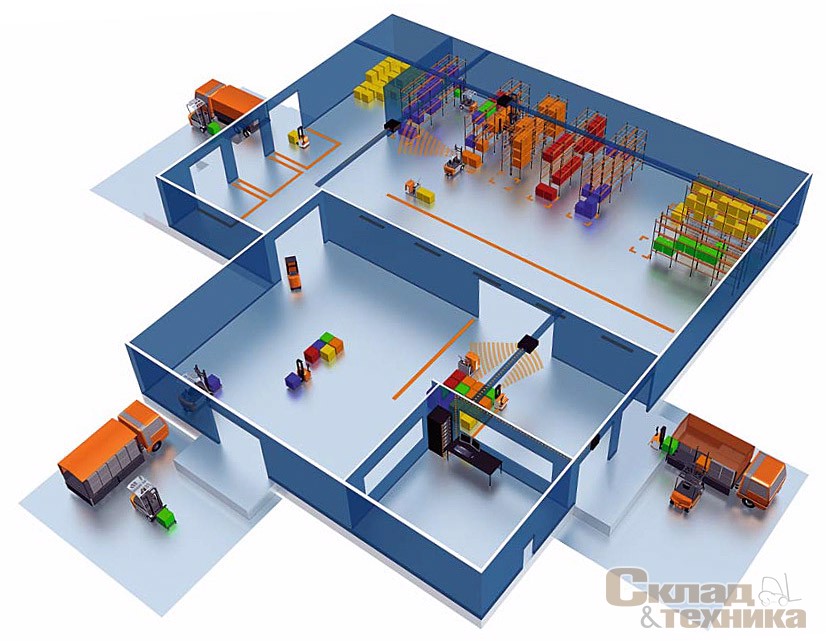
Оптимизация технологического процесса на складе (Часть 1)
Основу внутрискладской логистики составляет технологический процесс, т. е. система операций по подготовке склада к приемке продукции, разгрузке транспортных средств, приемке продукции, размещению ее на хранение, организации хранения, комплектации заказов, подготовке к отпуску и отгрузке со склада. От того, насколько эффективно будут выполнены эти операции, зависит работа других отделов компании, уровень логистического сервиса, предоставляемого клиентам, а следовательно, и уровень конкурентоспособности компании на рынке. В связи с этим перед руководством склада каждого предприятия стоит задача максимально оптимизировать технологический процесс.
В современной практике сформировались типовые принципы и общая логика организации технологического процесса, типовой порядок выполнения операций которого показан на рис. 1.
Правильно организованный складской технологический процесс должен отвечать оптимальным параметрам по скорости выполнения операций, обеспечивать сохранность товаров, экономичность затрат и высокий уровень логистического сервиса. Первичной операцией этого процесса является приемка продукции и связанные с ней операции по подготовке склада к приемке.
![[b]Рис. 1.[/b] Типовой технологический процесс](/article/10169-optimizatsiya-tehnologicheskogo-protsessa-na-sklade/Images/01.jpg)
В 2002/2003 г. специалисты Координационного совета по логистике провели детальный анализ процедуры приемки продукции на складах 23 компаний разных отраслей – оптовая продажа канцелярских товаров, офисной и домашней мебели, производство и продажа сплавов и металлических изделий, парфюмерной продукции и средств бытовой химии, не скоропортящихся продуктов питания и др. В ходе анализа получены следующие результаты: на 60% исследуемых складов допускались ошибки в приемке продукции по количеству (массе), которые приводили к отсутствию более 8% товаров. На 25% складов допускались ошибки, приводившие к 5%-ной недостаче, и на 15% складов были допущены ошибки, приводившие менее чем к 2%-ной недостаче (бo’льшую часть складов составляли терминалы логистических операторов). На 70% складов качество приемки становилось причиной того, что предприятия, сами того не ведая, принимали на хранение и реализацию более 12% товарных позиций, которые не соответствовали товарной номенклатуре, определенной в договоре поставки, а это в дальнейшем, естественно, приводило к пересортице. На большинстве складов (более 60%) осуществлялась приемка бракованной продукции (как с несоответствующими потребительскими свойствами, так и с нарушенной оригинальной упаковкой производителя), составляющая от 3 до 8% общего объема единовременной поставки. В совокупности эти ошибки приводили к серьезным финансовым потерям и ухудшению отношений с клиентами, так как из-за возникающей пересортицы клиентам данных компаний также частично поставлялась продукция, не соответствующая условиям договора.
