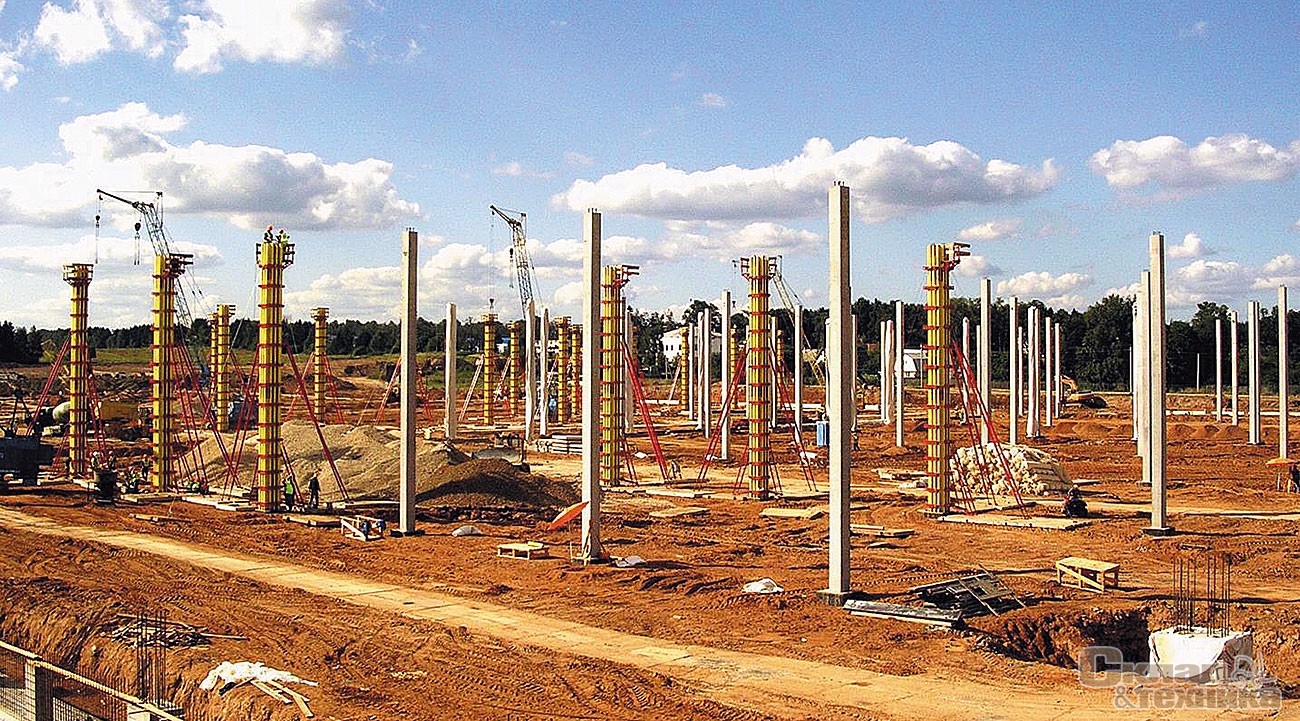
Особенности реконструкции и запуска склада в эксплуатацию в условиях современной экономики
В условиях прогрессирующего кризиса экономики основной стратегией выживания для бизнеса является снижение эксплуатационных затрат. Это подталкивает как торговлю, так и дистрибуционные компании к снижению нормативов запасов и удешевлению эксплуатации логистических процессов
Однако в большинстве своем существующие складские комплексы низкотехнологичны и затратны в эксплуатации, поэтому и реализовать такие планы весьма проблематично. Эта ситуация осложняется еще и тем, что даже при общем снижении объемов товаропотоков нарастают тенденции к росту количества заказов от конечных потребителей. При этом структура заказа стремительно смещается в сторону все более мелких единиц – отдельных штук и небольших коробок. Но подбор и последующая подготовка к отгрузке таких заказов в рамках привычных сегодня технологий требуют экстенсивного развития склада, что в свою очередь приводит к росту численности производственного персонала и все большему использованию ручного труда. А это требует увеличения фонда оплаты труда, налоговых отчислений, размеров административно-бытового комплекса, потребления тепла, энергии и пр., т. е. резкого повышения эксплуатационных затрат на складе. Таким образом, нарастают тенденции к снижению эффективности склада!
Опыт общения с руководителями складов показывает, что этим тенденциям не уделяется должное внимание. Но если проанализировать структуру затрат на эксплуатацию склада и построить графики изменения расходных и доходных характеристик его экономики во времени, то можно убедиться, что к моменту достижения так называемой «точки безубыточности» сумма накопленных эксплуатационных затрат в несколько раз превысит объем начальных капитальных вложений*.
*См. статью автора «Внутренняя логистика склада в условиях кризиса экономики» в журнале «СиТ», № 4, 2009 г.

Из этого можно сделать простой вывод: рост конкурентоспособности компании в значительной степени зависит от грамотного подхода к анализу ситуации на складе и разработке программы его модернизации. Учитывая, что складской комплекс – это сложный организм, при своей реконструкции требующий системного подхода и тонкой увязки составляющих его элементов, на передний план выходит знание методологии реализации инновационных проектов, современных технологий обработки товаропотоков и оборудования для их реализации. Крайне важно понимать методологию (суть и последовательность шагов) разработки проекта строительства или же модернизации (реконструкции) складского комплекса. Результатом этих шагов станет технологическая и конструкционная концепция склада.
Колоссальное влияние на обеспечение качества выполняемых на складе работ и на общую эффективность технологии оказывает грамотный выбор типа и модели системы управления складом – WMS. Доля расходов на эту систему в капитальных затратах не превышает 10–12% при модернизации существующего склада или же 4–6% при строительстве нового, но при этом она более чем на 50% может повысить эффективность эксплуатации технологии.
Любые планы модернизации не могут рассматриваться всерьез без анализа их экономических характеристик. Выбор технологии и оборудования для реконструируемого склада должен базироваться на расчете капитальных и, главное (!), эксплуатационных затрат, а также на анализе сроков достижения так назывемой «точки безубыточности», для чего необходим расчет еще и доходной части бюджета.
