при перемещениях, что на больших складах является очень актуальной задачей.
Адресное пространство, состоящее из ячеек, может быть объединено в зоны различного типа и в результате представляет из себя актуальную информационную карту склада, которая будет использоваться для всех внутрискладских операций, начиная с адресного хранения и заканчивая определением текущего местоположения сотрудников. На этом же этапе имеется возможность распределить сотрудников в соответствии с их сферами ответственности, а также описать различные типы сервисных ячеек, используемых для временного хранения или перемещения грузов.
Технологические процессы склада описываются с помощью настроек WMS. При этом, чем более гибкая система настроек предусмотрена, тем больше возможностей получает пользователь. К примеру, системы, обладающие возможностью настройки правил без программирования, как LEAD WMS, позволяют определять условия не только на уровне стандартных атрибутов, но и вводить собственные атрибуты, которые включаются в бизнес-логику. Тем не менее, несмотря на механизмы настройки, наличие хотя бы частично открытого кода является серьезным преимуществом, так как дает возможность поддержки и дальнейшего развития решения не только силами его производителя, но и пользователя.
Каждый исполнитель получает собственный идентификатор, который наносится (в большинстве случаев) на личную карточку в виде штрихкода и сканируется в начале работы с помощью мобильного радиотерминала, которым оснащается каждый сотрудник склада, получающий указания от WMS. Именно использование радиотерминалов позволяет осуществлять управление ресурсами и фиксировать все действия в привязке к шкале времени. Чаще всего радиотерминалы работают в управляемом режиме, получая указания от сервера и находясь с ним на постоянной связи.
При поступлении на склад продукции WMS распределяет места для ее хранения с учетом всех необходимых требований. В частности, учитываются сроки годности, температурный режим, правила совместимости разных товарных категорий и многие другие параметры. Также система управления складом с учетом внесенной ранее информации (топологии склада, параметров оборудования, правил работы и т. п.) самостоятельно формирует поэтапные задания для сотрудников склада, отправляя задачи на радиотерминалы. Таким образом, минимизируется влияние человеческого фактора и вероятность совершения ошибок, повышается точность выполнения задач. Кроме того, система формирует оптимальные маршруты передвижения погрузо-разгрузочного оборудования, что позволяет сократить их холостой пробег и тем самым уменьшить издержки на выполнение операций.
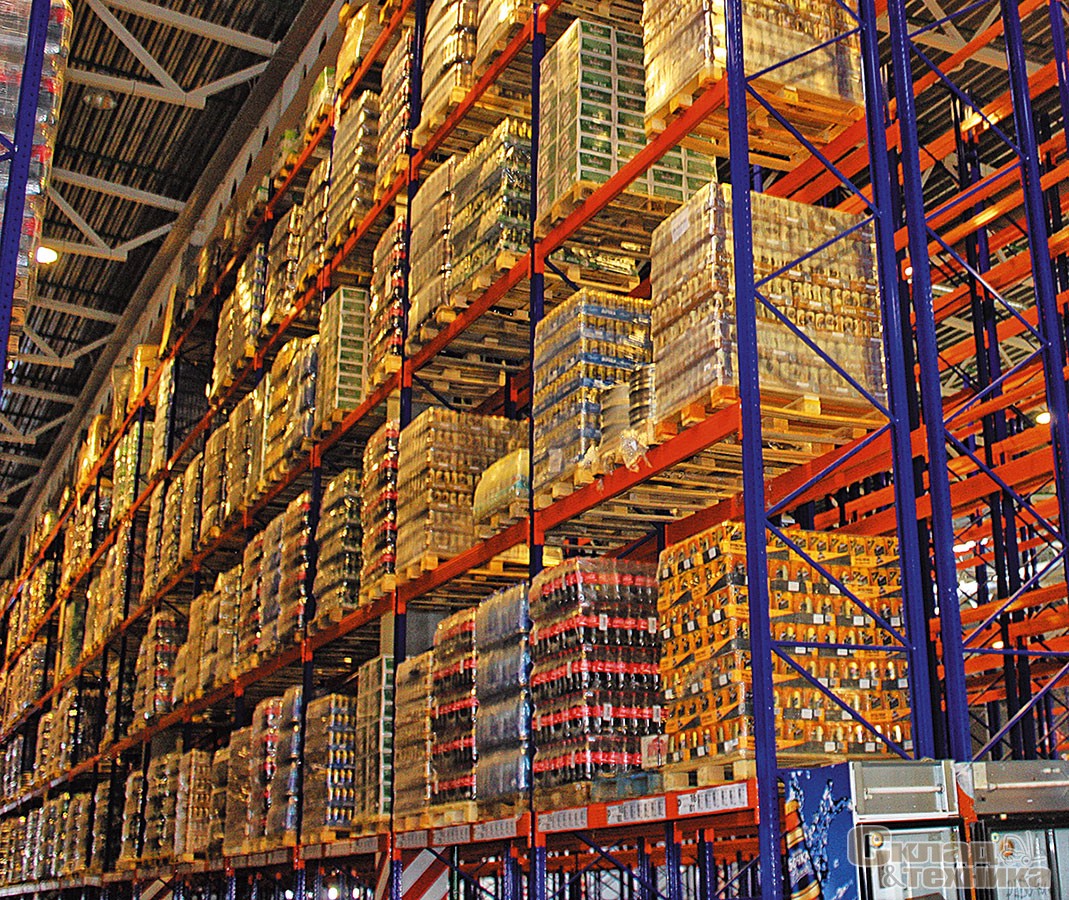
В чем разница?