С целью исключить возможность возникновения подобной ситуации был разработан универсальный алгоритм осуществления процедуры приемки продукции и смежных операций (рис. 2), который позволяет существенно оптимизировать процесс приемки продукции и связанных с ней операций.
![[b]Рис. 2.[/b] Алгоритм проведения приемки продукции и смежных операций](/article/10169-optimizatsiya-tehnologicheskogo-protsessa-na-sklade/Images/02.jpg)
Подготовка склада к приёмке продукции
На большинстве складов какие-либо операции по подготовке к приемке продукции не проводят вообще. Как следствие, поступление партий товара является полной неожиданностью для складского персонала, что в дальнейшем приводит также к негативным последствиям: незапланированный перевод сотрудников с одних операций на другие, например разгрузку транспорта, перемещение товаров и т. п., затоваренность проходов, проездов и др. Чтобы этого избежать, рекомендуется принимать ряд мер:
1. Своевременно получать информацию об ожидаемой поставке товара из отдела снабжения, а именно:
- перечень товарных позиций;
- количество поступающего товара (в том числе по каждой товарной позиции);
- сроки поступления товара;
- наименования поставщика (-ов);
- тип тары (короба, паллеты);
- информацию о дополнительной сопроводительной документации (сертификаты соответствия и т. д.).
Наиболее удобно создать форму документа (карточка сведений поставки), в которую эта информация экспортировалась бы из информационной системы или которую заполняют «вручную», в зависимости от возможностей склада.
2. Определить число служащих (с использованием технологических карт, примерная форма технологической карты приведена на рис. 3), участвующих в разгрузке и приемке продукции; определить состав техники, необходимой для разгрузки транспорта.
3. Определить потенциальные места хранения поступившей продукции.
![[b]Рис. 3.[/b] Примерная форма технологической карты](/article/10169-optimizatsiya-tehnologicheskogo-protsessa-na-sklade/Images/03-1.jpg)
В складской логистике существует философский принцип «всё имеет свое место и на этом месте должно храниться», т. е. предпочтительно, чтобы за каждой товарной группой (товарной позицией) от поставки к поставке была закреплена определенная зона хранения, что позволит в дальнейшем упростить поиск и подбор товара с мест хранения, а также соблюдать принципы товарного соседства. Определить число мест и их конкретное месторасположение можно несколькими способами. Первый – это использование данных информационной системы. В настоящее время практически любая ERP- или WMS-система позволяет достаточно быстро получить данную информацию, однако число складов, которые располагают такими программами, составляет приблизительно от 3 до 5% общего числа складов на территории России.
