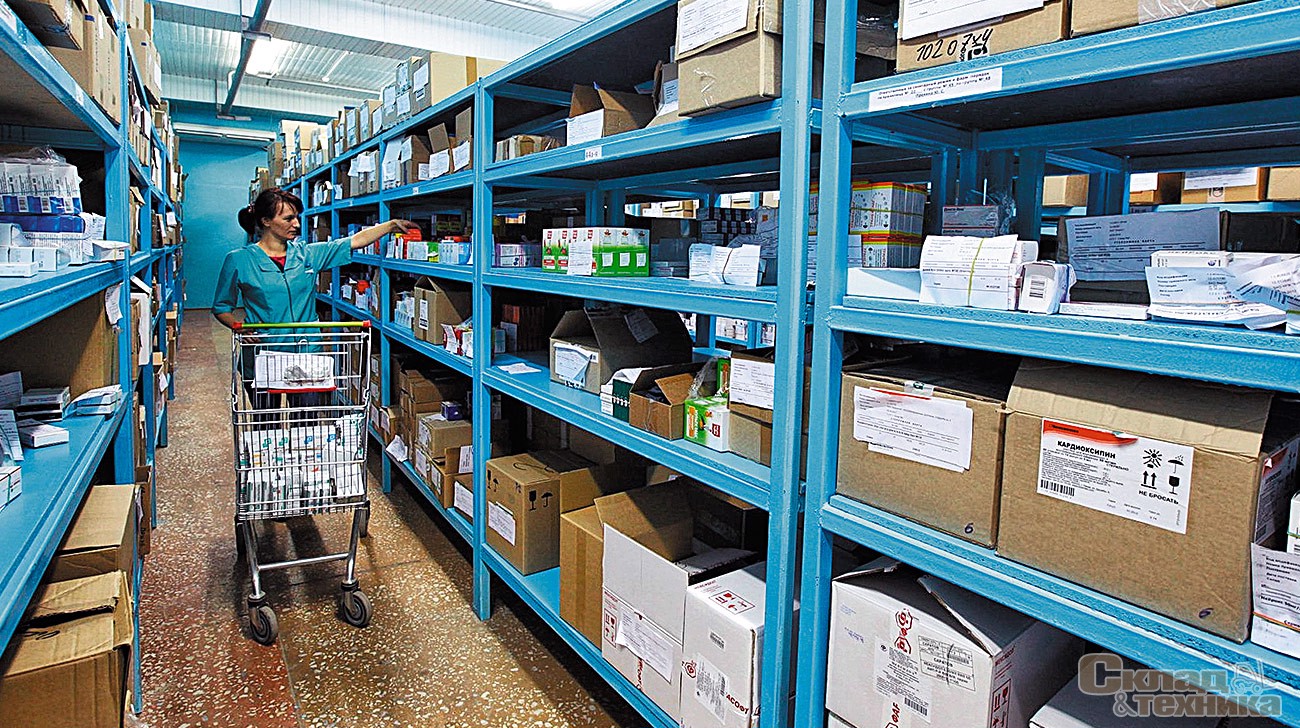
Особенности технологических решений для современных фармацевтических складов
Склад фармацевтической продукции, без сомнения, является одним из наиболее интересных решений для хранения продукции с точки зрения возможностей эффективной автоматизации внутренней логистики путем последовательного усложнения используемых систем хранения и комплектации, повышения технологического уровня обработки на фоне многообразия внутрискладского перемещения товаров.
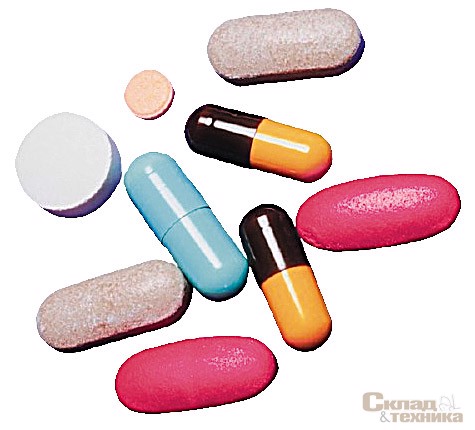
В последнее десятилетие российский фармацевтический рынок продемонстрировал фантастические темпы роста, в значительной степени превосходящие аналогичные показатели развитых рынков. Это потребовало соответствующего расширения его логистической составляющей, в том числе создания системы современных фармацевтических складов. При этом функционирование такого склада относится к видам фармацевтической деятельности и подлежит обязательному лицензированию в соответствии с постановлением Правительства РФ от 22 декабря 2011 г. № 1081 «О лицензировании фармацевтической деятельности», что вносит некоторые дополнительные организационные сложности в процесс его создания и запуска.
