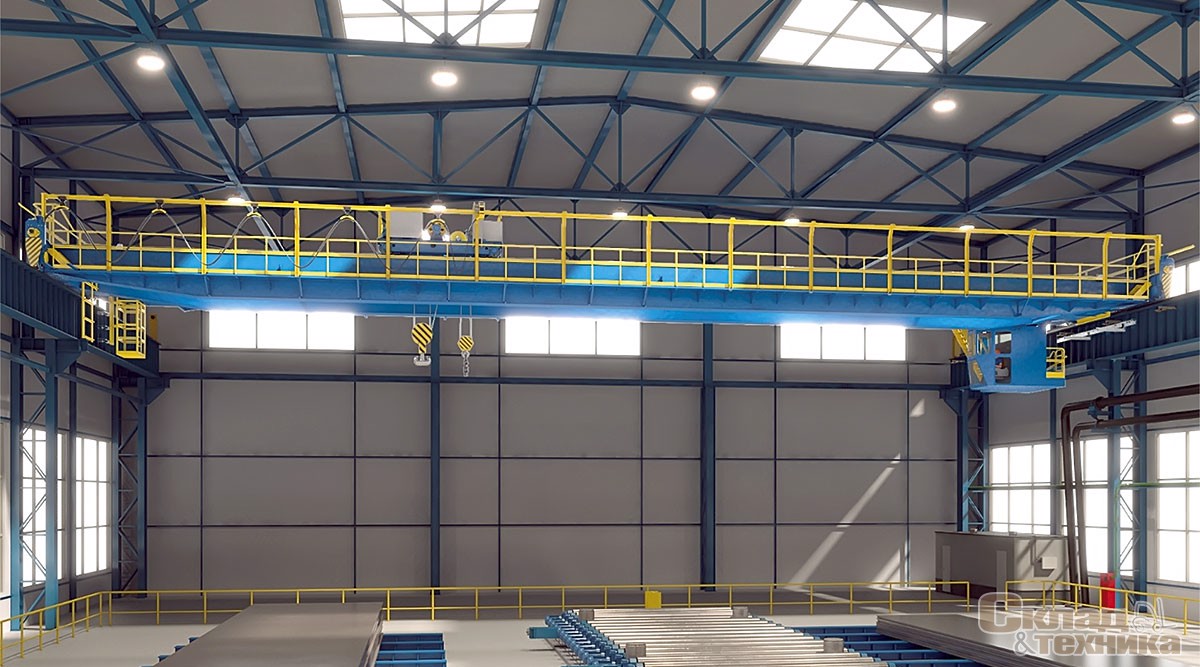
Умный склад на основе MAGNETTRACK
Введение
На сегодня с развитием технологий умные склады или 3D склады все больше входят в нашу жизнь. Внедрение 3D складов позволяет:
- быстро находить нужный товар;
- уменьшить или полностью исключить потерю материалов/товаров на складах;
- эффективно использовать складские площади;
- автоматически формировать отгрузочные документы.
Все это повышает конкурентоспособность предприятий, поскольку позволяет сократить издержки и потери, а также сделать все процессы более гибкими вплоть до изготовления индивидуальных изделий и розничной торговли.
В данной статье рассмотрены особенности реализации концепции «Умный склад» и систем прослеживаемости движения материалов для производств, владеющих средними и крупными складами, которые обслуживаются грузоподъемной техникой по типу мостовых, козловых и контейнерных кранов. Предложена революционная технология Magnettrack, которая позволяет исключить все слабые места традиционных технологий.
