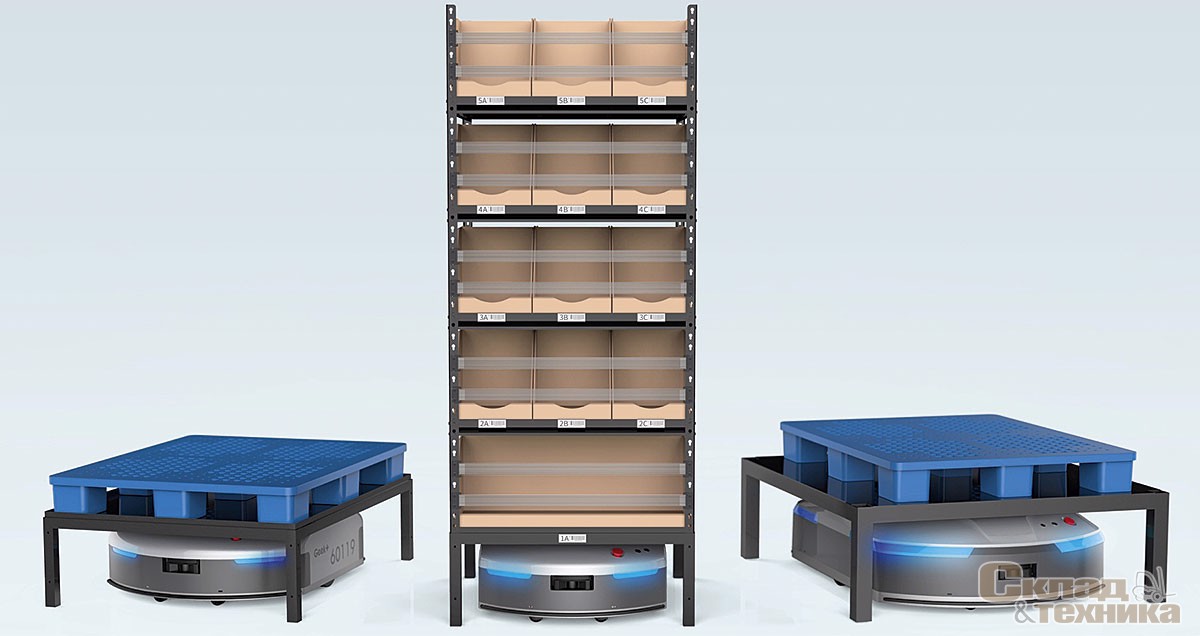
«Роботизация холодных складов со скоропортящейся продукцией»
Охлажденная продукция востребована, однако капризна в транспортировке и хранении. Когда нужно быстро доставить и сохранить ее первоначальную свежесть, счет идет на часы.
Промежуточным звеном между производством и магазином является распределительный центр, где нужно максимально быстро и без пересортицы организовать поставку в точки сбыта. Проблема может скрываться в том, что при неправильной организации процесса можно потерять драгоценные дни хранения на полках магазина, а когда до конца срока хранения остается 5-7 дней, то такую продукцию магазин просто не примет, ввиду нехватки времени на его продажу. Продукт придется списать, так что выгоднее не принимать вовсе. Производству приходится идти на всякие ухищрения в виде проставлении даты изготовления авансом на несколько дней вперед. Управляющие магазина понимают, что это убытки ближайшего будущего. Облегчить ситуацию и быстрее реализовать продукцию возможно благодаря внедрению различных акций и других активностей, чтобы как можно быстрее ее продать. Производители могут задаться вопросом: «А почему нельзя сделать так, чтобы можно было отгружать сколько нужно и при этом наращивая обороты производства?» Для этого потребуется оптимизировать процессы, но так, чтобы можно было обойтись без серьезных перестановок, аккуратно присоединившись к существующему процессу, дополняя его. Стандартный процесс обработки «ультрафреш» продукции может выглядеть следующим образом: обработанная продукция попадает на конвейер, где наносятся стикеры, а после всё размещается на паллетах. Далее требуется собрать микс-паллету и разместить её в зоне хранения для последующей отгрузки по магазинам. Если продукцию после конвейера отгружать в монопаллетах и сразу вести в РЦ для последующей комплектации, то возникает вопрос о ее наибыстрейшем наполнении. Здесь начинается процесс приемки, раскладывания по стеллажам паллетного хранения, создается так называемая «муда» (с японского, означающее «бесполезность»), так как дальше при комплектации заказа в магазин потребуется их спуск вниз. Теряется драгоценное время, приходится приостанавливать производство, чтобы избежать переполнения РЦ из-за несвоевременной отгрузки из него.