В настоящее время отечественный рынок располагает множеством систем управления складом с различным ценовым и функциональным уровнем: по оценкам экспертов, в России представлено более 40 их разновидностей. Все решения по управлению складом традиционно делятся на три основных типа: имеющие стандартный набор определенных функций «коробочные» системы, адаптируемые и заказные WMS.
Коробочные системы представляют собой программные продукты, полностью готовые к процессу внедрения за счет определенного объема уже готового функционала. Основные их минусы заключаются в ограничении вариаций настроек, а также в невозможности оценки их использования с точки зрения дальнейшего масштабирования. Возможно, второй недостаток не является таковым для предприятия, которое, приобретая подобную WMS, собирается в последующем заменить на другую, но возможные риски, связанные с переходом с одной системы на другую, включают в себя и несовместимость с точки зрения системы настроек и правил, что потребует внедрять новое решение «с нуля». В качестве резюме можно сказать, что коробочные системы подходят небольшим организациям для автоматизации складов со стандартными и простыми бизнес-процессами.
Адаптируемые системы управления складом сегодня наиболее востребованы как в России, так и за рубежом. Подобные решения эффективны уже не только для небольших компаний, но также для средних и крупных предприятий, где имеют место более сложные бизнес-процессы. Основное отличие адаптируемых систем от коробочных решений связано с их построением – «коробка» имеет определенный функционал и не подразумевает добавления никаких дополнительных функций. Адаптируемые системы построены на базе центрального модуля, позволяющего автоматизировать основные складские процессы. При необходимости к такой системе можно добавить дополнительные модули, которые способны обеспечить автоматизацию уже более специализированных процессов конкретного склада, а также выстроить свою систему правил, позволяющую описать новые технологические процессы.
Что касается систем управления, создающихся под заказ, то главная их задача заключается в том, чтобы максимально учесть все особенности складских бизнес-процессов конкретной компании со сложным строением логистической цепочки. В основе подобных систем управления лежит программная платформа, которая дает возможность для внесения значительных изменений и донастроек. Основная проблема заказной системы заключается в трудностях, связанных с дальнейшим сопровождением и масштабированием. Если система сильно кастомизирована, то поддерживать ее будет довольно сложно даже для производителя, а возможности масштабирования, несмотря на то, что такой «костюм» шьется по индивидуальным меркам, могут быть сильно ограничены именно самим подходом, который применялся при реализации функционала.
Как подготовить предприятие к внедрению
Как правило, процесс автоматизации склада начинается с формирования проектной команды. Оптимально, если она со стороны заказчика включает в себя руководителя проекта (согласование финансовых, юридических и прочих вопросов общеорганизационного характера), представителя отдела информационных технологий (вопросы интеграции, IT-инфраструктуры), бизнес-аналитика (сопоставление бизнес-процессов), директора по логистике (определение необходимых требований к масштабируемости на основании стратегии развития компании), начальника склада (распределение ролей, формирование групп обучения, согласование графика обучения, ответственность за подготовку склада к внедрению WMS) и координатора проектной группы (любой специалист, отвечающий за консолидацию данных и взаимодействие с руководителем проектной группы подрядчика).
Аналогичная проектная группа формируется и со стороны подрядчика. Обычно в нее входит руководитель проекта, администратор проекта, технолог/ бизнес-аналитик, системный аналитик и консультант (консультанты). Основная задача такой команды – обеспечить необходимую подготовку к внедрению системы управления складом и приложить все усилия для прохождения указанных в плане-графике проекта этапов без опозданий. От того, насколько организована будет эта команда, зависит как качество, так и оперативность принятия решений в ходе реализации всего проекта.
