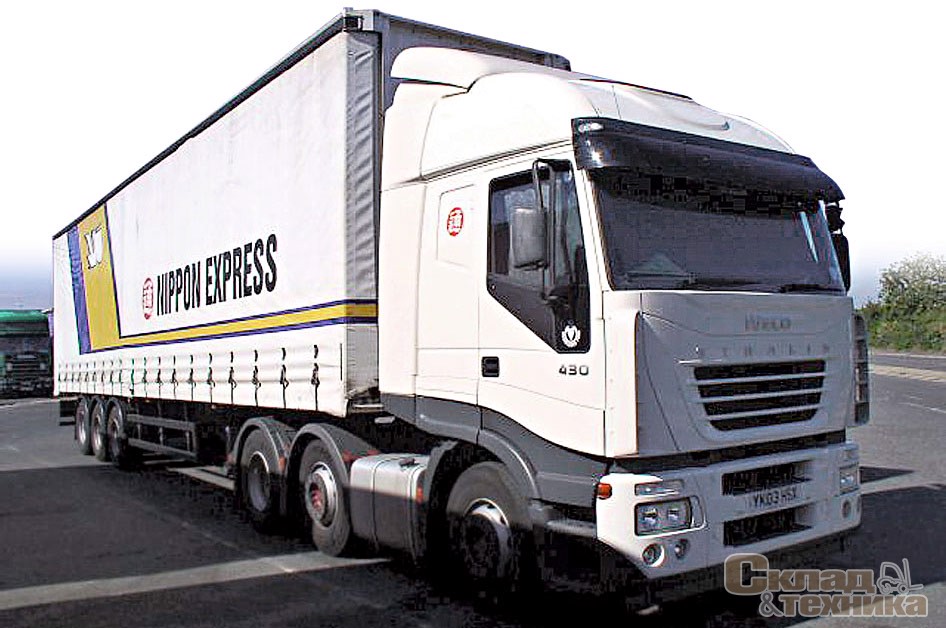
Как организована логистика автозапчастей в Германии
В Германии, как и во всей Западной Европе, автомобильная промышленность значительно влияет на деятельность ее поставщиков и их логистику. На складах автозапчастей используются особые системы обеспечения внутренних потребностей автомобилестроительных предприятий, среди которых наиболее широкое распространение получили решения, основанные на логистических концепциях «точно в срок» (just in time) и «точно одно за другим» (just in sequence). Основная идея этих концепций заключается в том, чтобы обеспечить доставку точно в указанный срок необходимого количества запасных частей, материалов и заготовок на производство, сборку и реализацию согласно расписанию предприятий. О том, как они работают в Германии, рассказывает Александр Рауш, директор по логистике компании ООО «Роберт Бош».
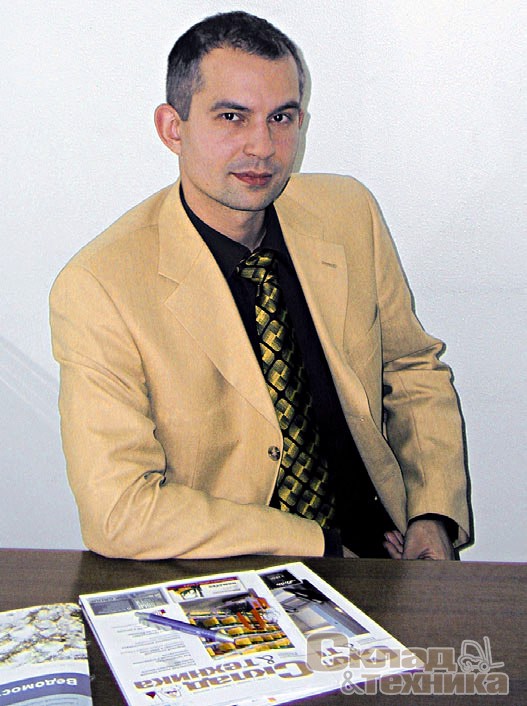
– Концепция «точно одно за другим» отличается от концепции «точно в срок» тем, что детали на конвейер поставляют в строгой последовательности по запросу завода. Самая простая концепция «точно вовремя» (canban) была разработана японской компанией Toyota. Она также хорошо известна в Европе, но используется реже. Реализация всех перечисленных подходов предполагает, что страховых запасов, которые замораживают денежные средства, не требуется и все поставки идут на конвейер строго в тот момент, когда это необходимо. Такая логистика оптимальна для производителей. Это именно те подходы, которые работают в европейской автомобильной промышленности лучше всего.