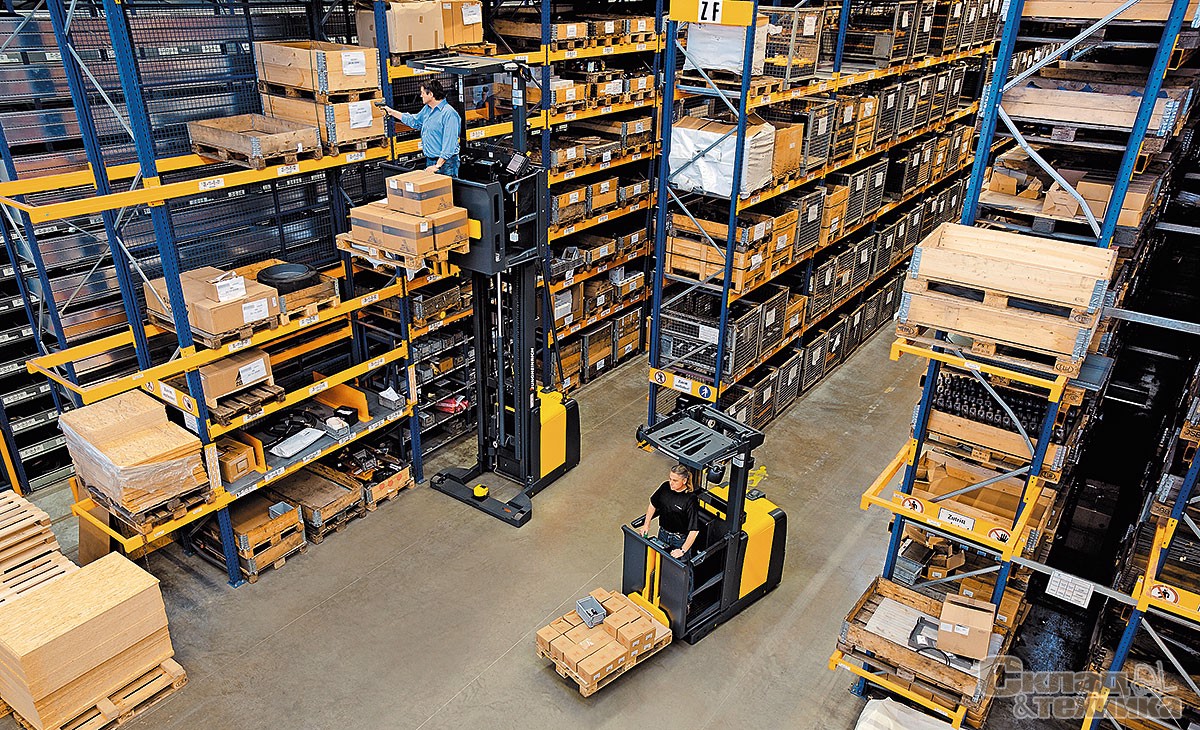
Затронутые выше вопросы отнюдь не исчерпывают весь список проблем, стоящих перед руководителями логистических служб компаний, и, как бы нам ни хотелось дать набор простых рекомендаций по их решению, умещающихся в одной статье, придется признать, что сделать это невозможно.
Поэтому возникла идея подготовки цикла статей, которые могли бы всесторонне проанализировать процесс строительства нового или же реконструкции существующего склада. При подготовке их будет использован опыт автора, полученный при выполнении более 100 аудитов действующих складов, эскизно-технологических проектов строительства складских комплексов и проведении открытых и корпоративных семинаров (тренингов, мастер-классов) в 2001–2009 гг. в России, на Украине, в Белоруссии, Казахстане, Азербайджане, странах Прибалтики. Надо сказать, что фраза, сказанная нашим великим поэтом много лет назад «…и опыт, сын ошибок трудных…», полностью соответствует современным реалиям. Но в процессе накопления этого опыта вырабатывались весьма нестандартные правила проектирования и взаимоотношений с заказчиками. Более того, в ряде случаев они противоречат существующим традициям управления процессами проектирования и строительства, но тем не менее показали свою эффективность. Давайте попробуем сформулировать эти правила.
Речь идет о двух параллельных процессах – собственно процессе реализации склада по этапам «выбор концепции реконструкции логистических процессов – проектирование складского комплекса – его строительство – оборудование – запуск в эксплуатацию» и сопровождающих эти шаги специальных проектах (cм. схему).
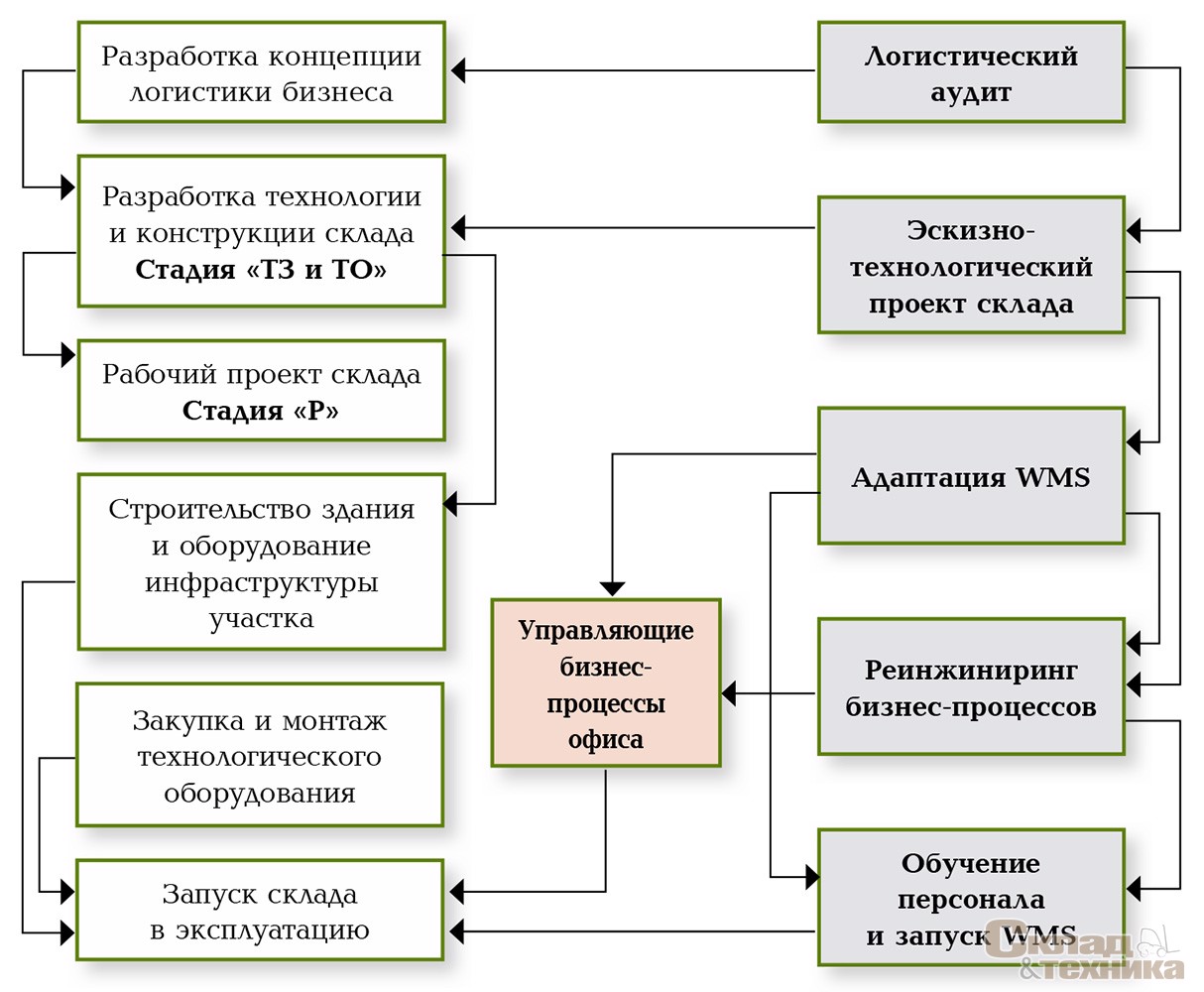
Правило № 1. Не пренебрегайте логистическим аудитом. К сожалению, выработка концепции создания или же реорганизации логистических процессов, обеспечивающих бизнес, очень часто выполняется без должных обоснований, на основе имеющегося личного опыта или же эмоций. Здравый смысл подсказывает, что на этом этапе до принятия концептуального решения абсолютно необходимо проведение так называемого «логистического аудита». Для существующего и модернизируемого бизнеса этот процесс включает в себя следующие шаги:
- анализ характеристик товарных потоков, которые обрабатываются в складском комплексе;
- изучение планировки, инфраструктуры участка и транспортных магистралей;
- изучение планировки и конструкции здания склада и его помещений;
- изучение применяемой технологии хранения и обработки товаропотоков, используемого в ней оборудования;
- разработка двух-трех вариантов концепции модернизации технологии, оборудования и выбора необходимой WMS, оценка необходимости реконструкции здания склада;
- разработка укрупненных поточной и экономико-математической моделей для получения эксплуатационных и экономических характеристик вариантов склада.