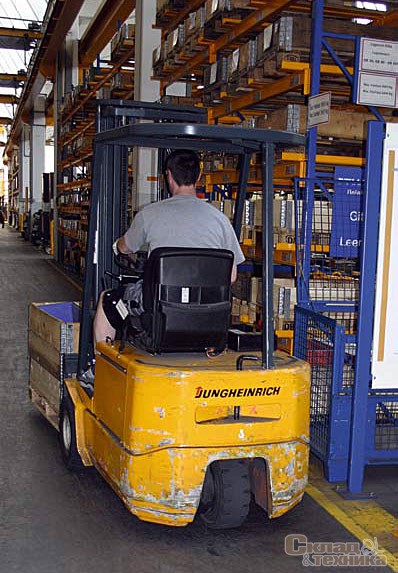
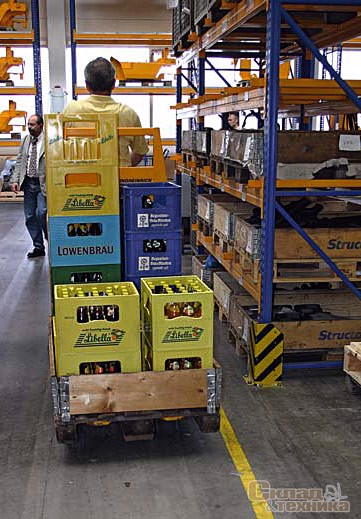
На складах площадью до 1500...2000 м2 число и месторасположение свободных мест на складе обычно определяют исключительно визуально, что занимает значительное количество времени. Кроме того, такая информация быстро теряет актуальность, поскольку за время, которое тратит служащий, производящий осмотр, на перемещение из одной зоны в другую, свободные места уже, как правило, затовариваются. На складах большей площади применение такого метода невозможно в принципе.
Есть еще один способ определения мест хранения – составление карты размещения свободных мест на складе (рис. 4). Этот способ может показаться весьма примитивным, но позволяет существенно оптимизировать процесс поиска свободных мест на складе средней площади – 2000...5000 м2. Сущность метода сводится к тому, что приобретается большая маркерная (пластиковая) доска, на которой несмываемой краской наносят все зоны склада, стеллажи, ячейки с указанием адреса каждого стеллажа и ячейки. Когда производится комплектация заказов, комплектовщик в листе отборки или в другом документе отмечает напротив каждой товарной позиции степень заполненности той ячейки, из которой осуществляется отбор. После комплектации заказа или его части комплектовщик пишет эту же величину маркером на доске (карте) размещения свободных мест на складе. При этом определяется перечень цветов, которыми производят заполнение. Например, красный – полностью заполненная ячейка, синий – ячейка заполнена наполовину, белый/пустой – отсутствие товара в ячейке. Число цветов увеличивать не рекомендуется – это может привести к путанице. В ходе процесса размещения товаров на хранение выполняют аналогичную операцию. Таким образом, получить информацию о наличии и расположении свободных мест на складе возможно при визуальном осмотре такой карты.
![[b]Рис. 4.[/b] Карта размещения свободных мест на складе](/article/10169-optimizatsiya-tehnologicheskogo-protsessa-na-sklade/Images/07f.jpg)
Безусловно, у этого метода есть ряд недостатков и ограничений:
- наличие информации не в режиме online;
- трудовые и временные затраты складских служащих на процедуры отметки в листе комплектации и карте размещения свободных мест хранения;
- риск человеческого фактора при заполнении карты (особенно на начальном этапе внедрения метода);
- практическая невозможность создать карту при глубинном хранении (технически «прорисовать» данную карту практически не представляется возможным);
- отсутствие возможности автоматической распечатки данных карты и передачи их непосредственным исполнителям (возможен только визуальный осмотр и фиксация «вручную» в ином документе).
Несмотря на эти недостатки, данный метод успешно реализован на складах ряда компаний. С течением времени число ошибок при заполнении карты существенно сокращалось, а экономическая привлекательность данного метода вполне удовлетворила руководство складов, не имеющих должного финансового обеспечения.
