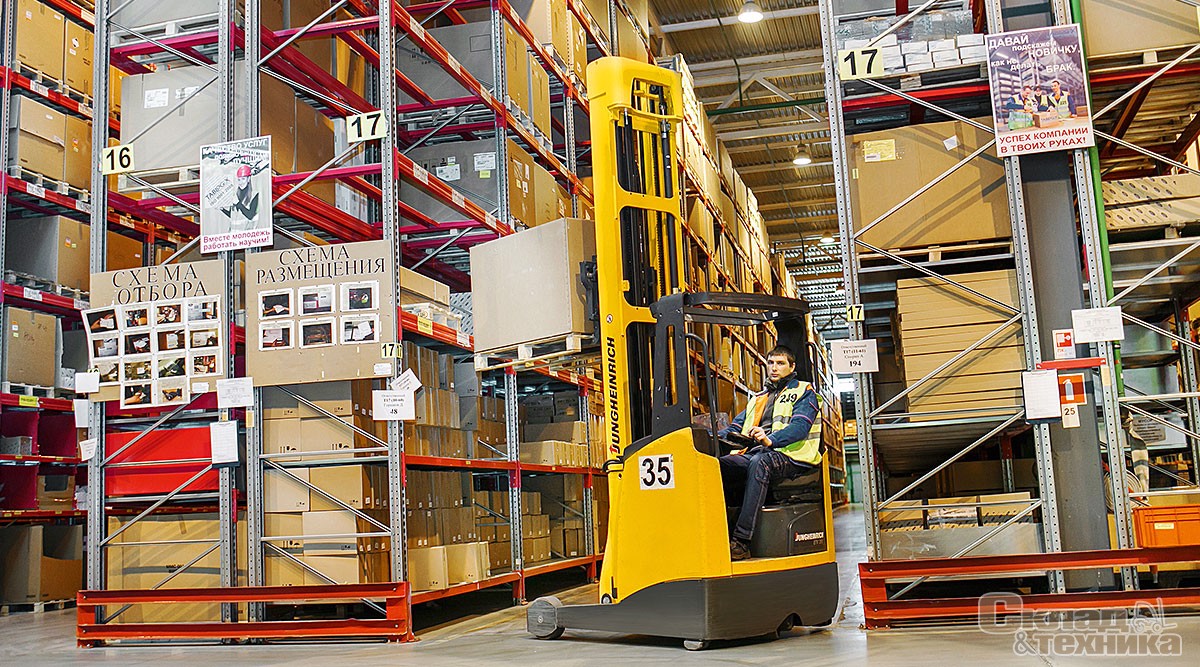
Борьба с «человеческим фактором» на складе
Ошибки персонала всегда имеют критическое значение для склада. За ними следует недовольство конечных получателей и рекламации. Причина большинства ошибок: «человеческий фактор», оптимизация процессов под исполнителя самим исполнителем, что приводит к нарушению рабочей инструкции и технологии. Ошибки на складе также могут быть вызваны низким уровнем автоматизации.
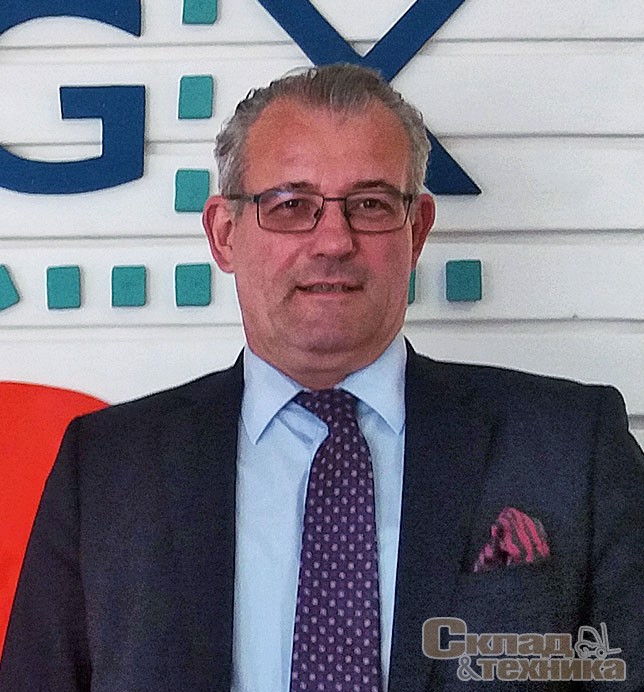
Чем робот-кладовщик отличается от человека? Он не умеет откликаться на среду. Например, если товар на склад поступает в беспорядке, то робот, который обучен выполнять определенные действия, не сможет визуально идентифицировать товар. У человека, наоборот, высокий уровень абстрактного мышления. Зачастую, чтобы распознать такой товар в складском хозяйстве, работник задействует все органы чувств. Стоимость складских роботов превышает стоимость ручного труда. Они могут безошибочно выполнять однотипные действия, если четко выстроены все операции.