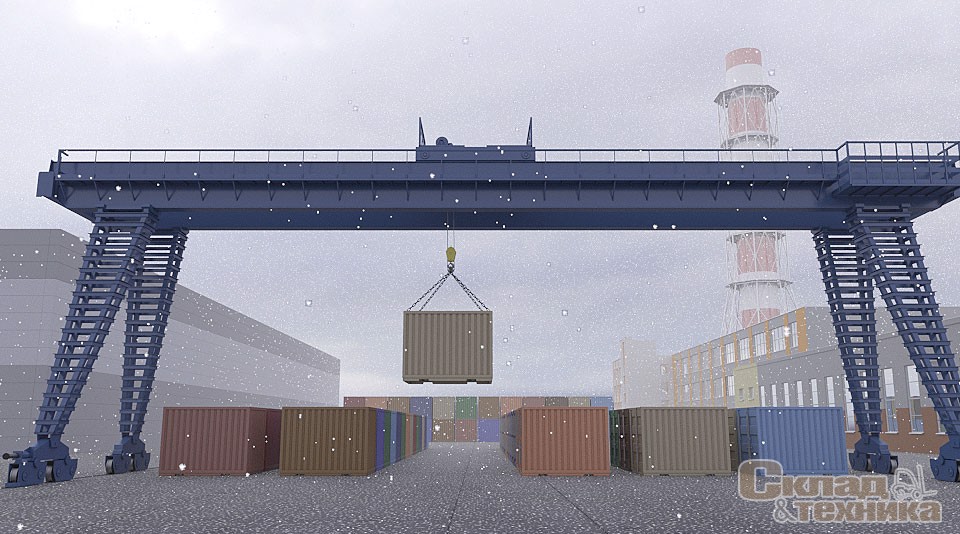
Особенности внедрения умного склада с применением кранов различного типа
Реализация проекта умного склада, на котором материалы перемещаются с помощью кранов на сегодняшний день невозможно полностью автоматизировать. Существует необходимость и в ручной помощи строповки грузов. А значит, в целях безопасности жизнедеятельности человека, управление кранами необходимо осуществлять в ручном режиме. В связи с чем проект умного склада осуществляет функцию слежения за перемещаемыми материалами и обновляет соответствующую информацию в учетной системе.
Чтобы внедрить функцию слежения, необходимо реализовать следующие основные задачи:
- идентификация перемещаемых материалов;
- определение координат перемещаемых материалов;
- изменение данных о перемещаемых материалах на сервере с помощью специализированного ПО.
По признанию руководителей проектов со стороны производителей, «ахиллесовой пятой» является вопрос по измерению координаты крановой тележки. Важным критерием при выборе системы измерения положения крана, является доступность и достоверность получаемой координаты всегда и везде с требуемой точностью.
При самых непродолжительных, но периодических сбоях в работе системы измерения координат, когда реальное положение крановой тележки (перемещаемого груза) не соответствует измеряемым значениям, система учета размещения материалов будет накапливать ошибки, выражаемые в несоответствии реального положения материалов и данных на сервере. Такая система требует постоянного ручного вмешательства в целях актуализации данных.
Для формирования требований к точности измерения положения крановой тележки должны приниматься во внимание следующие факторы:
- минимальный габарит складируемого материала;
- раскачка подвески крана;
- люфты и отклонения моста крана влево-вправо при движении;
- повторяемость системы измерения положения крана.
Руководители проектов умного склада все чаще склоняются к выбору наиболее точных измерительных систем для средних и малых материалов, как например ЖД колеса, предъявляя требования к максимальному значению повторяемости не хуже 10 мм.
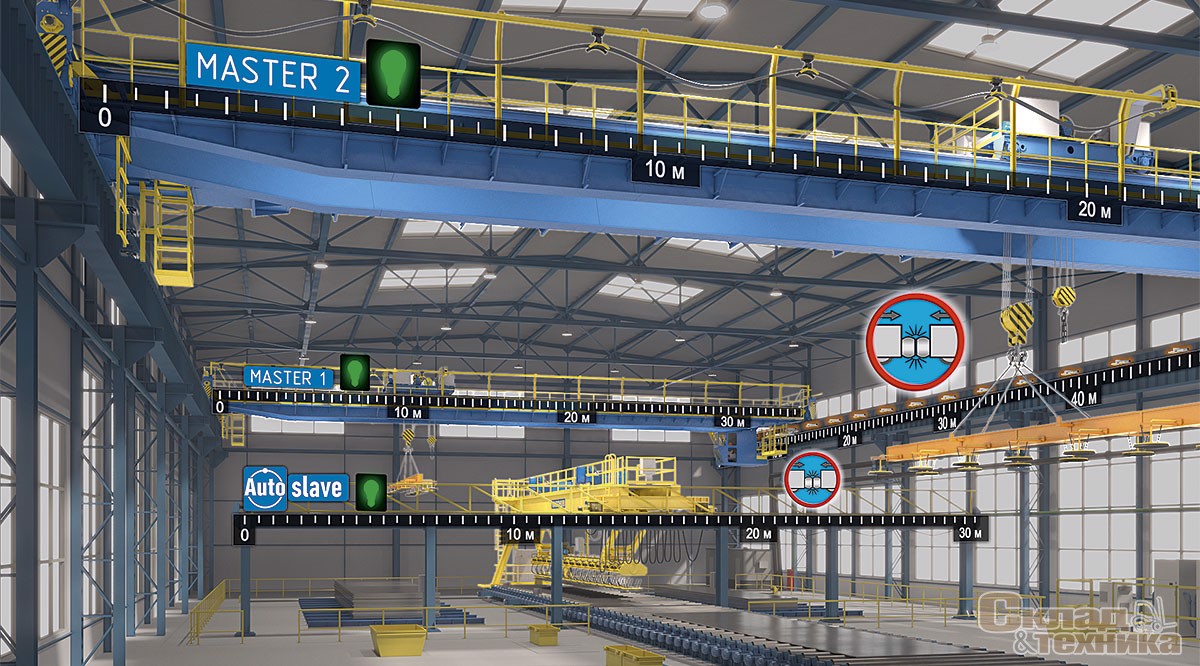
Существующие технологии для измерения перемещения
Известны следующие технологии и методы измерения координат:
- лазерные дальномеры;
- энкодеры с дискретными датчиками для сброса ошибки;
- системы радиочастотной идентификации;
- измерение перемещения с помощью оптического сканера и кодированной ленты;
- технология RTLS (сокр. от англ. Real-time Locating Systems – система позиционирования в режиме реального времени).
Каждое из перечисленных решений имеет существенные ограничения. В частности:
• Оптические системы (дальномеры, оптические линейки) требуют обслуживания и крайне уязвимы к загрязнениям. Их точность зависит от степени загрязнения и измеряемого расстояния. Так, уже на дистанциях около 50 м точность повторения может составлять более 10 см. Следует также учесть и то обстоятельство, что датчик, установленный на кране, подвержен вибрациям во время движения крана. Поэтому излучаемый оптический луч может не попадать в отражатель, особенно на дистанциях свыше 50 м. А если в одном пролете работает несколько кранов, то известны случаи, когда излученный одним датчиком луч принимался другим, что приводило к неверному измерению положения кранов.
• Системы позиционирования на основе энкодеров накапливают ошибку за счёт проскальзывания и износа колёс по набегу. Методы сброса ошибки посредством дискретной логики не работают надежно. Кран, например, может работать продолжительное время между двумя точками сброса ошибки, накапливая ошибку в измеряемой координате и передавая неверные данные о положении материалов на сервер. Известны случаи, когда накопленная ошибка измерения координаты составляла свыше 20 метров.
• Радиочастотные системы отслеживания перемещений крайне чувствительны к окружающим металлическим радио-отражательным конструкциям и имеют особые требования к местам установки компонентов. Отраженные волны могут пересекаться друг с другом и аннигилироваться, образуя так называемые радиопузыри. Точность работы радиочастотной системы, зависит от используемой частоты и расстояния до радиометок, и на практике составляет более 20 см. Наличие в зоне работы системы металлической пыли способно полностью блокировать работу радиометок. Такие системы отличаются сложностью монтажа и требуют многочисленных тонких настроек.
• Основной сложностью применения перфорированных лент является сложность их установки и зависимость натяжения ленты от температуры окружающей среды. Известны случаи, когда в летний сезон температурное расширение здания приводило к разрыву натянутой ленты, напротив, в зимнее время лента представляла собой изогнутую кривую, которая царапает оптическую поверхность сканера и выводит его из строя или выдает в учетную систему неверные координаты. Также следует принять во внимание возможные отклонения положения моста крана влево-вправо при движении, что также приводит к повреждению оптической поверхности сканера.
• Технология RTLS основана на активных радиометках, что уже подразумевает определенный уровень сложности обслуживания систем на их основе, так требуется следить за уровнем заряда батареек и наличия выключенных меток. Повторяемость подобных систем на практике составляет не менее 30 см. Запуск системы в эксплуатацию требует продолжительной и сложной настройки. Если после запуска системы, в цеху изменяется контур окружающих металлоконструкций, то система потребует дополнительной настройки, в противном случае, она может выдавать искаженную координату.