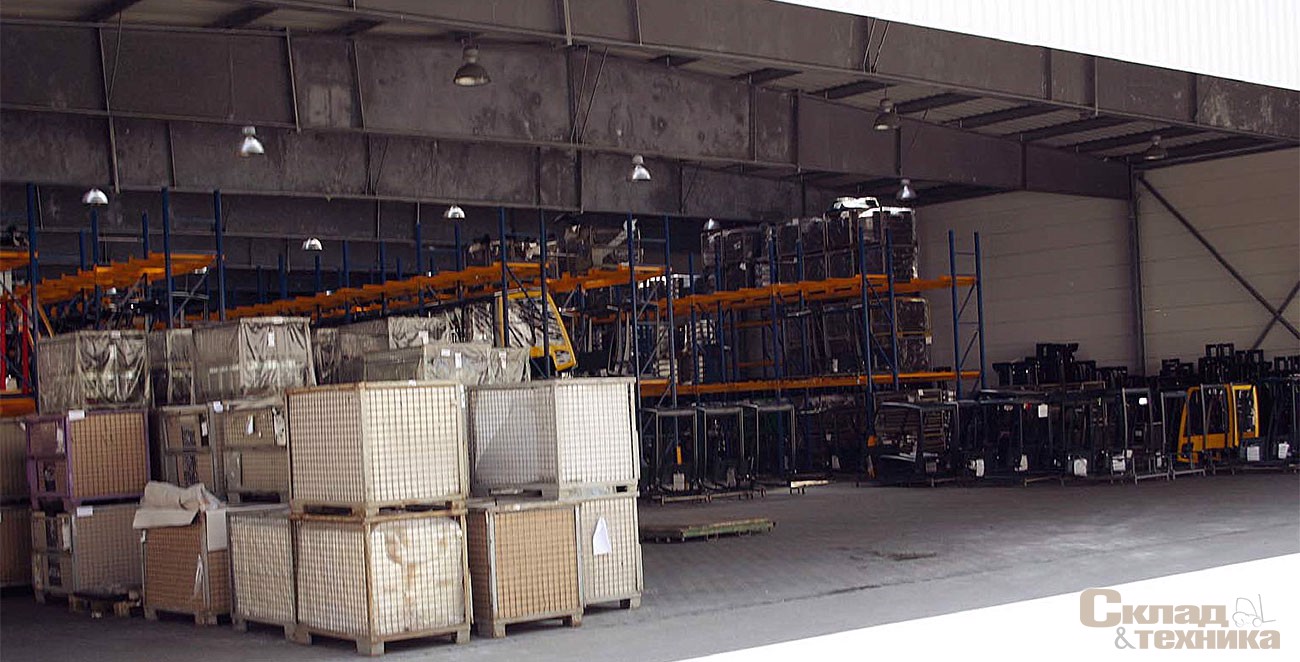
Приёмка продукции. Нормативно-правовое регулирование
До октября 1997 г. действовали инструкции о порядке приемки продукции производственно-технического назначения и товаров народного потребления по количеству, утвержденная постановлением Госарбитража от 15 июня 1965 г. № П-6, и по качеству, утвержденная постановлением Госарбитража СССР от 15.06.1965 № П-7. Инструкции весьма детально регулировали весь процесс приемки продукции, порядок перехода ответственности между контрагентами, порядок составления актов и направления претензий поставщику. Несмотря на то, что документы были приняты давно, бoльшая часть их норм оставалась весьма актуальной. Однако в соответствии с Постановлением Пленума ВАС РФ от 22.10.1997 N 18 (п. 14) их обязательное применение отменено, теперь их применяют только в случаях, когда это предусмотрено договором. В последнее время не принято ни одного документа, который в полной мере регулировал бы процесс приемки продукции. Гражданский кодекс РФ лишь в общих чертах регулирует порядок приемки. Отсутствие императивного регулирования приводит к тому, что в договорах поставки данный процесс, как правило, не фиксируется вообще, и в случае обнаружения в процессе приемки недолжного количества или качества, несоответствия ассортимента, нарушенной упаковки разногласия либо не разрешаются вообще, либо решаются на основе личной договоренности представителей компаний, что зачастую приводит к негативному результату для одного из контрагентов.
Исключение составляет ряд компаний, которые достаточно детально описали в договоре поставки условия приемки продукции или зафиксировали в договоре ссылки на Инструкции П-6, П-7 или на внутренние нормативные акты, с условиями которых была ознакомлена другая сторона. К таким компаниям относятся METRO Cash&Carry, а также ряд других торговых сетей и предприятий.