Характер продукции, которой оперирует фармацевтический склад, определяет целый ряд естественных требований к организации хранения, к которым относятся изолированность складского помещения, территориальное разделение зон приема, хранения и комплектации заказов. Отдельными документами регламентируются температурные режимы хранения, вентиляция и освещение, устройство полов и многое другое. Для обеспечения надлежащих условий хранения складские помещения необходимо оснащать термометрами, гигрометрами, системой приточно-вытяжной вентиляции, системами пожарообнаружения и пожаротушения. Полы аптекарских и фармацевтических складов должны иметь ровную гладкую бесшовную поверхность высокой прочности и износостойкости, легкую в уборке и химически устойчивую. Для хранения определенных видов фармацевтической продукции внутри склада могут размещаться холодильные камеры, обеспечивающие необходимый температурный режим хранения.
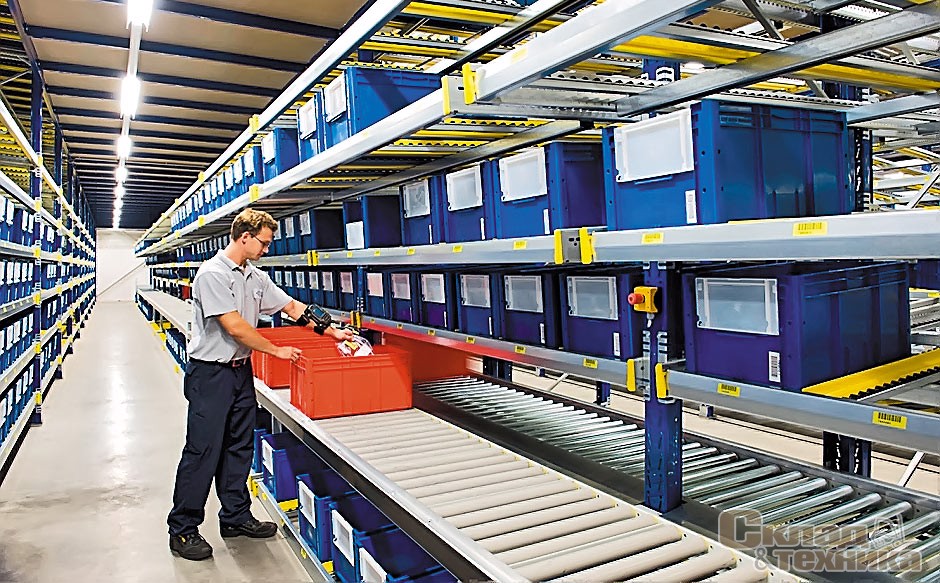
Но наибольший интерес представляют именно современные решения в сфере складской логистики, обусловленные самой природой фармацевтического склада, которые лучше всего рассматривать применительно к существующим и создающимся крупным складским комплексам. Как правило, в качестве базы для их размещения используются склады класса А. Первым важным звеном логистической цепочки фармацевтического склада является зона приемки и хранения. С формальной точки зрения автоматизация в ее современном воплощении может начинаться уже с этой позиции. Уровень развития складских систем позволяет построить полностью автоматизированный склад, который может быть оснащен кранами-штабелерами или шаттл-системами для полной автоматизации процесса размещения палетированных грузов и их последующего хранения и выгрузки в зону комплектации. Такие предложения сегодня представляет на рынке целый ряд производителей складского оборудования. Автоматизированный склад работает по принципу «goods-to-man», что можно перевести как «движение товара к человеку». Все перемещения грузов осуществляются при помощи автоматики, управление которой согласовано с WMS-системой склада, что позволяет избежать ошибок складского учета, связанных с человеческим фактором.
Основным преимуществом автоматизированного склада является максимально эффективное использование имеющихся площадей при помощи высотной системы хранения и минимизации расстояния между стеллажами. Передача значительной части управляющих функций от человека к WMS-системе сокращает время приема и обработки заказа, размещения товара и его подачи в зону комплектации заказов. Это существенно снижает операционные затраты, хотя и сопряжено со значительно бо’льшими капитальными затратами при строительстве склада подобного уровня автоматизации. Однако с учетом того, что на фармацевтических складах лишь в редких случаях применяют палетную отгрузку товаров, а чаще комплектуют заказы, используя в качестве единицы комплектования даже не коробки, а штучные упаковки, столь высокий уровень автоматизации зоны приемки и хранения может оказаться даже избыточным с точки зрения экономической эффективности. В этом случае, ориентируясь на доступную площадь, можно рассматривать в качестве возможного варианта системы хранения наиболее широко распространенные палетные стеллажи, рассчитанные на обычную систему загрузки–выгрузки, либо, в случае ограничения доступных площадей, использовать узкопроходные стеллажи.