– В Германии есть автопроизводители, у которых нет своего склада, а есть только технологическая линия, где собирают машины и куда поступают запчасти.
Поставщик гарантирует своевременную поставку деталей со своего склада к конвейеру. Автопроизводитель поддерживает запас комплектующих лишь на несколько часов, чтобы компенсировать незначительные сбои поставок. В последнее время наиболее популярными становятся так называемые «парки поставщиков» (supplier parks): склады поставщиков и часть их производства для удобства расположены на прилегающей к автопроизводителям территории. Это логистическое решение сейчас начинают внедрять в российском представительстве компании Bosch.
Надо отметить, что такие крупногабаритные детали, как пластмассовые панели для автомобилей, не хранят и не перевозят на большие расстояния, а, как правило, производят в непосредственной близости от предприятия, с конвейера которого сходят автомобили. Автопроизводители не изготовляют подобного рода крупноформатную продукцию, делегируя эту функцию поставщикам.
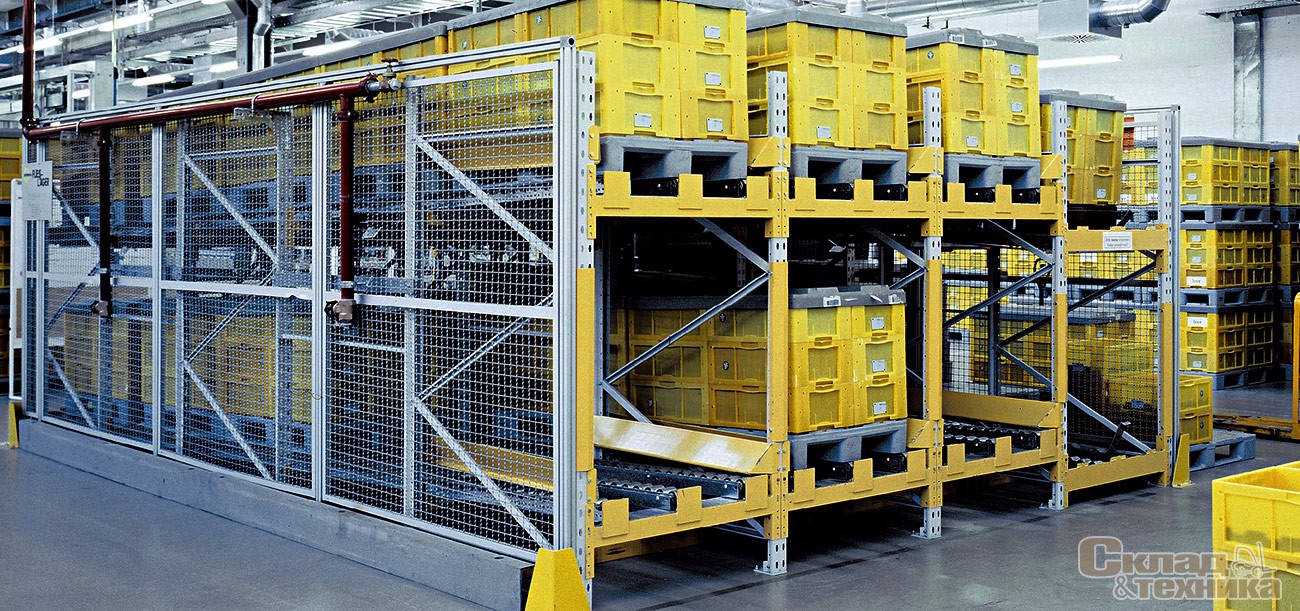
Европейские и японские автопроизводители руководствуются данными концепциями. Их российские заводы, занятые сборкой завезенных из-за рубежа комплектов, пока не оказывают такого большого влияния на систему поставки запчастей, существующую у поставщиков. Поэтому требования к ней ниже, чем на Западе.
