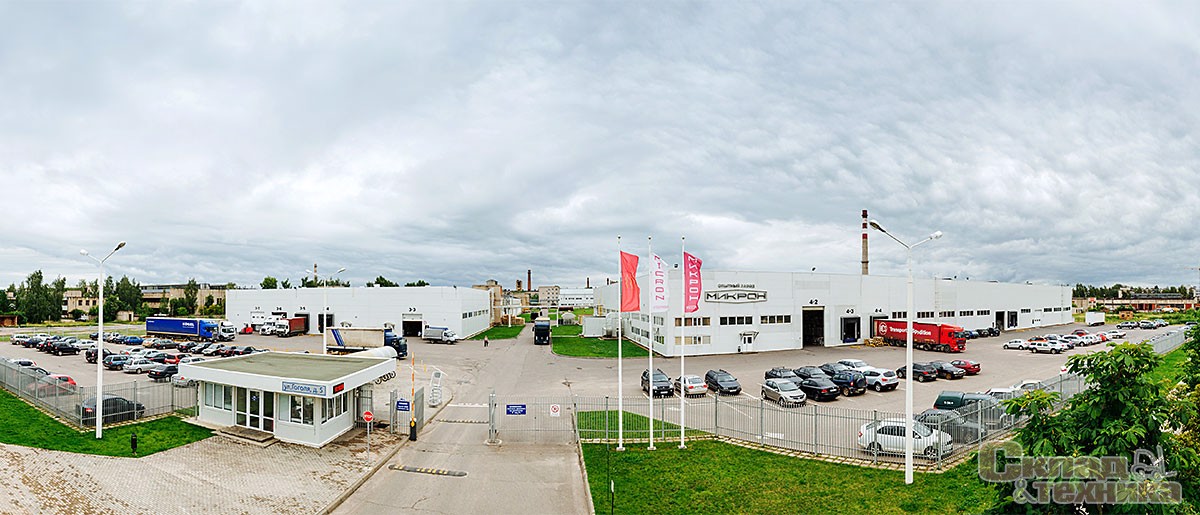
Опытный завод «Микрон»: «Умный склад» как элемент бережливого производства
Опытный завод «Микрон» – один из ведущих российских производителей стеллажей для компаний, торгующих продовольственными и непродовольственными товарами, распределительных центров и различных видов складов, а также торгового оборудования, динамично развивающийся и стремительно набирающий обороты. Это предприятие с полным технологическим циклом — от кроя листового металла до покраски готовых изделий порошковыми красками, производственные мощности которого способны удовлетворить растущие потребности в современном торговом и складском оборудовании.
Основной целью нашей компании являются разработка и внедрение комплексных решений, включающих все этапы организации складского пространства: от проектирования склада до сервисного обслуживания стеллажного оборудования. Главный приоритет в нашей деятельности – высокое качество продукции и ежедневное совершенствование всех производственных процессов.
Площадь производственного комплекса завода составляет более 40 тыс. м2, его мощность обеспечивает выпуск более 1 млн палетомест складских стеллажных систем в год. Численность сотрудников – более 900 человек.
Среди отличительных преимуществ ОЗ «Микрон» можно выделить:
- систему управления Lean Manufacturing («Бережливое производство»);
- систему менеджмента качества ISO 9001-2015;
- короткий срок изготовления продукции (от 7 дней);
- широкий ассортимент выпускаемых стеллажей;
- возможность изготовления изделий по индивидуальным эскизам;
- применение сталей повышенной прочности;
- наличие современного автоматизированного оборудования с быстрой переналадкой;
- возможность покраски изделий длиной более 12 метров;
- возможность окрашивания в любой цвет по каталогу RAL;
- наличие широко развитой дилерской сети.
Для производства стеллажей применяется как конструкционная, так и высокопрочная сталь (в зависимости от требуемой нагрузки). Для изготовления штампов и технологической оснастки на предприятии имеется собственное инструментальное производство, что сводит к минимуму простои оборудования и обеспечивает быстрое внедрение новых видов продукции. Все изделия проходят испытания на прочность и надежность для проверки соответствия теоретическим расчетам инженеров-конструкторов. Помимо этого проводятся и периодические испытания стеллажей.
Покраска изделий производится на покрасочных линиях Ideal (Дания). Современные технологии окрашивания металлических стеллажей обеспечивают качественное и долговечное декоративно-защитное покрытие. Порошковая краска, которая используется для стеллажей «Микрон», является самогасящимся и трудновоспламеняемым материалом, устойчивым к истиранию, поэтому покрытое ею оборудование имеет стойкую к огню, износу и коррозии поверхность.