Операции, выполняемые в процессе приёмки продукции
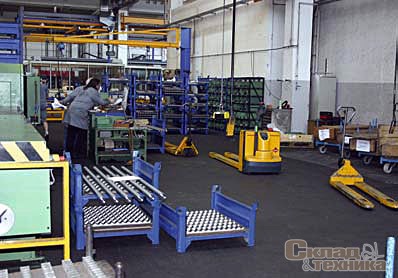
Проверка сопроводительной документации. При приходе транспортных средств на склад получателя в первую очередь проверяют наличие сопроводительных документов (товарно-транспортной накладной, счета-фактуры, технического паспорта, сертификата соответствия ГОСТу, удостоверения о качестве и др.) и их содержание на предмет соответствия условиям (количество, ассортимент, упаковка и т. д.), зафиксированным в договоре поставки. Если основные товарно-сопроводительные документы для приемки продукции отсутствуют, необходимо составить акт о фактическом наличии продукции, который впоследствии подписывают обе стороны, участвующие в приемке. Если отсутствуют дополнительные документы, делают соответствующую отметку в товарно-транспортной накладной.
Определение сохранности внешнего вида транспортного средства, тары и упаковки. Следует проверить наличие на транспортных средствах или на контейнерах пломб отправителя или пункта отправления, исправность пломб, оттиски на них, состояние транспортного средства, исправность тары. В случае обнаружения внешних или внутренних механических или технологических (например, нарушение температурного режима в рефрижераторе) повреждений транспортных средств, а также отсутствия или неисправности пломб, необходимо сделать отметку об этом в товарно-транспортной накладной либо, что более удобно, составить акт об осмотре состояния транспортных средств. Также, если есть возможность, рекомендуется сфотографировать явно видимые повреждения транспортных средств (панорамная и детальная съемка). Сделанные таким образом фотографии имеют большое влияние на поведение поставщика или транспортно-экспедиторской компании в случае требования замены бракованного товара или денежной компенсации. В России за последнее время такая практика находит все большее применение, а, например, в Прибалтике фотографирование транспортных средств и бракованных товаров широко используется уже достаточно давно.
Разгрузка транспортных средств. В процессе разгрузки одновременно проводят подсчет количества поступившего товара. Подсчет необходимо вести в единицах, указанных в товарно-сопроводительной документации.
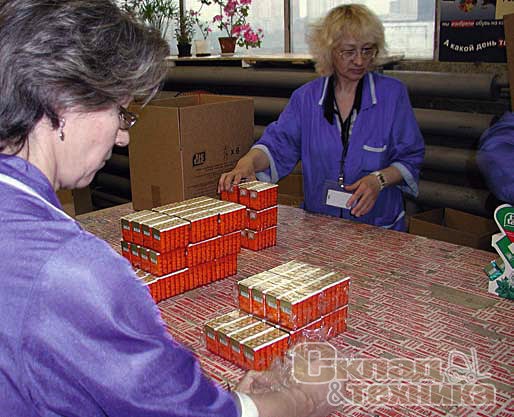
Проверка количества поступившего товара. При необходимости проверку количества проводят в каждом грузовом месте. При обнаружении недостачи составляют акт о приемке продукции, в котором указывают: номер транспортной накладной и счета-фактуры, количество недостающего товара, его общую стоимость, предполагаемые причины недостачи, лиц, участвующих в приемке, их подписи и дату составления акта. Если одна из сторон не согласна с содержанием акта, ей предоставляется право дополнительно зафиксировать в акте свое мнение. После обнаружения недостачи и составления акта необходимо уведомить поставщика о результатах приемки.