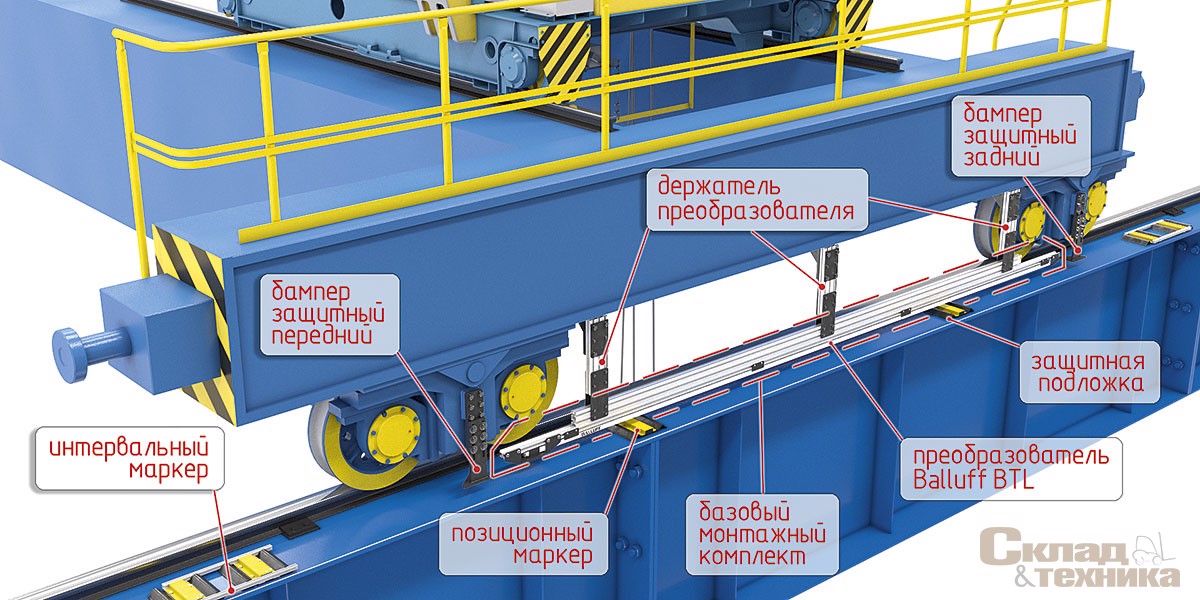
Система magnettrack
Учитывая все слабые места распространенных технологий, применяемых для реализации концепции 3D-склада, компания Balluff совместно с компанией Магнеттрек выпустили революционное решение – систему Magnettrack, которое позволяет исключить все описанные выше проблемы для измерения перемещений на средние и большие дистанции.
Данное решение состоит из трёх основных компонентов:
- магнитострикционный преобразователь линейных перемещений Balluff BTL;
- набор магнитных маркеров, каждый из которых представляет собой один или несколько магнитов в защитном корпусе;
- программный модуль magnettrack, интегрируемый в управляющий контроллер.
Преобразователь Balluff BTL устанавливается непосредственно на движущийся объект и вместе с ним движется вдоль магнитной трассы, состоящей из отдельных магнитных маркеров. Преобразователь считывает положение каждого магнита, над которым проезжает, относительно своей активной зоны и передаёт эти данные в управляющий контроллер, где программный модуль Magnettrack производит вычисление расстояний между соседними магнитами и на основании этих данных строит абсолютную систему координат.
Система Magnettrack обладает высокой надежностью и требуемой точностью, а также является абсолютной системой измерения положения, что позволяет восстанавливать координату в случае сброса питания. Адаптивный алгоритм программного модуля обеспечивает автоматическую перенастройку системы в случае внесения изменений в магнитную трассу, например, после ремонта рельсовых путей.