Анализ потоков является основой для всех дальнейших процессов проектирования, так как склад – это не здание, построенное на определенном участке, а станок по переработке товарных потоков. Сложность анализа потоков заключается в огромных размерах файлов данных (иногда до нескольких гигабайт), потребности в подробном справочнике товаров и наличии специального программного обеспечения с весьма специфическими алгоритмами. В одной из следующих статей рассмотрим эти проблемы подробно. Можно, конечно, попытаться обойтись динамикой изменения объемных характеристик потоков во времени, но это резко снизит качество анализа.
При проведении аудита для вновь строящегося объекта последовательность шагов будет почти такой же. Если склад создается для нового бизнеса, не имеющего истории потоков, либо для оказания логистических услуг сторонним заказчикам, то расчетные потоки придется «создать», исходя из понимания сути планируемого бизнеса и ряда принципиальных договоренностей о типах товаров и условиях их хранения и обработки. Существенную помощь окажет грамотное маркетологическое исследование рынка в регионе. Этапы 3 и 4 из вышеприведенного перечня придется выполнять, основываясь на размерах участка под строительство и величинах расчетных потоков. Фактически решается так называемая «обратная» задача – определение максимально возможных для данного участка характеристик склада при данном выбранном варианте технологии. А затем мы сравниваем их с требуемыми параметрами.
В любом случае результатом логистического аудита станет обоснованная концепция модернизации склада.
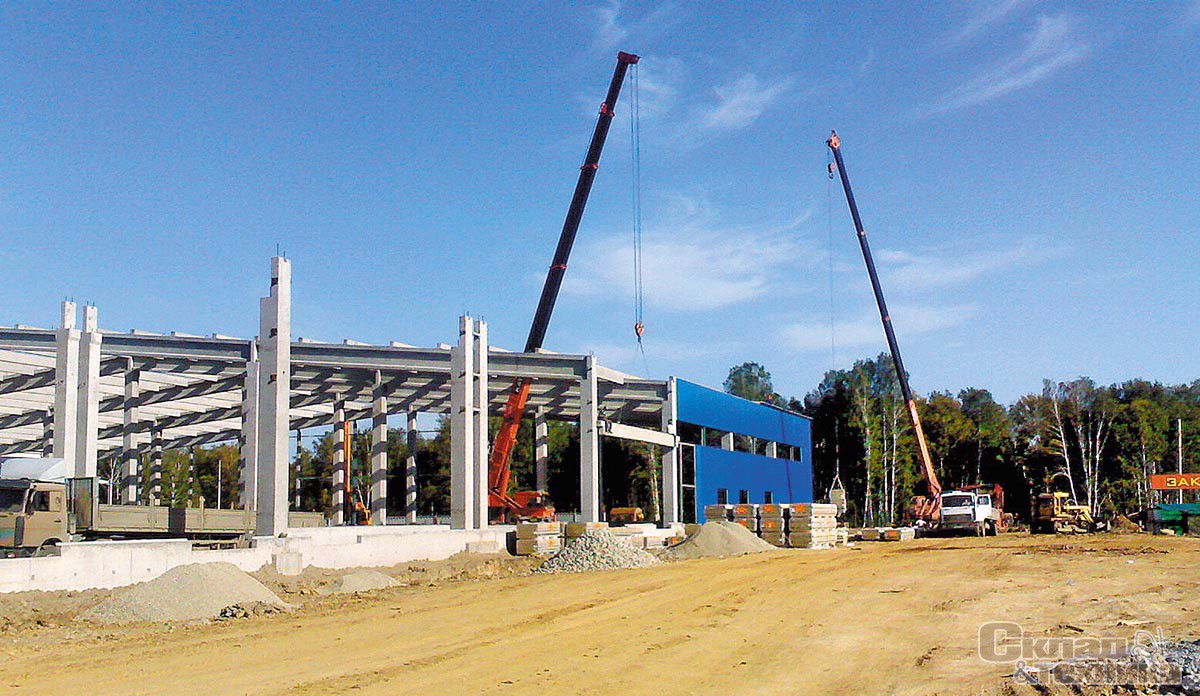
Правило № 2. Не экономьте на математическом моделировании. Второй критической проблемой как логистического аудита, так и эскизно-технологического проектирования является потребность в двух специальных моделях – так называемой поточной и экономико-математической. Поточная модель даст возможность описать выбранную для конкретного варианта технологию процессов обработки товаропотоков и оптимизировать количество единиц техники и производственного персонала. Экономико-математическая модель на основании выбранной технологии и типах оборудования и рассчитанном исходя из поточной модели их количестве даст оценку капитальных и эксплуатационных затрат и позволит оценить эффективность технологии. Обычной ошибкой является попытка использовать простые формулы, связывающие количественные объем и вес товаров с площадью зон склада и нужным количеством техники, персонала с помощью некоторых коэффициентов, подсчитанных кем-то на каких-то проектах. Однако вероятность того, что ваш новый проект совпадает с тем старым, по которому были получены эти коэффициенты, весьма мала. Не могу утверждать, что склад, спроектированный с использованием такой «коэффициентной» методики, не будет функционировать. Но почти наверняка он будет работать неоптимально и потребует значительных дополнительных усилий по доводке.