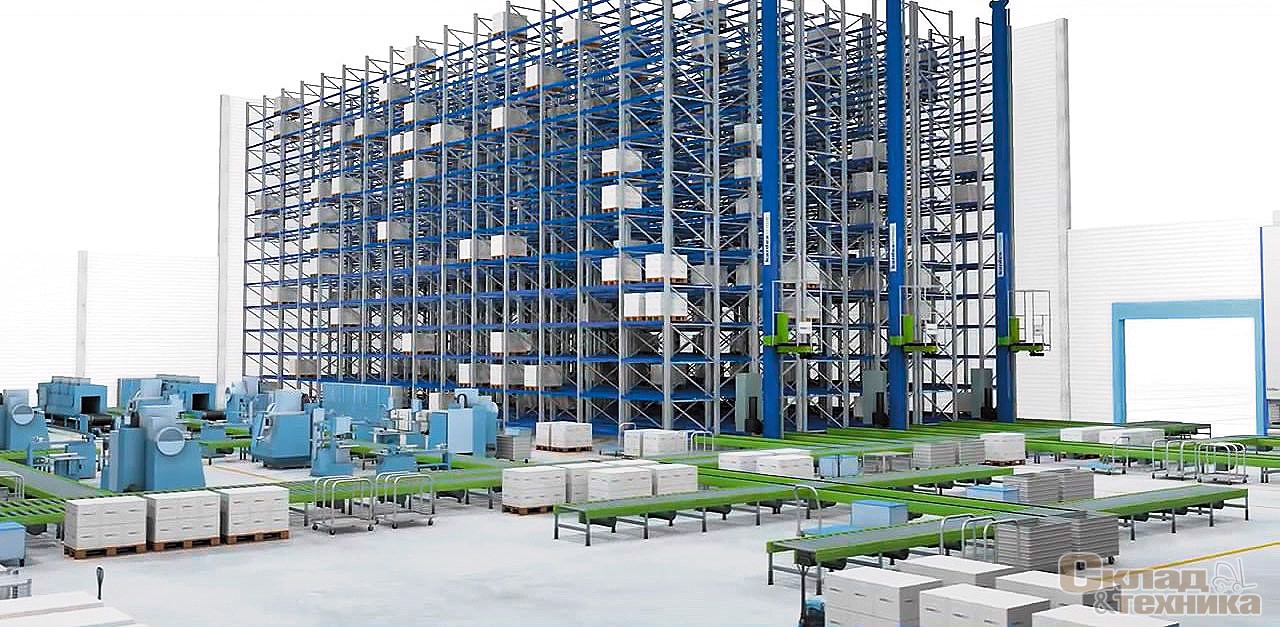
Более широкие возможности для автоматизации имеются на участках комплектации, что связано с необходимостью повышения производительности и точности сборки заказов, состоящих из множества наименований товара. Грамотная организация процесса формирования заказов влияет не только на качество предоставляемых фармацевтическим складом услуг, но и снижает возможные убытки, которые могут возникать в случае ошибок персонала при сборке, уменьшает количество возможных возвратов и рекламаций, улучшает имидж поставщика.
Отбор поштучных заказов – один из главных процессов, который заслуживает пристального внимания, поскольку включает самое большое количество операций, на которые тратится значительное количество ресурсов складского персонала, в отличие от процессов приемки, перемещений, отгрузки. Именно поэтому подготовка заказов является наиболее весомой статьей затрат на складскую обработку. Главная цель, которую преследует автоматизация процессов на этой стадии обработки, – увеличение производительности труда, сокращение времени отборки заказов при увеличении точности отбора. В общем случае попытка добиться большей производительности только за счет организационных или стимулирующих мер может приводить к снижению качества комплектации, соответственно требует дополнительных мер контроля, что усложняет и удорожает процесс. В этом случае на помощь могут приходить современные технологии.