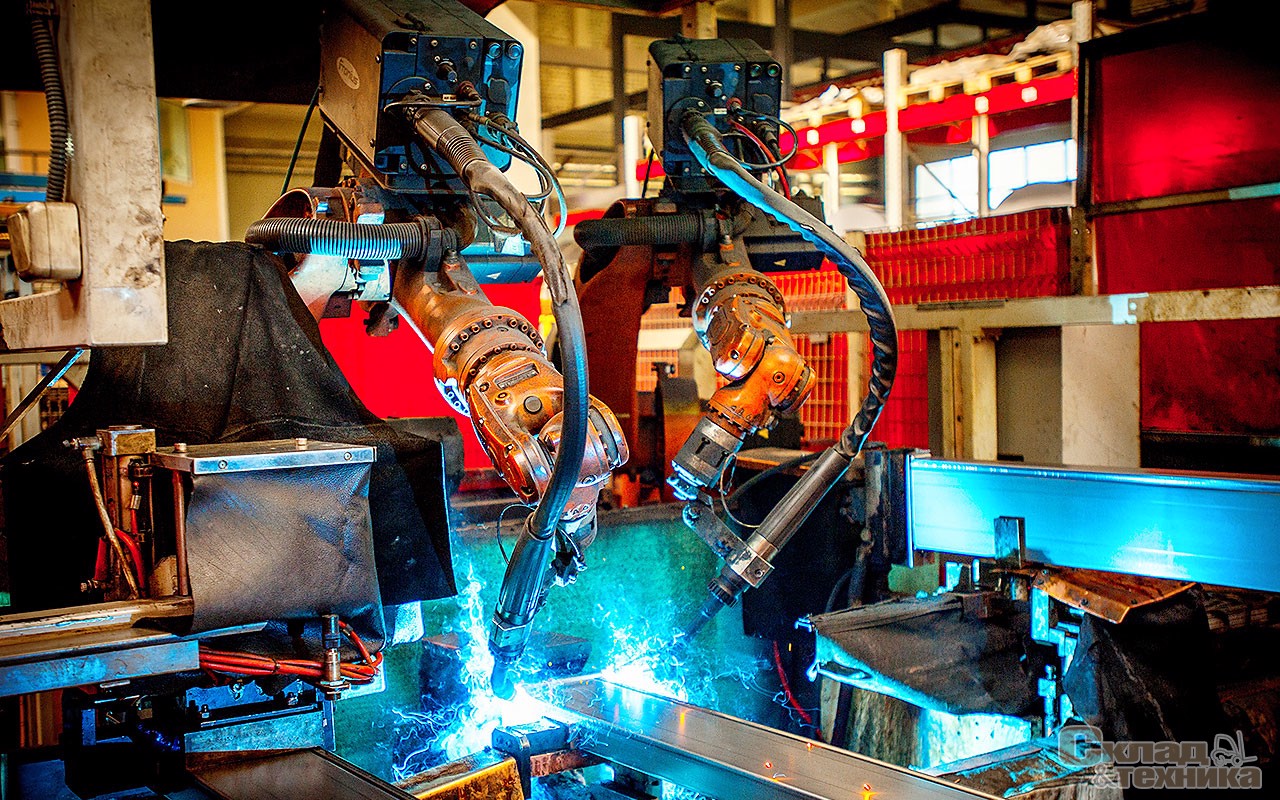
Современной модифицированной альтернативой стеллажам глубинного типа хранения является Автоматизированная стеллажная система с шаттлами, или «Умный склад».
Современное решение для автоматизации «Умный склад» оптимизирует технологические процессы хранения, сортировки и учета грузов. Эта система позволяет размещать большее количество товарных позиций (SKU), чем глубинные стеллажи, то есть дает возможность хранить однотипный товар в пределах каждого яруса стеллажного канала.
Управление шаттлом осуществляется оператором погрузчика с дистанционного пульта либо с мобильного устройства, работающего на базе операционной системы Android. Оператор имеет возможность управлять одновременно несколькими шаттлами с помощью одного устройства. Шаттл, получая команды по беспроводной сети, перемещает палеты внутри канала стеллажной конструкции на любую необходимую глубину и переставляется с яруса на ярус с помощью погрузочной техники.
Ложемент стеллажей такой системы представляет собой двухуровневые направляющие: нижний уровень – для передвижения шаттла, верхний – для размещения палет. Погрузчик ставит шаттл на ложемент, а затем загружает на него палету с грузом. Механическая подъемная система шаттла поднимает палету с грузом чуть выше яруса и перемещает ее в заданном свободном канале, после чего шаттл опускает палету на ярус и порожним возвращается в начало канала для следующей загрузки. Далее операция повторяется. По такой же схеме шаттл отгружает палеты. Погрузчик и шаттл работают одновременно, при этом простой погрузочной техники на складе сводится к минимуму.