Имея разработанную концепцию логистического решения складского комплекса, можно провести разработку «Эскизно-технологического проекта» склада (иначе – ТЗ и ТЭО). Этот этап подробно отражен в соответствующих СНиПах, на основании которых от владельца склада (заказчика-застройщика) требуется предоставление ТЗ для проектирования, согласования и строительства. При создании этого документа возникает несколько проблем, опыт решения которых также привел к возникновению набора правил.
Правило № 3. Не экономьте на консультантах. Редкий заказчик может сделать эскизно-технологический проект требуемого состава и качества самостоятельно. Поэтому, осознав тщетность усилий в области самодеятельного проектирования, он вынужден приглашать консультантов. В качестве них чаще всего выступают либо поставщики какой-либо складской техники (стеллажной, подъемно-погрузочной и т. п.), либо так называемые «независимые консультанты» – проектировщики. Мотивация принимаемых решений при этих двух подходах будет весьма различна. Первым надо продать свое оборудование, поэтому вся технологическая часть проекта делается под него. Кроме того, далеко не все поставщики техники (особенно если это не крупная фирма-производитель) имеют специализированные подразделения по проектированию технологической части проекта. Вторым выгодно спроектировать максимально эффективный склад, рекомендуя те типы оборудования (и перечень их возможных поставщиков), которые в наибольшей степени соответствуют выбранной технологии склада и обеспечат максимальную эффективность его эксплуатации. А уже дело заказчика – проводить тендеры и выбирать.
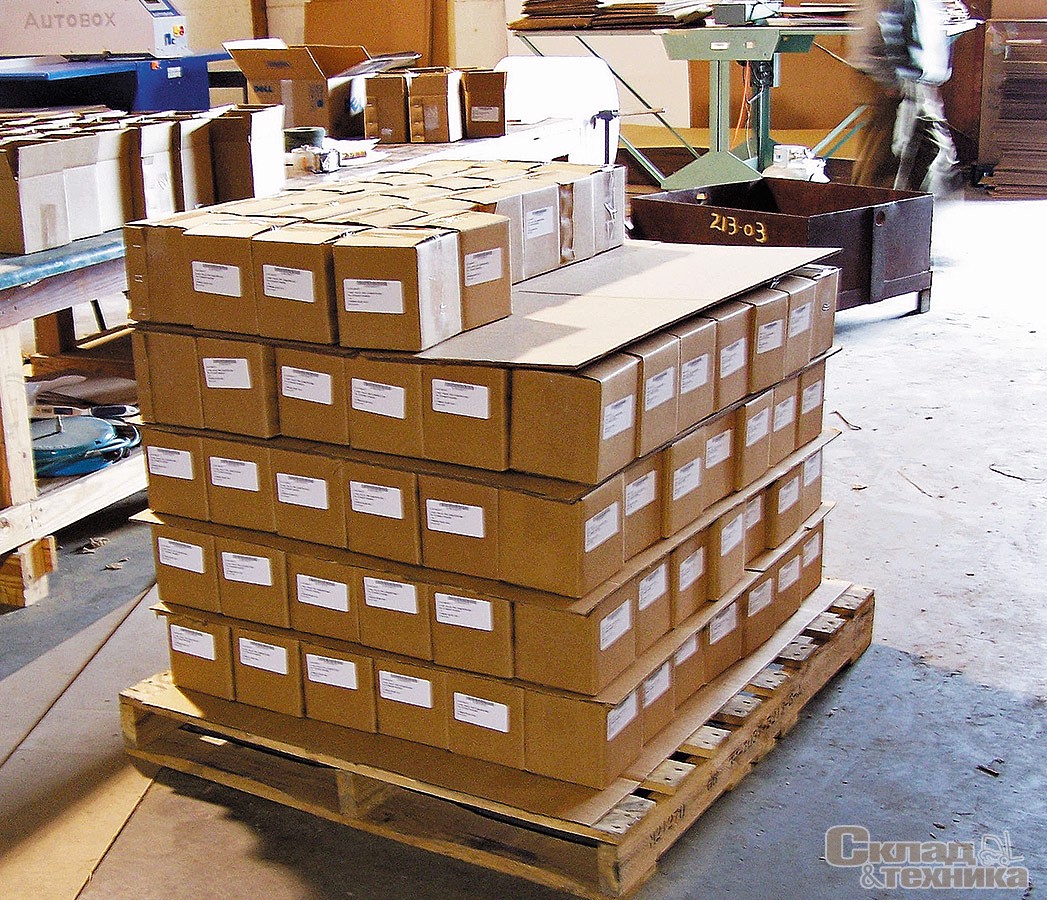
Правило № 4. Изучайте методологию проектирования складского комплекса. Выбор консультанта сродни выбору врача при тяжелом заболевании. Как правило, мы мало что понимаем в медицине и ищем врача, имеющего опыт лечения (практику!) и способного доходчиво объяснить, что и как он будет с нами делать.
К счастью, рассматриваемый нами предмет все-таки проще, чем человеческий организм, и, изучив его в общем виде и поняв методологию процесса его проектирования, можно не только выбрать консультанта, устроив ему маленький экзамен, но и грамотно участвовать в процессе проектирования, контролируя этапы проекта, их результаты и принимая взвешенные решения. Знание методологии проектирования нужно еще и потому, что представители заказчика должны непрерывно общаться с проектировщиками, снабжать их необходимой информацией и принимать участие в оперативных обсуждениях возникающих идей и проблем. Речь не идет о мелочном контроле. Ведь качественный проект – залог эффективной эксплуатации склада, и нет смысла становиться на позицию «Я тебе плачу – вот ты и работай!». Не надо забывать, что склад является сложнейшим объектом, подверженным воздействию большого числа факторов и абсолютно идеального решения быть не может. Мы всегда ищем компромисс между желаемым и возможным. А это двусторонний процесс.