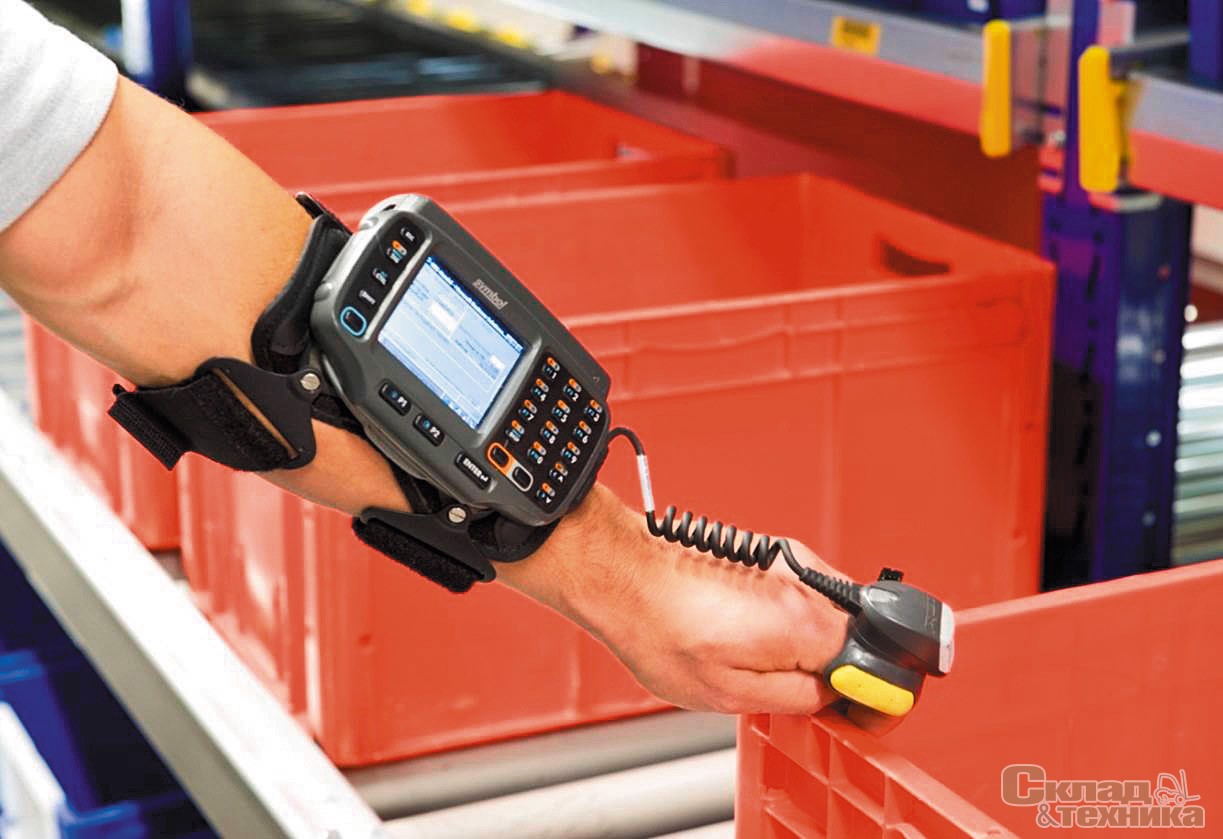
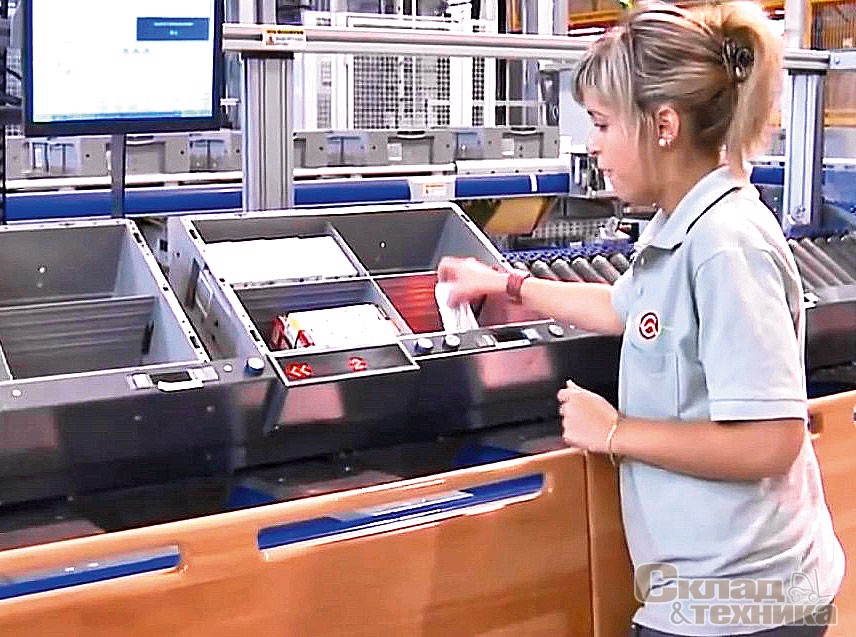
Сегодня на рынке существует целый ряд конструктивных решений автоматизированных линий, бо’льшую часть которых, тем не менее, можно свести в две основные группы – горизонтальные и вертикальные карусельные конструкции или лифтовые системы. Рассмотрим обе эти группы более подробно.
Начнем с вертикальных карусельных шкафов, которые являются одними из самых простых систем для хранения товара и автоматизированной комплектации заказов по системе «goods-to-man». Устройство состоит из лотков с товаром, которые последовательно перемещаются в вертикальной плоскости. Отличительной особенностью конструкций подобного типа является компактность. Лотки могут использоваться как для хранения одного вида товара, так и нескольких наименований. Для их перемещения применяется цепной привод с автоматически регулируемым натяжением цепи, что обеспечивает малые временные затраты на транспортировку требуемой продукции к оператору, плавность движения, надежность и долговечность системы перемещения.
Основная сфера применения вертикальных карусельных систем – помещения, ограниченные по высоте (до 8 м). Представленные сегодня на рынке системы монтируются в течение очень короткого времени, а также при необходимости перепланировки могут без демонтажа перемещаться по территории склада. Таким образом, основными преимуществами вертикальных карусельных систем являются: высокая эффективность использования складских площадей при наличии ограничений по высоте, высокая плотность хранения товаров, малое время поиска и транспортировки товара к оператору, высокая скорость комплектации заказов, незначительное количество ошибок в процессе комплектации, простота и надежность конструкции.