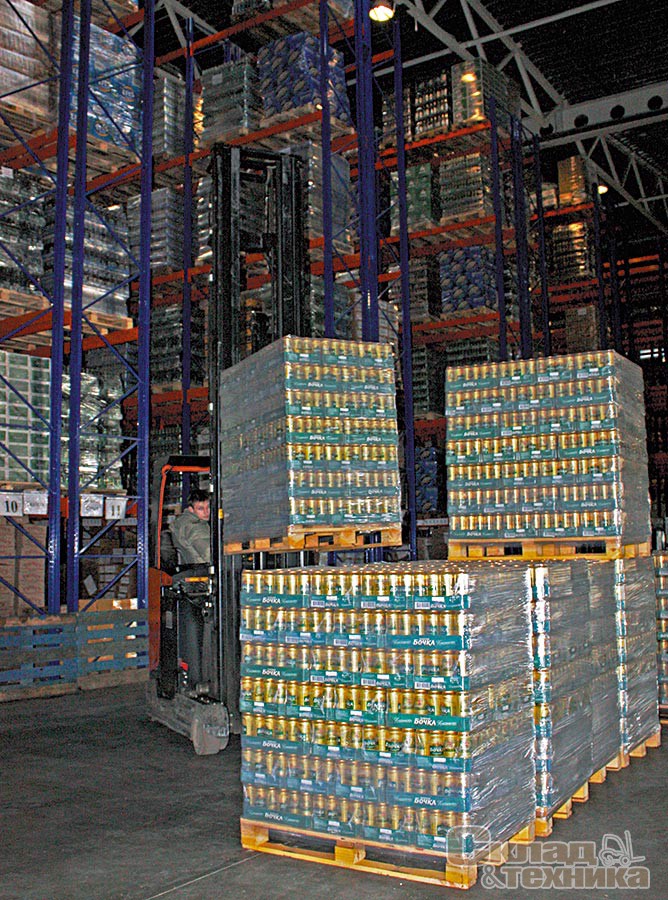
После того, как сформированы проектные группы, определен регламент взаимодействия по различным вопросам, начинается процесс разработки технического задания (ТЗ). Базой для ТЗ является технология работы складского комплекса, и если заказчик WMS ее не имеет, то придется либо разрабатывать ее самостоятельно, либо заказывать. Надо учитывать, что разработка технологии – процесс довольно длительный, а если он еще и накладывается на размытую стратегию развития компании, то рискует стать бесконечным. На этапе утверждения ТЗ необходимо детально проработать процесс интеграции WMS и внутренних корпоративных информационных систем (КИС) заказчика. Конечно, будущему пользователю изначально трудно представить себе весь спектр возможных вопросов, которые необходимо обсудить с внедренцем, но при тщательной проработке ТЗ «белых пятен» в нем оставаться не должно. Вопросы технологии, технической реализации и сроков должны быть прозрачны для каждой стороны.
Далее начинается один из самых сложных этапов проекта – подготовка склада к внедрению и прохождение первичного этапа освоения WMS. Сюда входит целый ряд мероприятий: от обучения персонала и его организационной подготовки, выработки схемы мотивации до планирования инвентаризации, если речь идет о работающем складе. Упустив из виду даже одно из таких мероприятий, можно получить серьезные проблемы с качеством проекта, поскольку сотрудники склада не смогут работать с тем, чего они не понимают и чему они не доверяют. Прорабатывать вопрос доверия людей к некой «системе» необходимо с самого начала. Часто проблемы возникают на уровне начальника склада и старших смены, которые тревожатся, смогут ли они сохранить свои места и уровень своей значимости, и потому стараются все возникающие ошибки перекладывать на систему управления, руководствуясь простым аргументом, что проверить это вряд ли возможно. В определенные моменты такой подход может сформировать полноценный базис для саботирования проекта, что не такая уж редкость даже в современных условиях.
Также необходимо отметить, что одним из критериев успешного проекта является выбор оптимального времени для запуска. Не имеет смысла запускать проект в сезон пиковых нагрузок на склад в надежде на то, что WMS «все вытащит». Именно в этот период может возникнуть необходимость произвести некоторые корректировки в настройках, и не стоит забывать об определенном времени, которое требуется персоналу для адаптации к новой технологии работы. Сопровождение опытной эксплуатации командой подрядчика – необходимость, от которой не стоит отказываться, даже если оно увеличивает стоимость внедрения. Решая вопрос сопровождения, особое внимание надо обратить на режим работы склада, так как круглосуточное сопровождение будет стоить намного дороже, чем только дневное. Практикуемый некоторыми заказчиками подход «на месте договоримся» может вылиться в отсутствие необходимого ресурса (круглосуточная работа подразумевает три смены сотрудников), поэтому такие вопросы лучше решать заранее.
Где бы ни использовались системы контроля исполнения, их доля неуклонно растет. Логично, что работа сотрудников под управлением системы значительно снижает риски, связанные с неисполнением предусмотренных по технологии работ, а средства автоматической идентификации позволяют подключить современную технику даже к распознаванию пришедших на склад грузов. Именно поэтому спрос на WMS и логистический консалтинг в этом году значительно выше, чем в прошлом, а в скором будущем сложно будет себе представить предприятие, склад которого не оснащен системой управления. Чтобы выдержать современный ритм и успешно работать как на российском, так и на зарубежных рынках, компаниям необходимо оптимизировать свой бизнес, используя и внедряя инновационные технологии. Только следуя современным тенденциям его ведения, отечественные предприятия смогут быть конкурентоспособными.