Отличительная особенность логистики закупок немецких автопроизводителей – наличие точного планирования. В России процесс планирования краткосрочный, такой детализации поставок пока нет. Практически у каждого автопроизводителя есть склад, на котором хранится определенный запас комплектующих. По-видимому, это связано с нерегулярностью поставок. Российские предприятия пока не предоставляют возможность своим поставщикам использовать на практике передовые логистические концепции, поскольку последние подразумевают очень длительное планирование. Например, в Германии автопроизводители дают своим контрагентам прогноз на поставки со складов за 6 месяцев до их начала, за 3 месяца его детализируют и за месяц расписывают по дням, что и когда должно быть получено. В России европейскую модель логистики только начинают внедрять.
Первыми шагами к ее внедрению в компании Bosch можно считать планирование консигнационных складов, т. е. складов, которые принадлежат поставщику, но размещаются на территории производителя. Это позволяет минимизировать расстояния, гибче и быстрей отвечать на запросы производителя.
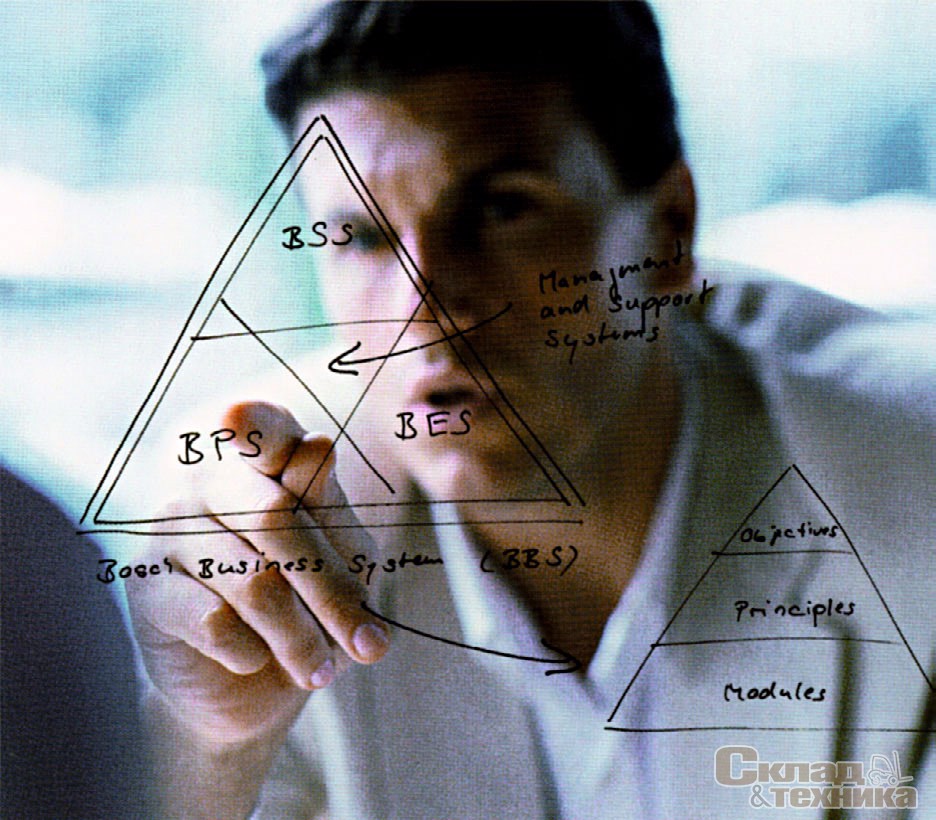
– Строить работу на основе всех перечисленных концепций с учетом больших объемов производства возможно лишь при условии полной поддержки соответствующим программным обеспечением как автомобильного завода, так и склада поставщика автозапчастей. Наиболее приемлема система электронного обмена данными (Electronic Data Interchange или EDI), с помощью которой обеспечивается оперативное взаимодействие между производителем, складом и поставщиком.
Надо также учитывать, что при поставках информация, содержащаяся в штрих-кодах на бумажных носителях, должна дублироваться. Лучше всего это делать на этикетках, где уже зашифрована большая часть данных о товаре и поставке. В Германии существует такой стандарт, как VDA (Verbаnd der deutschen Automobilindustrie). Это специальный стандарт этикетки для автомобильной промышленности, который должны использовать все поставщики, чтобы успешно работать с производителем. В нем точно расписано, какие штрих-коды должны быть нанесены и какая информация в них должна содержаться. Такая стандартизация помогает компании Bosch работать с большим числом клиентов.