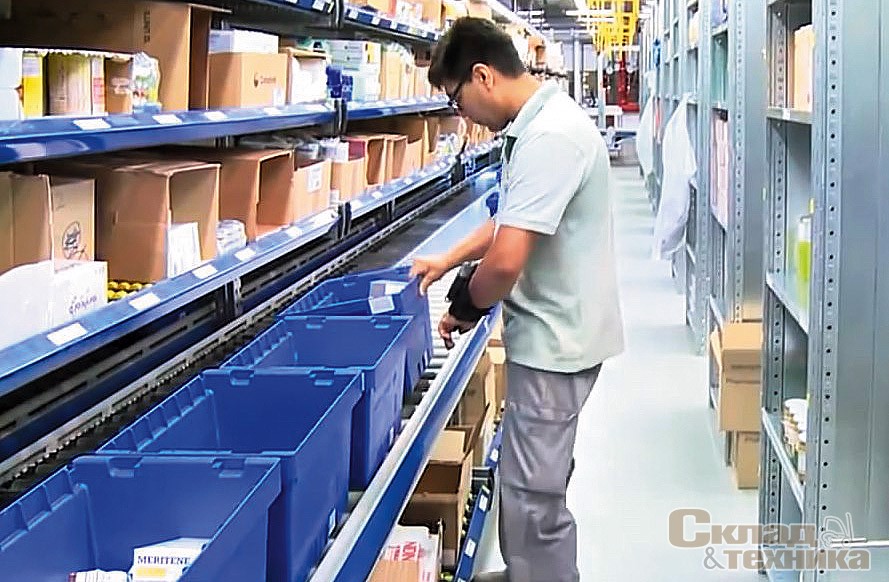
А что делать, если высота имеющегося помещения намного меньше, чем 8 м? В этом случае специалисты по автоматизации рекомендуют горизонтальную карусельную систему, которая может успешно применяться в помещениях высотой всего до 4 м, также обеспечивая при этом высокий уровень автоматизации подбора. В устройствах контейнеры с товаром движутся по кругу в горизонтальной плоскости. Если высота помещения позволяет, можно использовать более сложную конструкцию, которая позволяет эффективно осуществлять подбор на двух (а иногда, если позволяет высота помещения, – и на трех) уровнях помещения склада. Практика использования горизонтальных карусельных систем показывает, что при максимальной загрузке один оператор за смену может обеспечить комплектацию более 3 тыс. заказов. Использование съемных контейнеров облегчает доукомплектование системы. Размер рабочей станции может достигать 50 м в длину и 10 м в ширину.
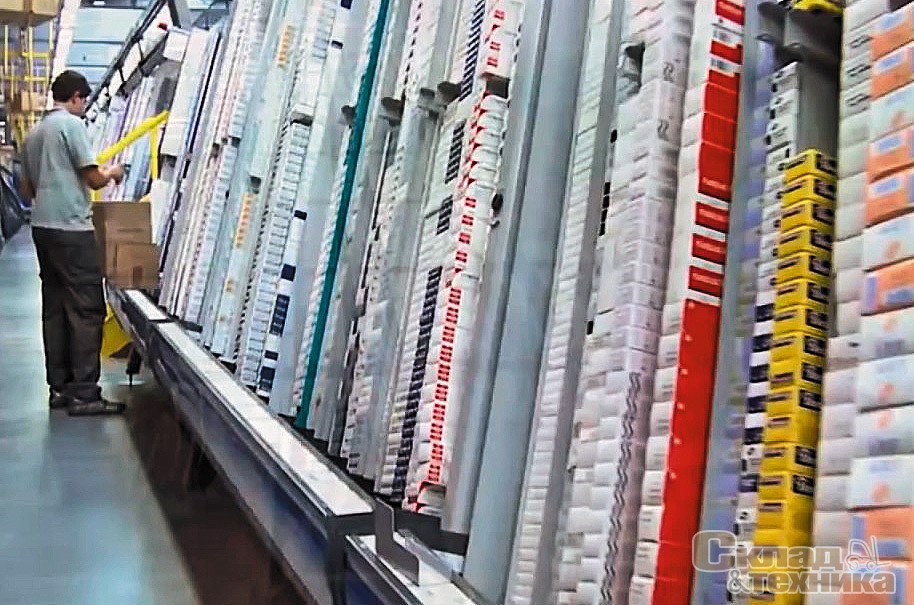
Горизонтальные карусельные системы имеют практически тот же набор основных преимуществ, что и вертикальные. Кроме того, они являются наиболее эффективным (или единственным действительно эффективным) решением для низких складских помещений.