Приемка продукции по качеству и комплектности. В зависимости от условий, зафиксированных в договоре поставки, приемка продукции по качеству может проводиться с применением частичной или полной выборки товаров. Выборочная (частичная) проверка качества продукции с распространением результатов проверки качества какой-либо части продукции на всю партию допускается в случаях, когда это предусмотрено стандартами, техническими условиями, особыми условиями поставки, другими обязательными правилами или договором. При обнаружении несоответствия качества поступившей продукции склад обязан приостановить дальнейшую приемку продукции и составить акт, в котором указывается количество осмотренной продукции и характер выявленных при приемке дефектов. После этого получатель должен уведомить поставщика об обнаружении при приемке продукции недолжного качества. В зависимости от решения поставщика дальнейшая приемка может проводиться с участием представителя поставщика, с независимым экспертом либо получателем в одностороннем порядке. Следует отметить, что как уведомление поставщика, так и его ответ получателю лучше всего оформлять с помощью телеграммы, так как это прямое доказательство (в отличие от оповещения по телефону) соблюдения обязанности стороной, которая должна произвести уведомление.
Однако работа с телеграфом часто связана с большими временны’ми затратами, в связи с чем наиболее эффективно использовать электронную почту, но с применением электронной цифровой подписи.

После составления акта составляют претензионное письмо (с целью допоставки товара с должным качеством или возмещения в денежном эквиваленте), которое должно содержать: наименование и адрес предприятия, которому адресована претензия, указание партии товара, количество бракованного товара, стоимость бракованного товара, номер и дату акта о приемке продукции, содержание самого требования (допоставить товар взамен бракованного, оплатить стоимость бракованного товара, др.). В приложении к письму необходимо предоставить копию акта о приемке, копию счета-фактуры, копию товарно-транспортной накладной, копию телеграммы (письма) об уведомлении предприятия-поставщика. Заключительная часть претензионного письма содержит дату, подпись руководителя предприятия, полное наименование предприятия.
Скрытые недостатки продукции. Среди большинства сотрудников складов и отделов снабжения бытует мнение, что претензии по недолжному качеству поступившей продукции можно предъявлять только в процессе приемки продукции либо непосредственно по ее окончании, но это далеко не так. В гражданском законодательстве РФ предусмотрена возможность предъявить претензии к предприятию-поставщику и в случае обнаружения скрытых недостатков продукции. Скрытыми признаются такие недостатки, которые не могли быть обнаружены при обычной для данного вида продукции проверке и которые выявлены лишь в процессе обработки, подготовки к монтажу, в процессе монтажа, испытания, использования и хранения продукции на складе.
В связи с этим склады предприятий имеют право независимо от проверки качества товаров, проведенной ими в сроки, указанные в договоре или ином документе, актировать скрытые недостатки продукции, если таковые будут обнаружены в течение 4 месяцев после получения товаров. Акт о скрытых недостатках продукции должен быть составлен в течение 5 дней после обнаружения недостатков, но не позднее 4 месяцев со дня поступления продукции на склад получателя, обнаружившего скрытые недостатки.
После завершения всех операций, связанных непосредственно с приемкой продукции, оформляют товар на хранение с занесением всей необходимой информации в информационную систему. Далее проводят операции по идентификации продукции и размещению продукции на хранение.