В любом бизнесе есть процессы, без автоматизации которых и при использовании только ручного труда невозможно избежать ошибок.
С целью снижения количества ошибок на складе используются терминалы сбора данных. Для их эффективной работы требуется высокая культура производства – подготовленный персонал, выверенные рабочие процессы и планировка склада. Каждый ресурс на складе (техника, стеллажи, упаковка, продукция, персонал) должны иметь обозначения, которые распознает компьютер. Стратегию работы склада (приемка, размещение, отгрузка и др.) автоматически строит система управления складом (WMS). Если ресурсы не оцифрованы и производственные процессы не налажены, терминал сбора данных бесполезен. Другими словами, беспорядок нельзя автоматизировать.
К ошибкам в управлении ведет нарушение международного стандарта менеджмента качества.
Задача менеджера – организовать процесс. В правильно организованной системе управления результат работы на 80% зависит от руководителя и на 20% – от исполнителя. На одного руководителя должно приходиться до семи подчиненных. Идеально, если их количество не превышает пяти.
Нарушение стандарта менеджмента 9001:2015 приводит к грубым ошибкам. Первая типичная ошибка – вместо фактов при принятии решений полагаться на чьи-либо мнения, вторая – пытаться исправить ситуацию, не проанализировав ее причины. И наконец, третья: поручить работу сотрудникам, которые не обладают нужной квалификацией (навыки, подготовка, опыт).

Менее серьезные ошибки менеджер допускает, когда нарушает порядок принятия решения, который насчитывает не менее 20 шагов, начиная с прогноза ситуации и заканчивая уточнениями и поправками своих решений. Типичный пример такой ошибки: менеджер поставил задачу и не убедился, что исполнитель четко понял ее, не обеспечил необходимые ресурсы или не проверил исполнение. Если с двух-трех попыток менеджер не достигает результата, то у него низкая результативность.
Менеджер работает в условиях неопределенности и ограниченных ресурсов, поэтому вероятность ошибки есть всегда. Как было сказано выше, чтобы минимизировать ошибки, рекомендуется придерживаться международного стандарта менеджмента качества 9001:2015. Менеджер также должен оценивать собственную результативность. Она складывается из того, сколько он давал указаний и как часто возвращался к этому вопросу, насколько точно его понимают подчиненные.
Нехватка ресурсов – одна из причин ошибок.
На этот счет есть две теории. Международный стандарт 9001:2015 говорит, что сначала нужно достичь результата, а потом экономить ресурсы. Теория повышения эффективности с самого начала учит экономить ресурсы. И те, кто ей полностью следует, рискуют потерять результативность.
Мы боремся с ошибками путем непрерывного улучшения всех процессов.
В Tablogix мы используем план действий (action timing plan), листы непрерывных улучшений, отрабатываем предложения сотрудников, проводим кружки качества, применяем инструменты lean-менеджмента, используем метод анализа Парето. Развитие этих инструментов входит в круг ответственности Tablogix Center of Excellence (Центр передового опыта), который объединяет сотрудников отделов: управления качеством, проектов, складской аналитики, автоматизированных систем управления. Расскажем подробнее о перечисленных инструментах.