Наибольший интерес при создании новых фармацевтических складов, начиная с этапа строительства либо при размещении их на территории современных складских комплексов класса А и А+, где высота помещений составляет не менее 11 м, вызывают вертикальные лифтовые системы. Это вертикальные конструкции, их высота иногда достигает 30 м. Товары размещаются на полках, высота которых может регулироваться с достаточно малым шагом, что обеспечивает высокую плотность загрузки. Каждый модуль автоматизированной лифтовой системы хранения может иметь несколько окон выдачи товара, они также являются рабочим местом оператора. Вертикальные лифтовые системы применяются для очень широкого спектра товаров, включая как мелкие расфасованные товары (основной вид фармацевтической продукции), так и крупногабаритную продукцию, масса которой, бывает, достигает 1 т.
Перемещение полок с размещенными на них товарами от места хранения к окнам выдачи осуществляется с помощью специальной платформы, движущейся по вертикальным направляющим и оснащенной специальными экстракторами. С их помощью полки с размещенным на них товаром движутся из отсека хранения на платформу, а затем по лифтовым направляющим к окну выдачи. Высокая производительность подбора достигается при одновременной работе нескольких окон выдачи (нескольких операторов), а также за счет того, что в каждое окно выдачи может одновременно доставляться несколько полок с товаром, размещенных на разных уровнях.
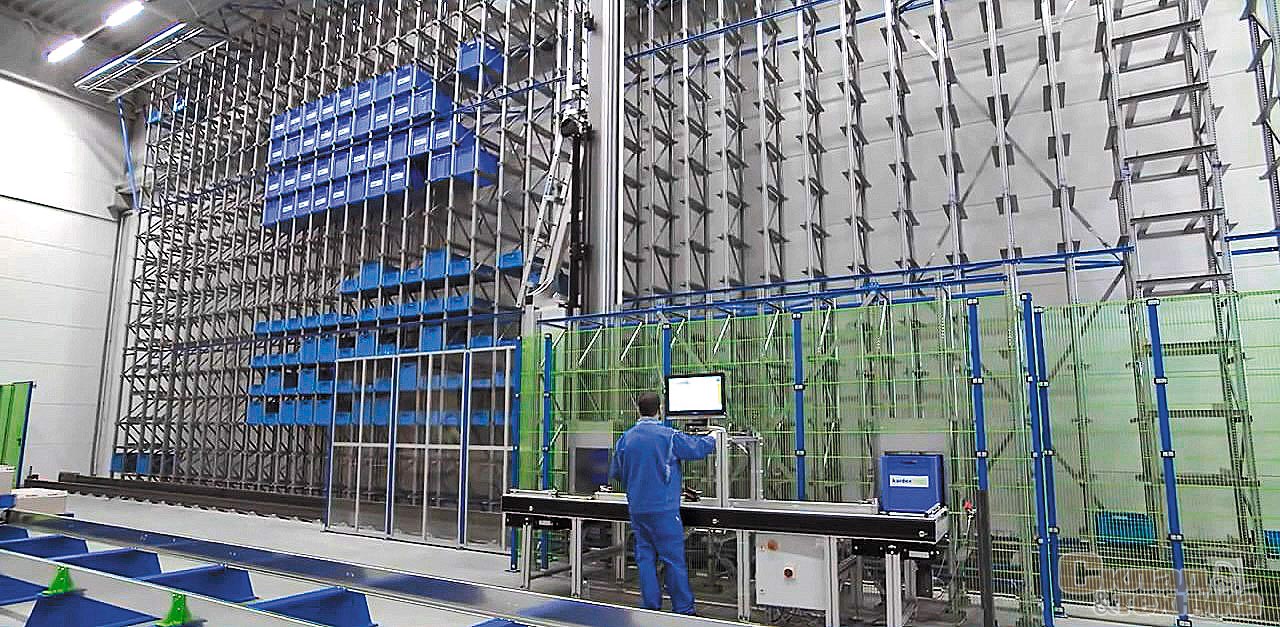
Еще одним из важнейших элементов повышения эффективности работы современного фармацевтического склада является организация процесса эффективного пополнения товарного запаса, размещенного непосредственно на участке комплектации в автоматизированных системах карусельного или лифтового типа. Ускорить процесс комплектования можно за счет организации промежуточной зоны, в которую будут подаваться на разукомплектование (подпитку) палеты с товаром, имеющим наиболее высокую скорость оборота. Для таких промежуточных зон целесообразно использовать палетные гравитационные стеллажи, работающие по системе FIFO (First-In First-Out, то есть первый загруженный поддон будет первым доступен со стороны выгрузки). Гравитационные стеллажи представляют собой блочно-рамные конструкции с наклонными неприводными гравитационными роликовыми конвейерами, установленными под определенным углом к горизонту, чтобы обеспечить движение поддона под действием собственного веса к зоне выгрузки.