Идентификация
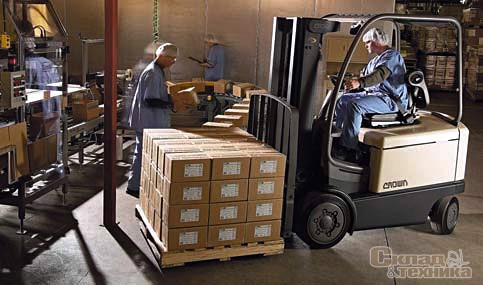
Безусловно, нет необходимости объяснять значимость такой операции, как идентификация поступающей продукции, ведь если ее не проводить, любой склад просто «задохнется», так как в дальнейшем невозможно будет осуществлять ни учет и контроль за движением и состоянием продукции на складе, ни его поиск при комплектации и инвентаризации. Однако к выбору метода идентификации следует подходить, тщательно взвесив задачи, стоящие перед складом, его технико-технологические и финансовые возможности, природу товарного ассортимента и многое другое. В своей практике мы встречали объекты, где идентификация практически не проводилась вообще, а точнее, к периодически присутствующим ярлыкам производителя на коробах и паллетах грузчики подручными средствами «дорисовывали» им одним понятные символы и обозначения, что, естественно, в дальнейшем приводило к путанице. Как правило, проблему пытались разрешить резким, необдуманным введением штрихового кодирования, что в 80% случаев приводило к неэффективным затратам, так как склады изначально не были подготовлены к внедрению этого метода – не было технико-технологических возможностей для выполнения данных операций. Отсутствовало и должное программное обеспечение. Таким образом, эффективность операций по идентификации продукции на складах сводилась к нулю. В связи с этим мы рассмотрим три основных метода идентификации в складском технологическом процессе, каждый из которых может быть эффективен в зависимости от возможностей конкретного склада, целей и задач, стоящих перед ним.
Индивидуальное кодирование. Это наиболее простой метод идентификации, предполагающий минимальные затраты на его внедрение и использование. Сущность индивидуального кодирования заключается в следующем: каждой товарной позиции присваивается индивидуальный код, который может содержать в себе информацию («смысловой» код), а может не нести никакой информации («не смысловое» кодирование). При разработке «смыслового» кода необходимо определить, какая информация является важнейшей и требует сохранения в коде. Например, создается девятизначный код, содержащий информацию о поставщике (первые три цифры), информацию о товарной группе (две цифры) и товарной позиции (три цифры), о статусе данного товара (например, о его ценности, порядке хранения и проч.). Пример структуры индивидуального смыслового кода приведен на рис. 5.
![[b]Рис. 5.[/b] Пример структуры индивидуального смыслового кода](/article/10169-optimizatsiya-tehnologicheskogo-protsessa-na-sklade/Images/11.jpg)
Абсолютно не обязательно знать структуру кода оперативным работникам – грузчикам, комплектовщикам и др. Важно, чтобы структура кода и значение каждой цифры были зафиксированы в нормативном документе предприятия и руководитель склада, его заместители или другие лица при необходимости всегда могли расшифровать информацию по конкретной грузовой единице. Основной целью данного вида идентификации является возможность учета продукции на складе, ее индивидуализации при комплектации заказов. Аналогичную функцию носит и «не смысловое» кодирование, когда каждой товарной позиции присваивается свой номер, что позволяет индивидуализировать ее среди другой продукции при однородном внешнем виде.
Стоимость внедрения и использования этого метода не высока. Как правило, в затраты на введение индивидуального кодирования включается только закупка этикеточной ленты и печать на ней кода товаров, а также закупка нескольких этикет-пистолетов. Ярлык (этикетку) с напечатанным на ней кодом товарной позиции наклеивают с помощью этикет-пистолета на каждую грузовую единицу по завершении операций приемки продукции и ее сортировки.
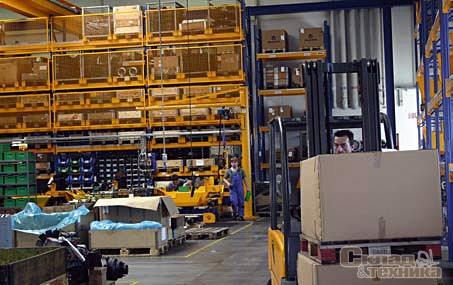
Штриховое кодирование (ШК). Внедрение ШК на складе позволяет существенно ускорить процесс приемки продукции (в случае, если на поступающих грузовых единицах уже имеется штрих-код), значительно снизить влияние человеческого фактора в процессе выполнения технологических операций и при инвентаризации, упростить поиск (определение) нужного товара на стеллаже или в стеллажной ячейке. Внедрение ШК обосновывается и тем, что все чаще крупные клиенты торговых и производственных компаний ставят его наличие обязательным условием при закупках продукции. Однако внедрение системы ШК влечет за собой серьезные основные и дополнительные затраты. К основным затратам относится закупка оборудования (терминалы сбора данных, сканеры, сервер, принтер для печати этикеток), программного обеспечения, совместимого с системой ШК, оплата услуг и взносов в Ассоциацию Юнискан/EAN. К дополнительным затратам можно отнести обучение персонала, услуги консультантов по подготовке склада к внедрению ШК и проч.