В автомобильной промышленности России такой стандартизации этикеток нет, поэтому здесь автопроизводителям еще предстоит прийти к общему соглашению о стандартах маркировки. В Германии вопросами, касающимися стандартизации, занимаются объединения автопроизводителей и автомобильной промышленности. В ходе обсуждений утверждаются сначала минимальные нормативы, а потом рассматриваются дополнительные требования, в рамках которых каждое предприятие может менять что-то самостоятельно.
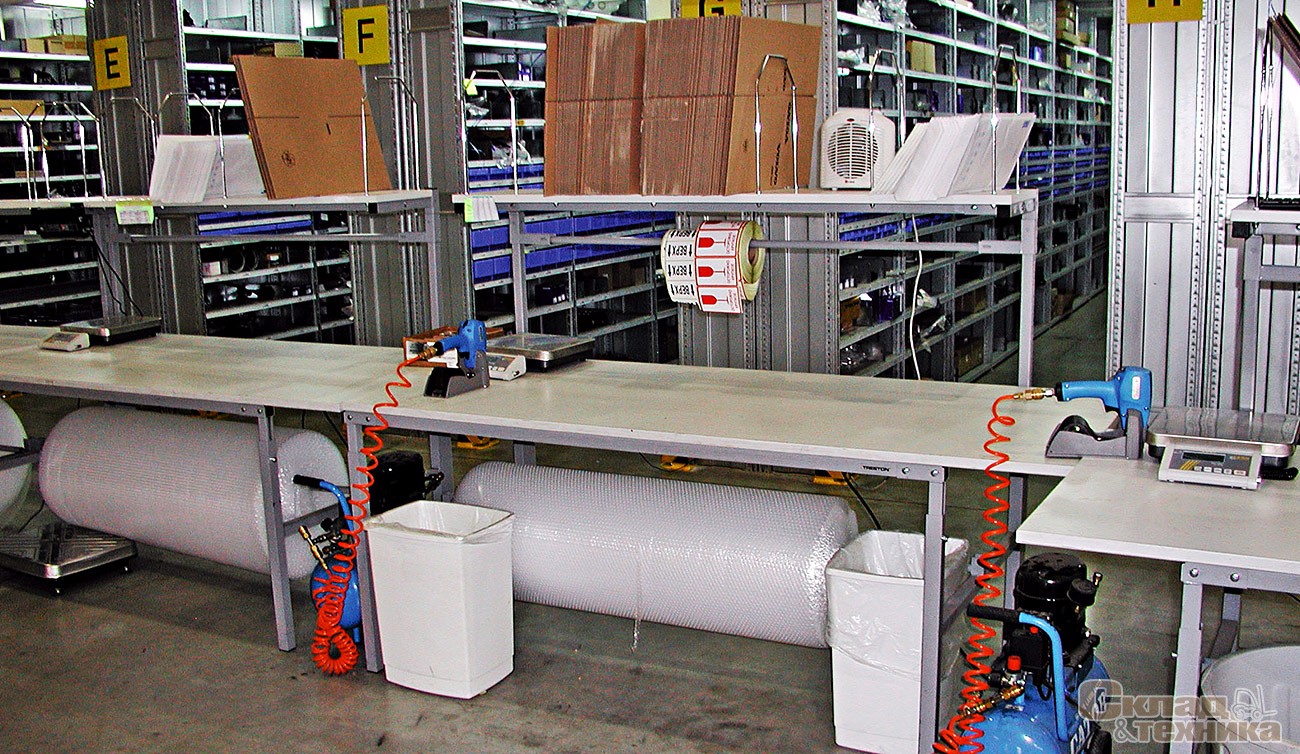
– Национальным автопроизводителям стоит улучшить организацию производственного процесса. В России глубина процесса производства автомобилей значительно больше, чем в Германии, где он сокращен до минимума. Это связано с тем, что большое количество комплектующих производится непосредственно автопроизводителями России. Европейские концепции так или иначе нужно здесь внедрять, но с учетом местной специфики: в первую очередь это расстояние и состояние инфраструктуры.