Остался маленький вопрос – что нужно сделать, чтобы изучить методологию проектирования? Конечно, не помешает прочитать несколько учебников по логистике складов. Сейчас на эту тему выпущено более двух десятков изданий различного уровня. К сожалению, многие из них ориентированы на учебный процесс в вузах и грешат одним недостатком, который в одной из старинных поговорок сформулирован так: «Из-за деревьев леса не видно!» С «деревьями», т. е. конкретикой по различным видам оборудования и конструкций, все в порядке. А вот как они связаны между собой в различных типах технологий (т. е. как выглядит весь «лес» как объект) – непонятно. Это типичное отсутствие системного подхода к построению сложных (и больших!) систем.
Помимо чтения учебников большим подспорьем окажется участие в так называемых практических семинарах по внутренней логистике склада, которые организуют различные учебные организации. Хороший результат дают корпоративные семинары, на которые обычно приглашают практиков – проектировщиков складских комплексов. Это может оказаться особенно эффективным, если совмещать такой корпоратив с аудитом существующего складского комплекса.
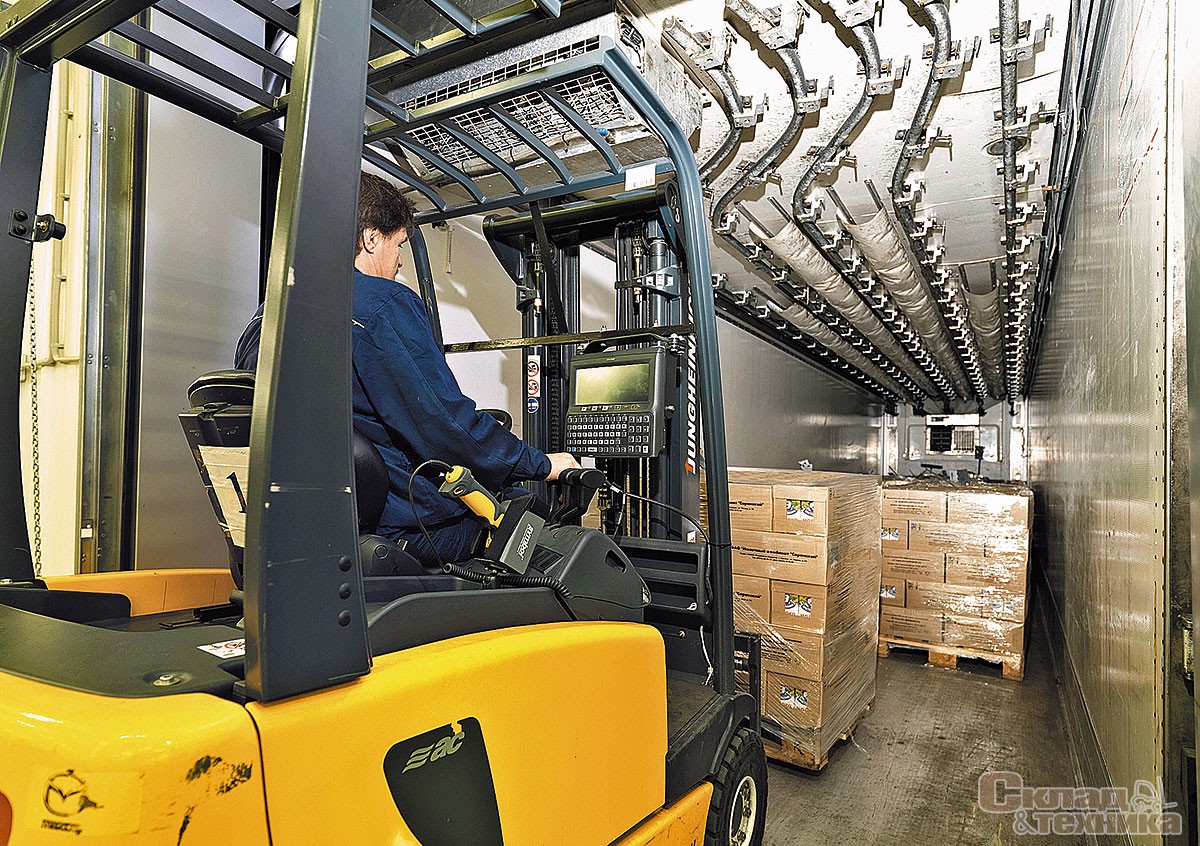
Правило № 5. Выбирайте поставщика WMS в процессе разработки технологического проекта. Одним из важнейших результатов технологического проекта является пошаговое описание технологического процесса обработки товарного потока. Управление операциями технологии в современных складах ведется с использованием автоматизированной системы управления. Каждой операции спроектированной технологии должна соответствовать специальная функция, запрограммированная в WMS, поэтому одним из основных критериев выбора типа и ее модели (а значит, и ее поставщика) является полное функциональное соответствие технологического проекта и выбираемой WMS.
Обычной практикой является проведение тендера на закупку WMS после завершения этапа технологического проектирования. Однако в процессе настройки системы (так называемой адаптации) может потребоваться не только параметрическая настройка WMS, но и изменение программы в каких-то функциях или же написание новых функций. Такая необходимость возникает при отсутствии всего перечня требуемых функций в стандартном или же дополнительном списке опций. Этот процесс обычно называют «кастомизация». Он может иногда существенно увеличить стоимость и время подготовки WMS к внедрению и даже привести к труднопредсказуемым сбоям в процессе эксплуатации, казалось бы, хорошо отлаженной системы. Поэтому выгоднее выбрать поставщика WMS и ее модель в процессе технологического проектирования сразу же после того, как выбран конкретный вариант технологии и оборудование. Тогда совместная работа разработчиков-технологов и внедренцев WMS даст наилучший результат и позволит сэкономить время и деньги. Ведь технологу иногда проще изменить постановку задачи, чем влезать в кастомизацию. Это вовсе не значит, что проектировщик-технолог должен заниматься протекционизмом. Просто тендер по выбору этой критически важной системы нужно сдвинуть во времени. В обязанность консультанта входит представление заказчику нескольких возможных WMS и организация контактов с их поставщиками.
Правило № 6. Выбирайте проектировщика здания склада в процессе разработки технологического проекта. Складское здание является достаточно простым строением, поэтому в практике технологического проектирования часто ограничиваются рисованием различных планировок – как здания самого склада, так и расположения его на участке. Остальная часть работы передается архитекторам и рабочим-проектировщикам. Для экономических же оценок пользуются некоей «среднерыночной» стоимостью 1 м2, что выглядит так же странно, как использование в медицинской практике такого показателя, как «средняя температура по госпиталю». А в современных экономических условиях, при резко меняющихся на все ценах, такой подход вовсе недопустим.