Одним из достоинств системы является безопасность использования шаттлов за счет встроенных сенсоров (датчиков), которые не допустят травм оператора, повреждений стеллажных конструкций и груза. Все датчики делятся на функциональные сенсоры и сенсоры безопасности.
Большая скорость шаттла обеспечивает высокую производительность выполнения операций. При приближении шаттла к палете с грузом на расстояние около 2 метров срабатывает ультразвуковой сенсор, размещенный на его передней и задней панелях, после чего его скорость уменьшается до безопасного значения.
Сенсоры защитного бампера производят луч, при разрыве которого подается сигнал тревоги на пульт дистанционного управления. Причиной прерывания луча между сенсорами может стать испорченная упаковка груза (например, размотавшаяся пленка), которая попала в зону его действия, или препятствие в канале стеллажа. При разрыве луча срабатывает система экстренной остановки, и шаттл, снижая скорость, прекращает движение.
Кроме прочих приспособлений, обеспечивающих безопасность шаттла, система по отдельному запросу может быть оснащена вариантом защиты от падения с погрузчика – магнитами, установленными на днище шаттла, которые обеспечивают ему надежное крепление на погрузчике при транспортировке по складу. В стандартной комплектации днище имеет специальное противоскользящее покрытие.
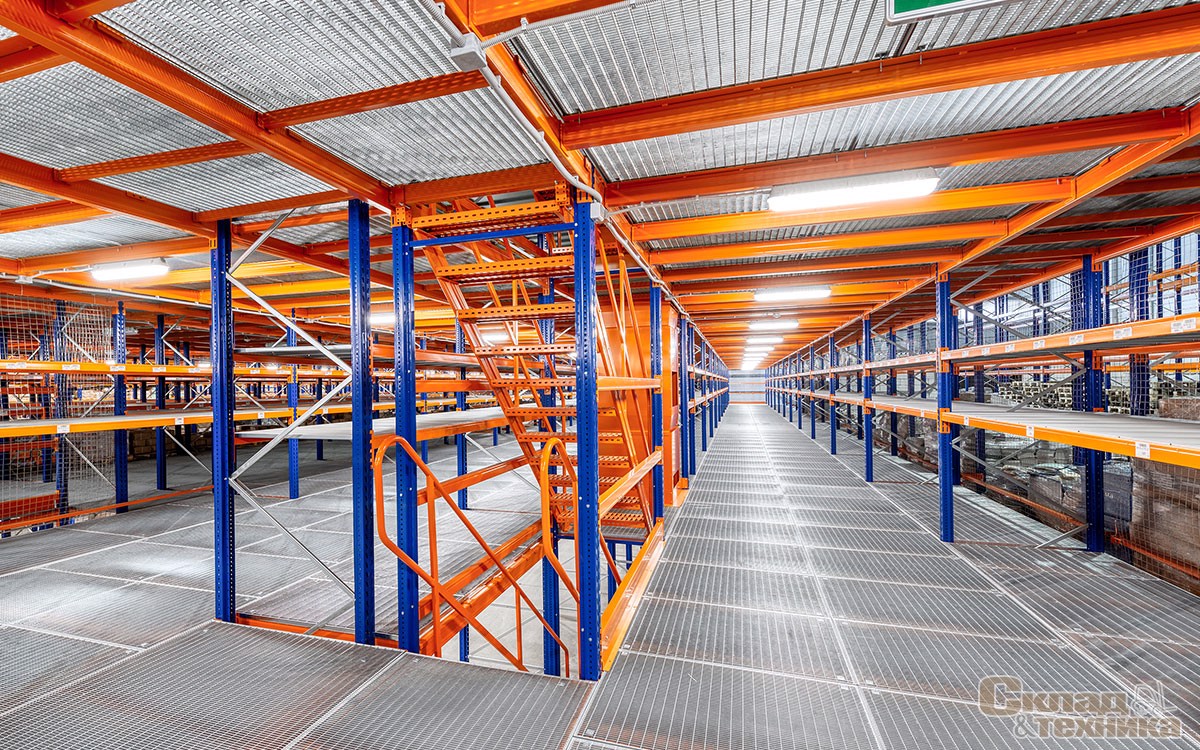
В автоматизированной системе предусмотрены следующие составные части:
- стеллажные системы – позволяют размещать большое количество палет с грузами при меньшей площади хранения;
- автоматизированная система наполнения, шаттлы и кран-штабелеры – позволяют оптимизировать технологические процессы хранения;
- устройство идентификации грузов с помощью штрихкодов или RFID-меток – обеспечивает распознавание грузов, исключая ошибки в работе операторов склада;
- система управления складом (WMS) – дает возможность интеграции с учетной системой заказчика, что позволяет получать актуальную информацию по топологии склада и остаткам в режиме реального времени.