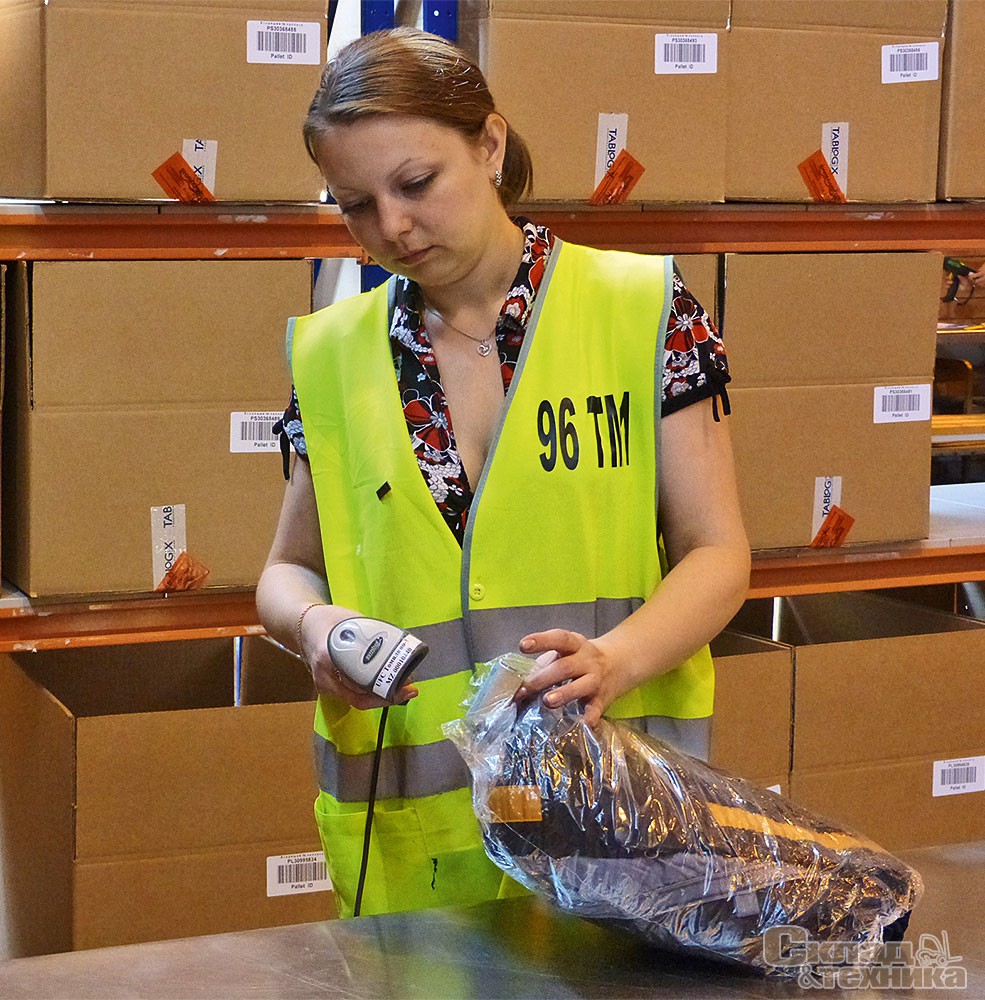
GEMBA (Zero Tolerance Depot Walk). Этот подход мы позаимствовали у японцев. Он учит для понимания ситуации прийти на «гемба» – место выполнения процесса, и на основе фактов, полученных на месте, принять решение. Руководитель должен знать, где в компании создается добавленная стоимость. Как правило, это производственный участок, а в нашем случае – склад. Именно здесь необходимо следить за точностью и ходом работы. Допустим, мы замечаем беспорядок в определенной зоне, который приведет к снижению производительности труда во время комплектации заказа. Для выявления «узких» мест используется Zero Tolerance – фиксация всех малейших замечаний. Менеджер делает фотографии там, где работники допускают ошибки. Затем согласовывает мероприятия по улучшению и отслеживает исправление ситуации к определенной дате. Для устранения замечаний используется система 5S – метод организации рабочего пространства.