И наконец, «вершиной» автоматизации современного фармацевтического склада можно считать полностью автоматизированную конвейерную систему комплектования заказов, которая эффективно применяется в случае больших объемов отбора аналогичных товаров, имеющих относительно небольшие размеры. Автоматические системы подготовки заказов в большинстве случаев применяются именно на фармацевтических распределительных центрах, где требуется комплектация большого количества заказов с аналогичными наименованиями товаров.
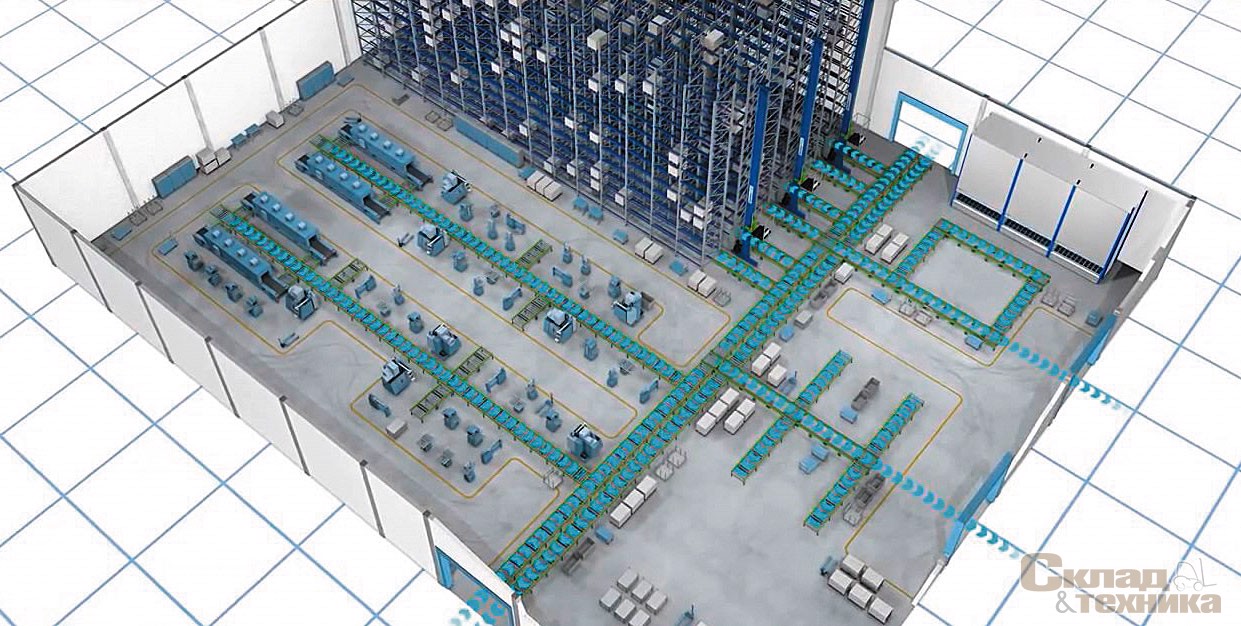
Подведем некоторые итоги. Конечно, рассматриваемые в этой статье виды автоматизации фармацевтических складов применимы не во всех случаях. Важное значение имеет фактор масштаба, поскольку автоматизация не цель, а средство повышения эффективности, в том числе финансовой отдачи на сделанные инвестиции. Тем не менее все большее значение в последние годы приобретает стратегия увеличения масштабов бизнеса, расширения клиентской базы как основной путь повышения устойчивости.
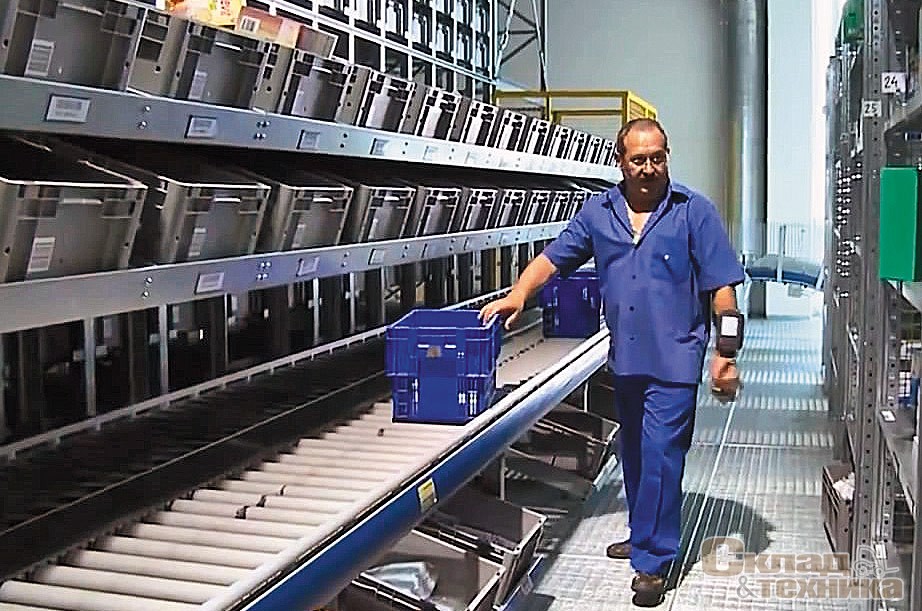
Растущие компании неизбежно сталкиваются с проблемой масштабирования бизнеса, когда попытка «арифметического» умножения существующих бизнес-процессов – увеличение количества операторов подбора и иного складского персонала, парка складской техники, складских площадей – становится главным ограничением потенциального роста, поскольку повышает вероятность ошибок, затрудняет управление. Именно в этот момент компания должна сделать правильный выбор, определив именно то решение по автоматизации бизнес-процессов, которое, с одной стороны, позволит в достаточной степени нарастить объемы бизнеса, а с другой стороны, потребует оптимальных финансовых затрат.