К преимуществам «Умного склада» относятся:
- возможность использования до 80% объема складского помещения для хранения грузов;
- высокая скорость обработки (до 300 палет одним оператором за одну рабочую смену);
- реализация системы хранения LIFO (last in first out) – «набивные стеллажи» и FIFO (first in first out) – «проходные стеллажи»;
- соответствие концепции Индустрия 4.0:
1. Совместимость – все устройства автоматизированной системы хранения взаимодействуют друг с другом и системой управления на одном языке.
2. Прозрачность – создание цифровой копии склада посредством датчиков и сенсоров, установленных на «Умном складе».
3. Техническая поддержка – программное обеспечение производит сбор, анализ, систематизацию, визуализацию данных, полученных с датчиков, что помогает человеку принимать решение, или принимает их в автоматическом режиме, тем самым высвобождая человеческие ресурсы.
4. Децентрализация управленческих решений, автоматизация различных решений системами, максимально полное освобождение человеческих ресурсов;
- глубина хранения – до 250 м;
- экономия пространства, времени и финансовых затрат;
- работа в температурных режимах – от -30° до +45°С;
- высокая безопасность эксплуатации;
- долгий срок бесперебойной работы.
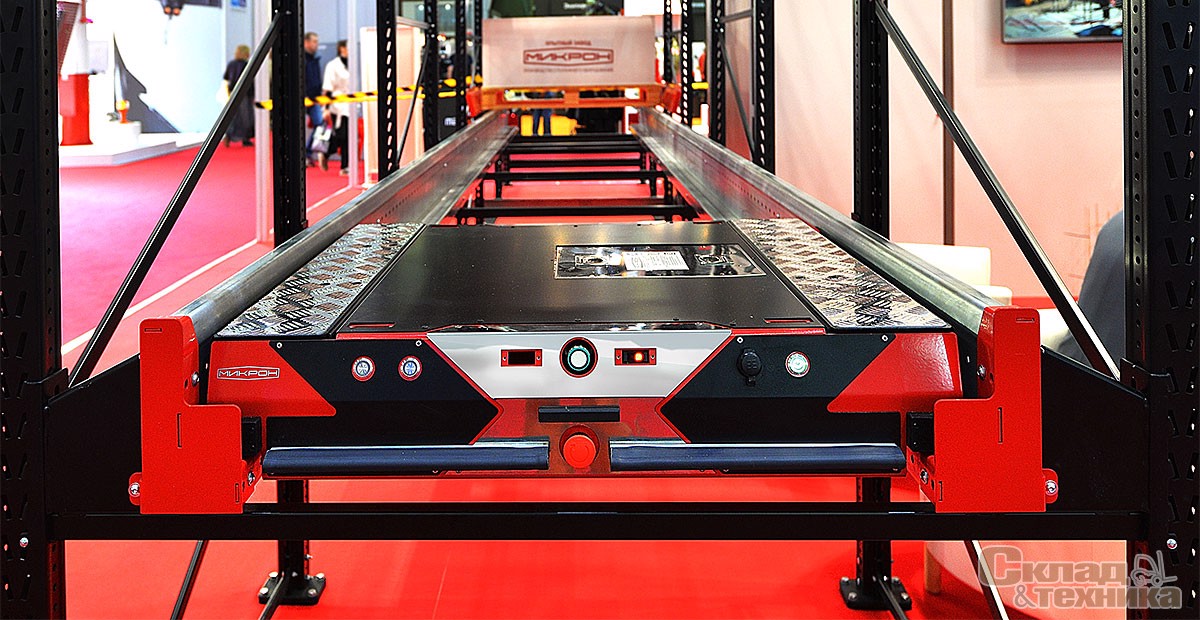
«Умный склад» как элемент бережливого производства позволяет:
- оптимизировать производственную логистику;
- добиться уменьшения складских площадей;
- оптимизировать обслуживающий персонал за счет того, что функции кладовщиков переходят к комплектовщикам участков;
- в любой момент времени определить остатки материальных ценностей на складе.
Как элемент развития производственной системы, это автоматизированное и высокоэффективное решение обеспечивает максимально возможную плотность хранения продукции на квадратном метре площади складирования.