Из этого следует простой вывод – на этапе технологического проектирования надо привлечь конкретную архитектурно-проектную фирму. Это позволит не только избежать тривиальных ошибок в планировках и более точно учесть ограничения СНиП, СанПиН, правил пожарной безопасности, но и договориться с проектировщиками здания и инфраструктуры участка о размерностях и источниках различных ресурсов, требуемых для эксплуатации склада. Информация о типах современного инженерного оборудования здания, их стоимости, расценках на строительные и монтажные материалы, стоимости ресурсов (энергия, вода, тепло, уровни зарплат и т. д.) позволят достаточно точно выполнить как сам проект с необходимыми планами, сечениями и разрезами, так и подготовить бюджет проекта. Этот бюджет помимо оценки стоимости капитальных затрат и плана-графика платежей для строительства, закупки и установки оборудования послужит базисом экономико-математического моделирования работы проектируемого склада. Конечно, грамотный технолог-консультант должен учитывать все эти особенности проектирования. Но тот же опыт, о котором мы говорили выше, подсказывает, что наилучший результат достигается при кооперации усилий.
Если на этом же этапе выбрать еще и конкретную строительную компанию, то все сказанное выше уточнится в еще большей степени. А если архитектурно-проектная и строительная фирмы имеют опыт совместной работы на предыдущих объектах, то сроки и стоимость реализации проекта могут быть значительно сокращены.
Все, что было сказано об условиях проведения тендеров для выбора WMS, применимо и в этой части.
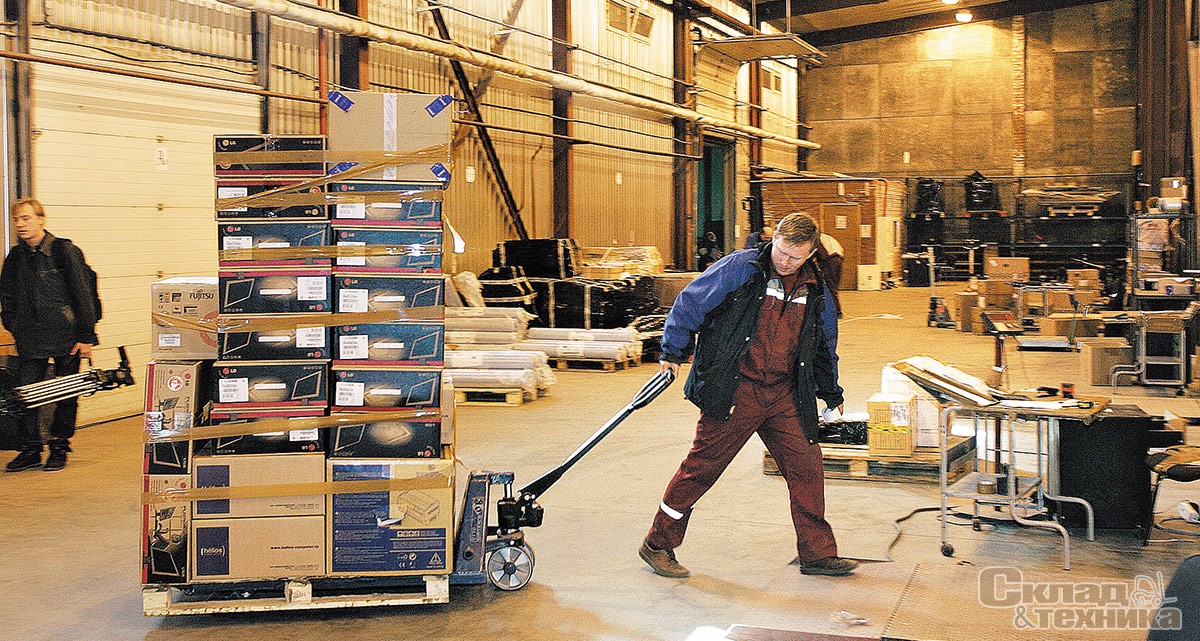
Правило № 7. Реинжиниринг бизнес-процессов в офисе делать придется. Но не на этапе технологического проектирования! Ничто в природе не существует изолированно. Поэтому, поставив перед собой задачу повышения эффективности логистики компании и решая ее часть, касающуюся внутренней логистики складского комплекса, надо понимать, что придется обратить внимание и на процедуры управления этим новым, модернизированным объектом со стороны офиса компании.
Обычно оргструктура компании построена по функциональному (тейлористскому) принципу, когда существуют жесткая специализация и подчинение служб в пределах так называемых функциональных зон: бухгалтерия подчиняется финансовому директору и т. д. При этом процессы, протекающие в компании, затрагивают всех, и на границах функциональных зон возникают конфликты, сначала производственные, а затем, естественно, и человеческие. Методы управления бизнесом компании создавались годами и очень часто имеют как «написанные» компоненты, так и те, которые создавались за счет внутренних договоренностей между различными службами и просто специалистами. Эти договоренности в нашей стране имеют специфическое название – «жизнь по понятиям» и часто оказывают большее воздействие на управленческие процессы, чем утвержденные инструкции. Создается некоторый эрзац корпоративной культуры.
Эта методология управления, к сожалению, распространяется и на складские процессы. Но модернизация склада, его технологии требуют использования современной системы управления, о чем уже упоминалось выше. Эта WMS резко сужает зону функционального произвола со стороны офисных служб и отдельных руководителей, ограничивая при этом и их политический вес в компании, и некоторые экономические возможности. И когда эти службы при обсуждении стадий проектирования нового склада начинают осознавать необходимость изменений в управленческом функционале (т. е. в их работе!), мы часто сталкиваемся с жестким сопротивлением планируемым переменам с их стороны, вплоть до попыток остановить процессы модернизации склада. Любая попытка в этот момент начать обсуждение приведения методов и процессов управления офисной частью компании, отвечающей за логистику, в соответствие с планируемой модернизацией склада только усиливает эту конфронтацию.