Система обладает следующими основными характеристиками:
- Бесконтактный и неоптический принцип действия;
- Дистанция позиционирования: от 3 до 700 метров и более;
- Повторяемость в статике: не хуже 10 мм;
- Максимальная скорость движения объекта: до 7 м/с;
- Ударопрочность 150g/6 мс в соответствии с IEC 60068-2-27;
- Вибростойкость 20g при 10…2000 Гц в соответствии с IEC 60068-2-6;
- Степень защиты: IP67 в соответствии с IEC 60529.
Система Magnettrack не требует обслуживания, а расчётный срок службы системы составляет 15 лет.
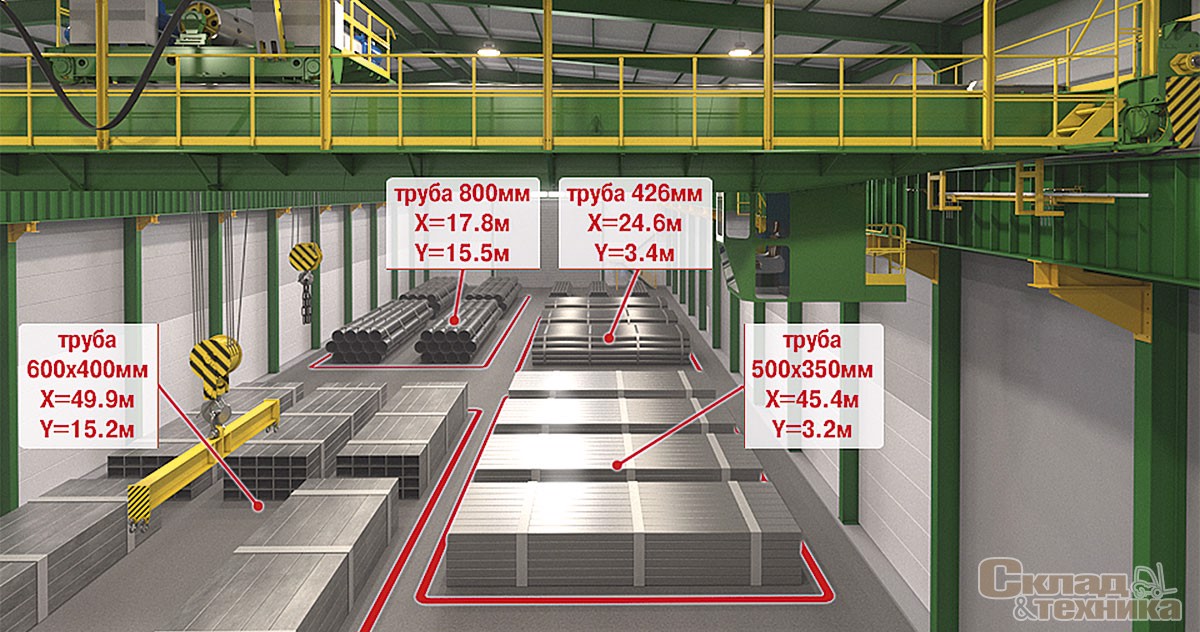
Опыт применения
Система уже установлена и успешно используется на 3D складах, а также применяется для задач слежения за перемещением материалов.
Краны, на которые установлена система, работают на дистанциях от 8 до 700 метров, обеспечивают высокую точность позиционирования даже в тяжелых промышленных условиях металлургического производства. Система Magnettrack применяется на производстве в условиях под открытым небом, что делает возможным ее применение для открытых складов.
Специалистами отмечена высокая надёжность системы: на более чем 100 установленных систем не было зафиксировано ни одного сбоя за все время эксплуатации.
Заключение
В производствах, владеющих средними и крупными складами, которые обслуживаются грузоподъемной техникой по типу мостовых, козловых и контейнерных кранов, реализация концепции «Умный склад» (3D склад) традиционными технологиями сталкивается с существенными проблемами, которые приводят к недопустимым сбоям, потерям точности, накапливаемым ошибкам. Предложенное компанией Balluff решение – система Magnettrack, основанная на магнитострикционном преобразователе и интеллектуальной обработке данных измерений, позволяет исключить эти проблемы. Система Magnettrack уже накопила широкий опыт внедрений, хорошо зарекомендовала себя как надежное решение и может быть рекомендована для автоматизации всех складов, которые обслуживаются грузоподъемной техникой типа мостовых, козловых и контейнерных кранов.