Метод организации рабочего пространства 5S – инструмент бережливого производства (Lean Management). Это создание оптимальных условий для выполнения операций, поддержания порядка, чистоты с целью экономии времени и энергии за пять шагов:
- сортировка, удаление ненужного;
- самоорганизация, определение для каждой вещи своего места;
- соблюдение чистоты, систематическая уборка;
- стандартизация процесса;
- совершенствование порядка и дисциплины.
План действий (Action and Timing Plan). Этот инструмент контроля содержит сводный план действий с последовательными шагами и ответственными с имеющимися у них ресурсами. План действий включает достаточно деталей для достижения цели. Применение этого инструмента требует организационных усилий от руководителя. Если менеджер не готов сам четко работать, он не добьется этого от рабочих.
![[b]Action Timing Plan[/b]](/article/24452-borba-s-chelovecheskim-faktorom-na-sklade/Images/07.jpg)
Предложения по улучшениям (Employee Improvement Suggestions). Сотрудник представляет предложение в структурированной форме: предпосылки, предложение, шаги, предполагаемая экономия. В случае достижения цели (запланированной экономии) он получает бонусную выплату.
Лист непрерывных улучшений (Continuous Improvement Worksheet). Это упрощенная версия инструмента Employee Improvement Suggestions (Предложения по улучшениям). Лист непрерывных улучшений прикрепляется на стенд. Сотрудники указывают в соответствующих полях, как выполнить рабочий процесс наилучшим образом и снизить риск ошибки. Менеджер оставляет замечания по каждому из предложений. Если они получают положительную оценку, менеджер записывает свои комментарии об исполнении. Если отрицательная, то финальное решение выносит руководитель следующего уровня.
![[b]Continuous Improvement Worksheet[/b]](/article/24452-borba-s-chelovecheskim-faktorom-na-sklade/Images/06.jpg)
Кружок качества (Quality Team Circles). Кружки качества появились в Японии. Они призваны установить доверие и взаимопонимание между менеджерами и линейными сотрудниками и подпитывать интерес к работе. В кружках качества участвуют сотрудники всех уровней. Еженедельно в пятницу, ближе к концу рабочего дня, рабочая группа собирается в комнате размышлений (think room) на 30 минут и обсуждает прошедшую неделю на предмет того, что можно было бы улучшить. Супервизор выслушивает всех и делает заметки. На следующей встрече группа вырабатывает план действий.
Шесть сигм (Six Sigma). Концепция была разработана сотрудником компании Motorola в восьмидесятые годы. Это метод улучшения процессов, в основе которого – статистическая оценка фактов и данных. 6 сигм применяет набор различных инструментов качества, например: статистическое управление процессами на основе контрольных карт, FMEA-анализ, диаграмма Парето, диаграмма Исикавы и др.
![[b]Метод четырех диаграммp[/b]](/article/24452-borba-s-chelovecheskim-faktorom-na-sklade/Images/05f.jpg)
Метод четырех диаграмм (QOS Methodology).
• Установите цель и следите за трендом.
Запустите соответствующую диаграмму и ежемесячно сверяйте показатель с ключевыми показателями эффективности.
• Сделайте анализ проблем по Парето.
Диаграмма Парето распределяет усилия для решения проблем и выявляет основные причины просчетов, с которых нужно начинать их исправление. Диаграмма показывает, какие ошибки вносят наибольший вклад в неблагоприятную тенденцию.
• Создайте план корректирующих действий.
Точно определите корректирующие действия для каждой ошибки.
• Контролируйте выполненные действия.
Определите, соответствуют ли достигнутые улучшения вашим ожиданиями, в противном случае вернитесь к началу.
Анализ видов и последствий отказов (Failure Mode and Effects Analysis, FMEA). Метод анализа и выявления самых критических шагов в процессах с целью управления качеством.
Метод решения проблем 8D (Eight Disciplines of Problem Solving (8D). 8D предназначен для поиска первопричины ошибки, разработки краткосрочного и долгосрочного решения, чтобы не допустить ее повторения. Когда услуга или продукт не удовлетворяет ваших клиентов, 8D является первым шагом к повышению их качества и надежности.