Как показывает практика работы лидеров складского фармацевтического бизнеса, выбирающих путь автоматизации процессов, современный фармацевтический склад, со всеми организационными сложностями, с наличием специфических требований к организации хранения такой продукции, с необходимостью комплектации огромного количества заказов с высоким уровнем детализации (с очень большим количеством уникальных наименований товаров – SKU), и в то же время соответствующий вызовам сегодняшнего рынка, является результатом решения целого комплекса задач в сфере складской логистики. Задач, с одной стороны, несомненно, сложных, но с другой – очень интересных и требующих высокопрофессионального подхода.
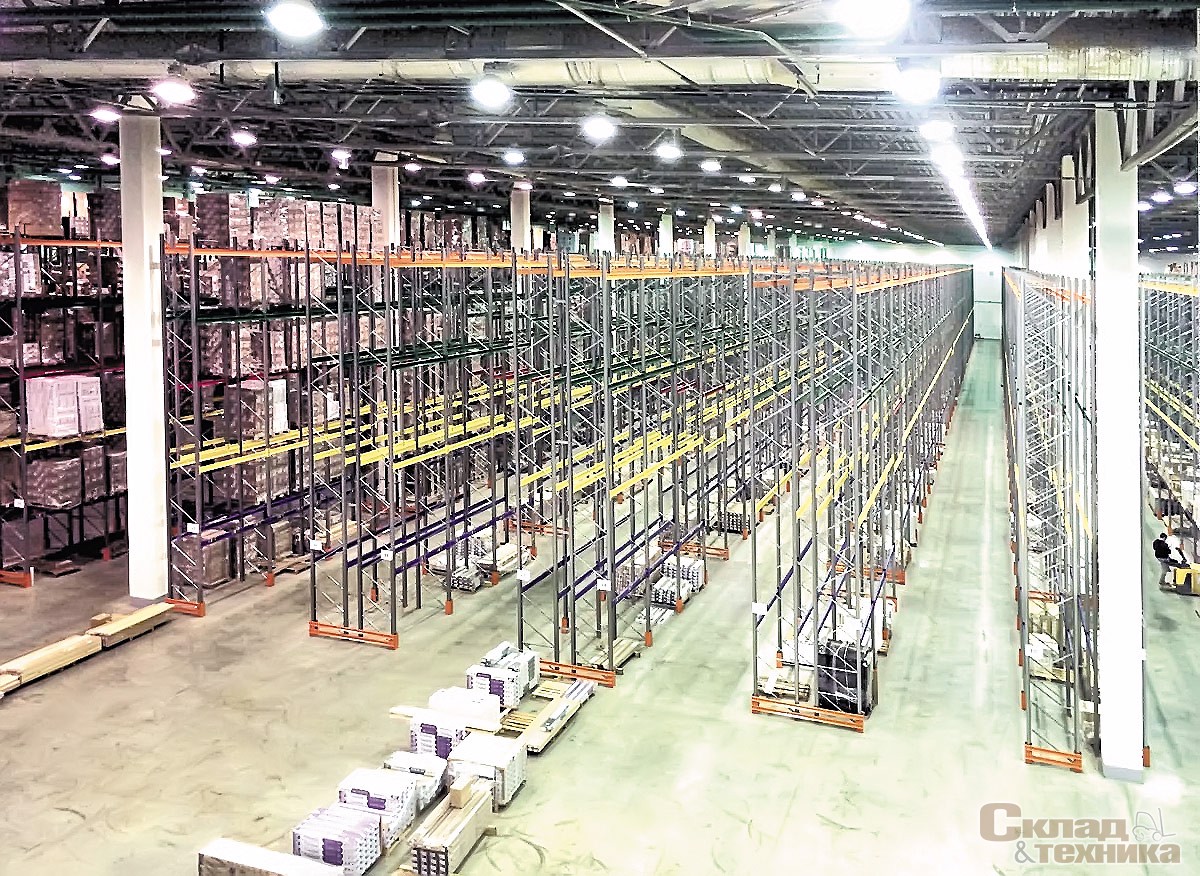