Практика проектирования показала, что к реинжинирингу бизнес-процессов в офисе желательно приступать тогда, когда уже разработана технология нового склада (т. е. подробно описаны производственные бизнес-процессы), выбрана WMS, заключен договор на ее адаптацию, специалистами-«внедренцами» WMS на основании согласованной технологии подготовлен проект адаптации и, наконец, создана информационная модель базы данных WMS. И вот в этот момент приглашение специалистов по бизнес-процессам вполне своевременно. Они вместе с «вэмээсниками» примут участие в изменении документооборота, разработке управленческих бизнес-процессов, увязанных с технологией склада и написанных на ее основе производственных бизнес-процессов, а возможно, и в создании специальных моделей, наиболее известные из которых – IDEF0, DFD, UML, ARIS. Некоторые из поддерживающих их программных продуктов – Design/IDEF, BPWin, Rational Rose, ARIS Toolset. Все они уже получили широкое распространение в России, к сожалению, только у программистов или в наиболее «продвинутых» компаниях. Но поскольку последних становится все больше, то соответственно продолжается и экспансия методологий. Учитывая большой потенциальный эффект от оптимизации управления бизнесом с использованием таких технологий и явную сочетаемость их с процессом модернизации складов в кризисных условиях сегодняшнего дня, имеет смысл подумать о возможности их внедрения.
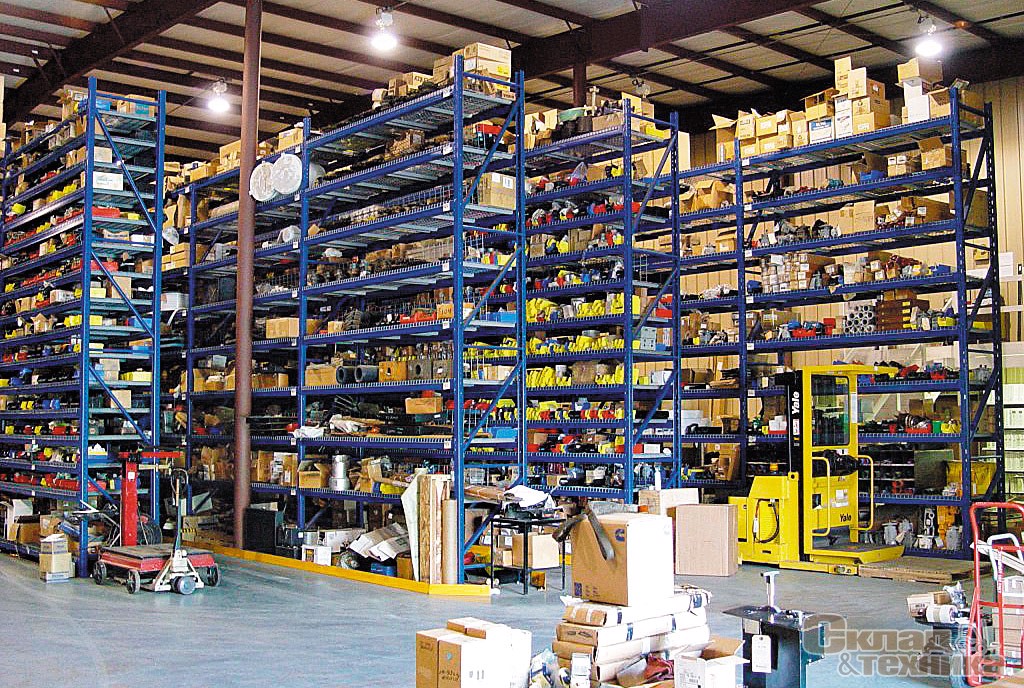
Правило № 8. Готовиться к запуску склада в эксплуатацию надо уже на этапе технологического проектирования. Проводя реконструкцию склада, часто забывают, что потом им придется управлять. Эта фраза кажется парадоксальной, но я слишком часто сталкивался с ситуацией, когда плохая подготовка к началу эксплуатации губит хороший проект. Обычно это происходит из-за того, что не принимается во внимание простая истина: управлять складом – это значит управлять коллективом людей, которые реализуют под жестким контролем современных WMS технологические процессы обработки товаропотоков. А чтобы управлять коллективом, надо сначала создать этот коллектив. И совсем не факт, что имеющиеся на старом складе работники могут сразу же и эффективно включиться в реализацию новой технологии на модернизированном складе. Дело в том, что современная WMS не только по-другому управляет технологией, но и предъявляет иные требования к персоналу. Происходит довольно жесткое деление на уровни по исполняемым функциям: административно-обеспечивающий персонал, менеджеры WMS, руководители процессов (их на практике часто называют надсмотрщиками), исполнители технологических процедур – собственно производственный персонал. Более подробно требования к этим категориям сотрудников будут рассмотрены в одной из следующих статей. Сейчас же хочу остановиться на 2-й и 4-й категориях сотрудников.
Менеджеры системы управления – это люди, реально управляющие технологией склада, хотя в процессе этого управления они склад и в глаза не видят, так как сидят в окружении компьютерных экранов. Как правило, их количество на складе невелико – от 2–4 до 12–15 человек в зависимости от размеров склада и сменности работы. Однако эта группа полностью определяет качество и эффективность оперативного управления складом, поэтому на их отборе и обучении экономить нельзя. Процесс обучения этой группы желательно разбить на два этапа:
- изучение адаптируемой WMS и тренинг под руководством ее поставщика. Желательно делать это на учебном стенде самого поставщика. Речь должна идти не только об управлении спроектированным функционалом, но и всеми обеспечивающими жизнедеятельность системы процессами;
- тренинг на создаваемом макете склада.
На этом последнем этапе уделяется внимание стадии подготовки к началу эксплуатации склада, которая обычно опускается. Нельзя ждать, пока склад будет запущен, и только после этого на реальной аппаратуре и реальных потоках начнинать учить людей новой технологии и используемой технике. Это скорее всего приведет к замедлению процесса запуска и выхода на проектную мощность надолго. Но потоки товаров ждать не будут и ни к чему хорошему это не приведет. Обычный результат – у директората компании не хватает терпения и (от безысходности!) он пытается возвратиться к старым методам управления этой новой, модернизированной и не желающей работать, как раньше, технологией.