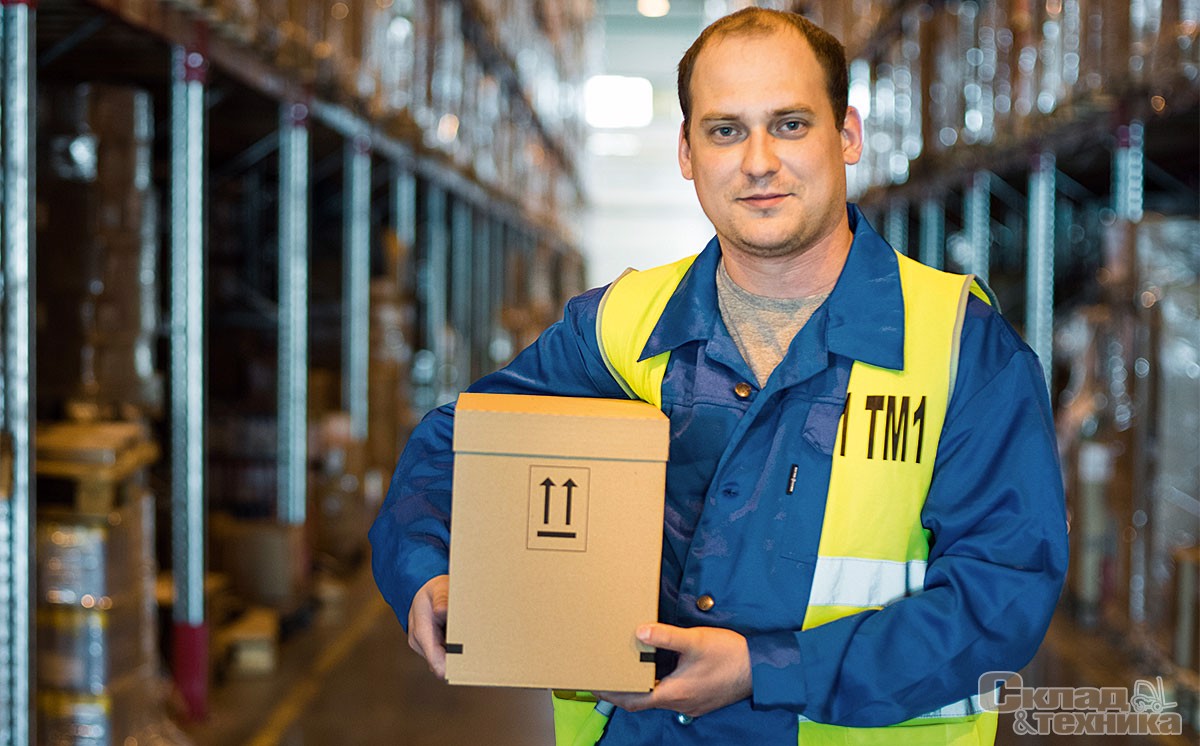
Отчет о корректирующих действиях (Corrective complain action report). Основная цель отчета – исследовать проблему, выполнив анализ первопричин и найдя решение для предотвращения повторения. Он используется как ответ на проблему. Исправление относится к сдерживанию, а корректирующее действие – к основной причине.
Бенчмаркинг (Best Practice Replication). Бенчмаркинг необходим, чтобы избежать многих ошибок, которые кто-то уже допустил до вас. Посещайте производства других организаций, фиксируйте интересные идеи, которые вы обнаружили. Планируйте их реализацию в вашей компании.
Особенности коммуникации для предотвращения ошибок. Установите информационные стенды с наглядными рабочими инструкциями. На стенде ежедневно размещайте ключевые показатели эффективности и достигнутые результаты. Простые индикаторы показывают уровень производительности и качества: большой палец вверх или вниз, веселый или грустный смайл, красная или зеленая карточка и др. Отображение актуального статуса мотивирует персонал сконцентрироваться на работе без ошибок и не подводить весь участок склада.