Важным фактором является и интеграция логистических концепций в систему управления складом (WMS). В WMS должны быть отражены все требования к хранению автозапчастей. Эта система занимается размещением большой номенклатуры товаров. Необходимо создать полную базу данных по всем весовым и другим характеристикам изделий, чтобы не нарушать работу WMS-системы. Но здесь возникает еще один вопрос: как отобразить в ней требуемые параметры хранения автозапчастей? Многие WMS-системы работают только с объемными параметрами единиц хранения, что не позволяет учитывать их физические габариты. По этой причине не всегда можно определить, поместится ли та или иная деталь в ячейку хранения. Система управления складом должна отслеживать все эти тонкости. Обычно стандартный подход WMS-системы всегда корректируется человеком, который может выбрать ту или иную ячейку, изменить ее конфигурацию и т. д. И все-таки в ячейке остается примерно 20% «воздуха», которые не используются. Cамое простое из того, что применяется сегодня во всех отраслях промышленности, – это динамичное складирование, которое предполагает, что WMS выбирает лучшую ячейку по размерам, объему или иным критериям. В этом случае употребляются также такие параметры, как АВС-анализ, сокращение путей подбора заказов и др. Поэтому поставщики зачастую стараются создать свои системы управления, которые помогают решить вопросы оптимизации внутрискладских процессов.
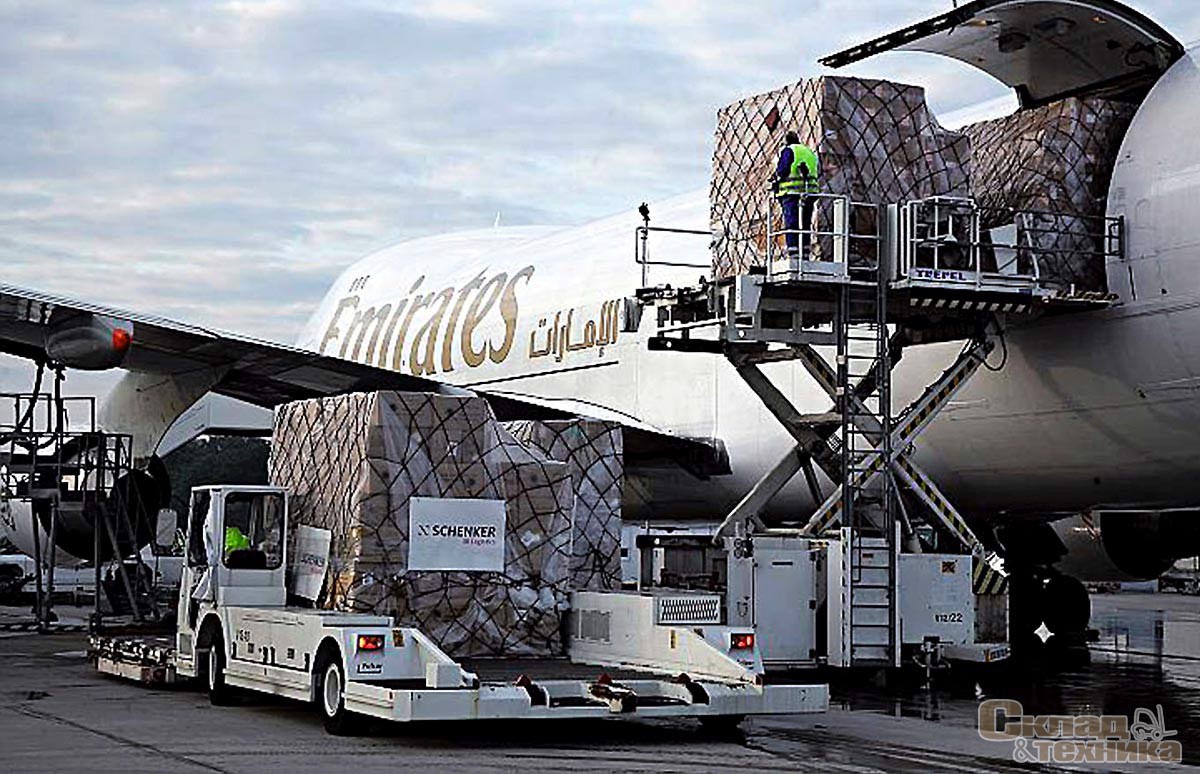
На складе автозапчастей есть товары с определенным жизненным циклом, который необходимо отслеживать. С многими автопроизводителями у компании Bocsh есть договоры поставок, которые заключаются сроком на 20...30 лет. Это делается для того, чтобы через 25 лет можно было купить оригинальную запчасть, например, для автомобиля Мerсedes-Benz, причем точно такую, какой она была четверть века назад. Соответственно на одном месте можно хранить поставки и одного месяца, и одного квартала, и года.