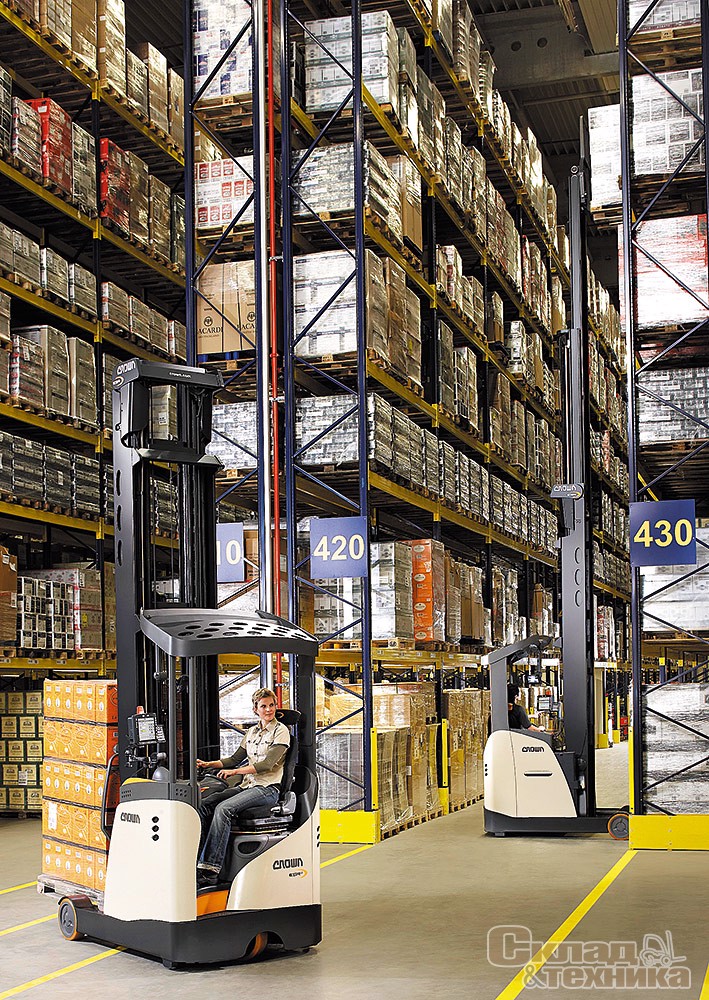
Проблема должна быть решена за счет создания макета склада для проведения тренингов персонала в режиме игры. Никаких особенных затрат такой макет не требует. Нужна не очень большая комната, куда устанавливаются столы с компьютерным оборудованием, которое уже закуплено для эксплуатации на новом складе. Имеются в виду как обычные персоналки, объединенные в локальную сеть, так и специальное оборудование информационных технологий: сканеры штрих-кодов, портативные компьютерные терминалы, специальные принтеры этикеток, средства радиодоступа и т. п. Все это оборудование объединяется в единую систему. В нее загружается купленная WMS и проводится весь процесс первоначальной настройки и отладки. В этом процессе обязательно должны участвовать члены команды менеджеров WMS, уже прошедших к этому этапу тренинг в офисе поставщика программного комплекса. Если же у поставщика нет своего учебного центра, оба тренинга совмещают, проводя их на макете склада. Если это условие отметить в договоре с поставщиком WMS, то помимо внедренцев к обучению работе с системой будут привлечены грамотные методисты, и такой подход окажется вполне логичным.
Не надо забывать, что макетируется не только IT-технология, но и процессы реальной жизни. А для этого в модели должны быть и стеллажи, и поддоны, и коробки с товарами. Должны быть смоделированы зоны склада, их топология и т. д. Все это легко сделать из бумаги, картона и детских кубиков различных размеров, правда, на все элементы нужно наклеить реальные этикетки.
Но основной эффект от макетирования склада получается в процессе тренинга именно производственного персонала. В этой игре на макете операторы получают не только навыки общения с WMS через портативные ручные терминалы со сканерами штриховых кодов, но и опыт по разрешению огромного количества нештатных ситуаций, обычно возникающих при эксплуатации системы. В итоге к началу сдачи склада в эксплуатацию у вас в наличии будет работоспособный коллектив. Дополнительный положительный эффект будет получен после проведения так называемого «гамма-тестирования» WMS на реальной (хотя и смоделированной) технологической ситуации. Это позволит обкатать систему до выхода на обслуживание склада. Если же вовлечь в игру на такой модели подразделения офиса, то эффект многократно увеличится.
Эта методология не новая. Ее применяли в различных отраслях в СССР еще 30–50 лет назад (в чем автор сам многократно участвовал), но настораживает то, что при проведении семинаров по внутренней логистике складов положительный ответ на вопрос об использовании таких методов дают не более 3–5% фирм-участников.
Набор приведенных правил невелик. Их реализация не требует значительных дополнительных капитальных вложений. Достаточно просто следовать здравому смыслу и иметь желание достичь наилучшего конечного результата.
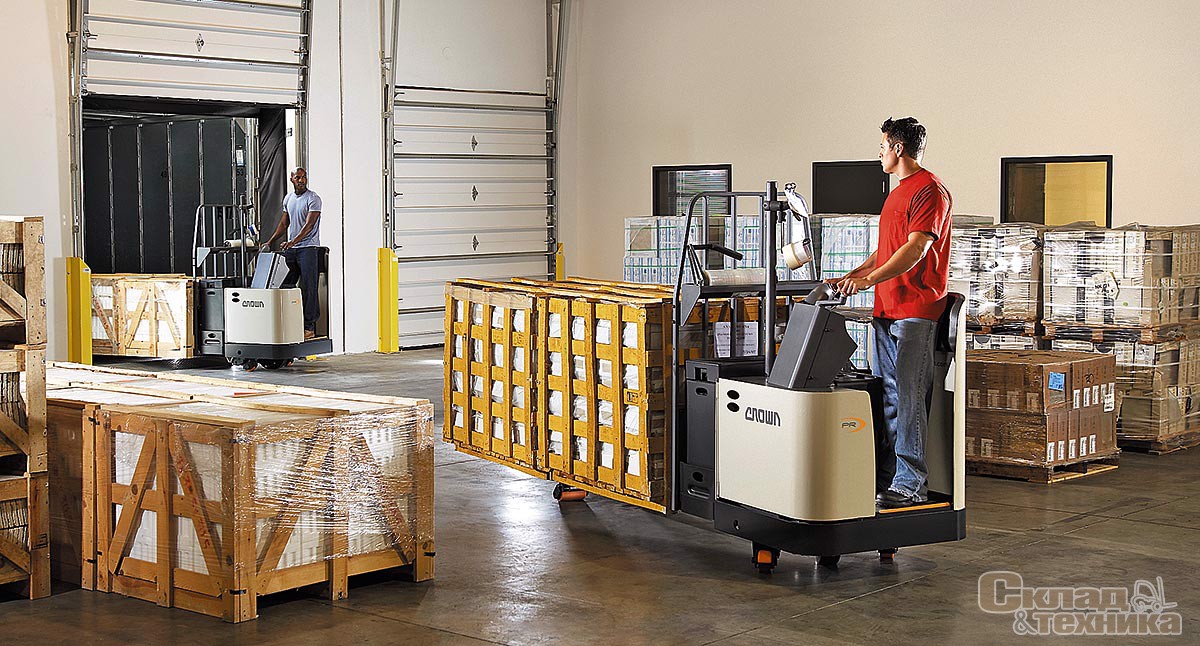