Радиочастотная идентификация (RFID). Система RFID появилась сравнительно недавно и в настоящее время на российских складах практически не используется, однако успешный опыт внедрения этой системы рядом крупных компаний в Европе (в частности, в Италии и Германии) позволяет сделать вывод, что в среднесрочной перспективе широкое применение системы RFID начнется и в России.
![[b]Рис. 6.[/b] Элементы системы радиочастотной идентификации](/article/10169-optimizatsiya-tehnologicheskogo-protsessa-na-sklade/Images/12.jpg)
Система RFID состоит из трех элементов – метка (tag), антенна (reader) и компьютер (рис. 6).
В метку заносятся необходимые данные о грузовой единице, после чего данные метки могут передаваться в компьютер с помощью антенны.
Преимущества RFID:
- данные идентификационной метки можно менять и дополнять;
- на метку можно записать гораздо больше данных по сравнению со штрих-кодом;
- данные на метке могут быть засекречены;
- радиочастотные метки более долговечны;
- расположение метки не имеет значения для считывания (метка может находиться внутри короба или паллеты);
- метка лучше защищена от воздействия окружающей среды;
- метки могут быть многоразового использования;
- при использовании RFID появляется возможность контролировать перемещения груза.
Недостатки RFID:
- относительно высокая стоимость;
- невозможность размещения под металлическими и электропроводными поверхностями;
- подверженность помехам в виде электромагнитных полей;
- возможность только локального использования.
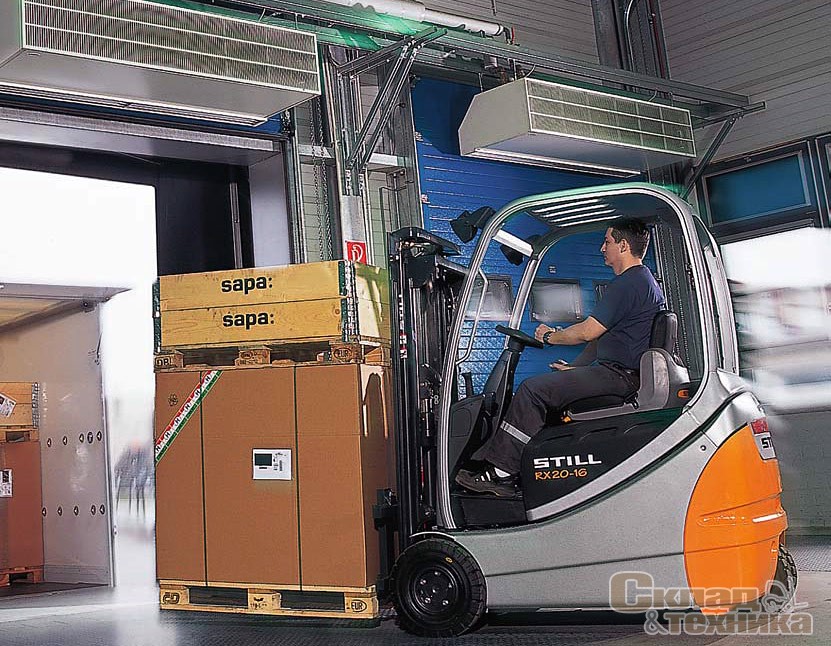