Есть и еще ряд специфических моментов, характерных для складирования в автомобильной промышленности. Во-первых, вплоть до поставки компонентов на конвейер необходимо отслеживать всю логистическую цепь в обратном направлении, как это сейчас и делают в Германии. Это надо для того, чтобы знать, где и когда изготовлена та или иная автозапчасть, и тогда при возникновении проблемы можно точно определить причину ее возникновения и оперативно выправить ситуацию. Это, наверное, один из самых важных факторов гарантии высокого качества продукции на протяжении всей цепи поставок автозапчастей.
Другим важным моментом, который следует учитывать, – это обращаемость изделий. Дело в том, что та часть деталей, что идет в автомаркет, т. е. на вторичный рынок, должна храниться долго, а у другой, поступающей на конвейер, напротив, короткий срок складирования. Если все спланировано точно, то у запчасти, предназначенной для сборки автомобилей, в принципе очень большая оборачиваемость: она находится на складе только то время, которое надо затратить на таможенное оформление в России. Продукцию могут оформлять и два часа, и два дня, поэтому на случай задержки необходимо иметь определенный запас на складе. Логика поставщика заключается в том, чтобы на каждом этапе логистической цепочки хранить только то, что требуется в данный момент. Она кардинально отличается от того, что было раньше, когда все, что произведено, сначала попадало на склад и лишь после этого к клиенту.
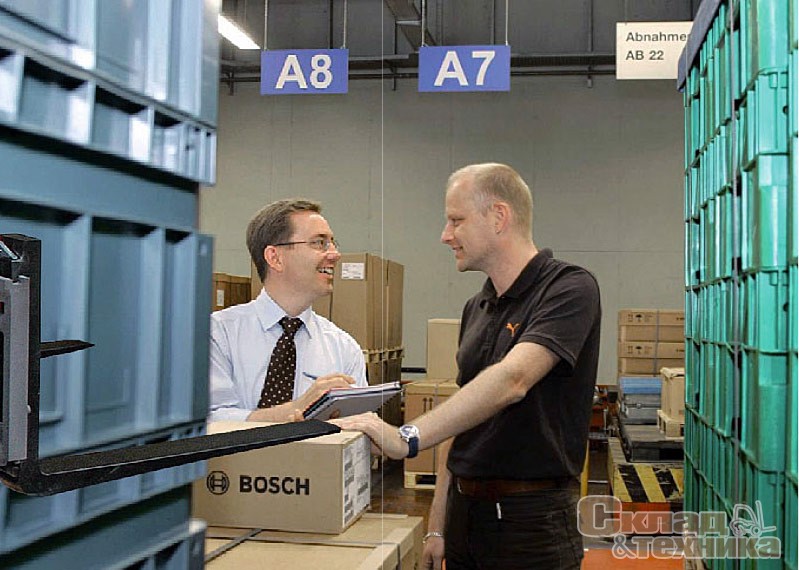
– Если говорить о чисто складских услугах, то, наверное, это произойдет довольно скоро. Экономика России движется семимильными шагами и за год преодолевает путь, на который европейским странам понадобилось не менее трех лет. Но, как известно, чем ближе финиш, тем тяжелей становится дорога, а на преодоление последних метров нужны самые большие усилия.
Темпы строительства складов здесь тоже рано или поздно замедлятся. Сказать, когда это произойдет – через 5 или 10 лет, трудно, ведь пока этот рынок только начинает развиваться. Но было бы не совсем правильно говорить только о том, когда же именно Россия догонит по складским площадям Европу. Российская логистика в целом должна достичь европейского уровня развития и обеспечить полную цепочку поставок. Мы должны думать не только о хранении, но и о совершенствовании каждого звена логистики, о транспорте, об информационных потоках и др., т. е. не об улучшении отдельных участков, а об улучшении их совокупности. В этом отношении в России очень большой потенциал, здесь можно и нужно развиваться…