Как эта ситуация может быть рассмотрена под другим углом
В распределительном центре можно применить принцип «Товар к человеку», когда вместо подъезжающих с товаром на штабелерах работников, нужный ассортимент доставляется без участия людей к точке комплектации. Для этого можно использовать автономные роботизированные платформы, приподнимающие и перевозящие в нужное время мобильные стеллажи прямо к сборщику на рабочую станцию.
Приемка выглядит как укладка паллеты на подъехавший мобильный стеллаж тем же штабеллером. Сотрудник сканирует штрих-код, робот отвозит этот стеллаж сразу в холодную зону хранения, выезжая из-под него и оставляя его там. После этого доставляет следующий пустой стеллаж. Роботов может быть несколько, в зависимости от количества стеллажей.
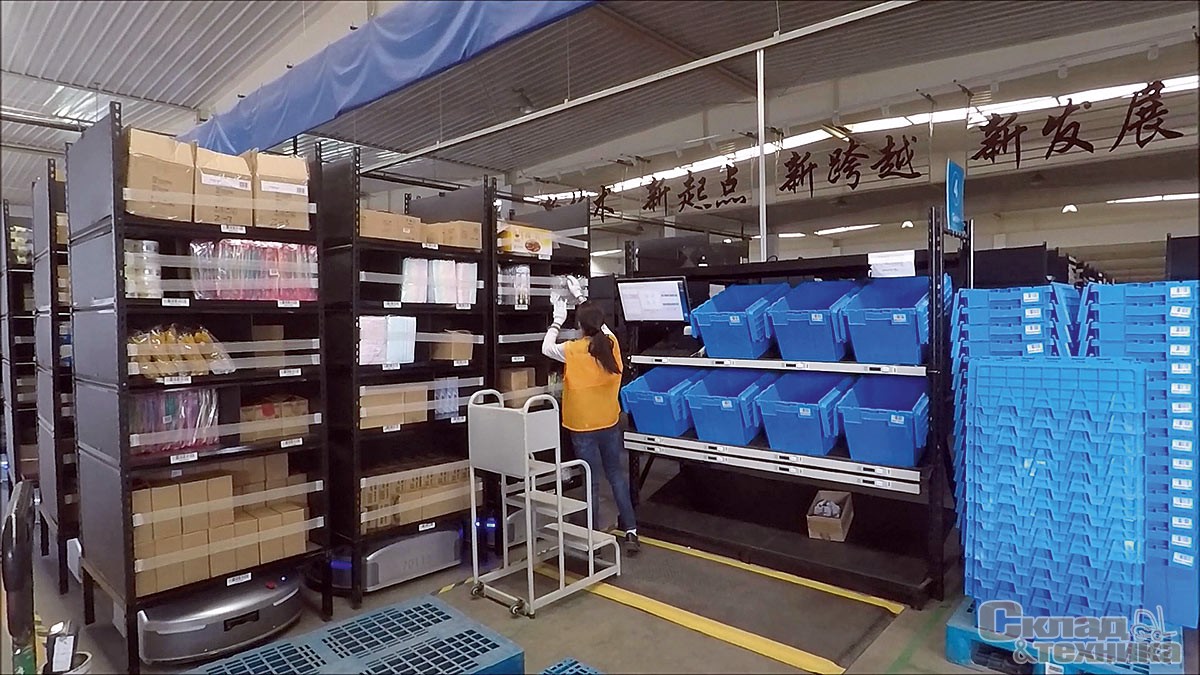
Чем это отличается от обычных операций по перемещению паллет на верхние полки?
Сейчас выстраивается транспорт в соответствии с расписанием, либо используется большая зона приемки, чтобы в ней сформировывать и вывозить транспортные паллеты. Решаемая задача с помощью мобильных стеллажей — это экономия места в зоне приемки, например, это может быть размещенный на носителях и стеллажах товар, рассортированный по ним. Такие стеллажи умещаются на меньшей площади.
Плюсами роботизированного решения являются: сокращение персонала до четырех раз при сохранении той же производительности, сокращении до нуля перемещений операторов, так как они стоят на месте, а также более компактном размещении товаров в операционной зоне комплектации по сравнению с традиционными способами с использованием паллетных стеллажей. Если нужно занять всю высоту склада, то можно использовать мезонин.
Сам мобильный стеллаж имеет несколько регулируемых по высоте полок-уровней. Он сочетает в себе достоинства обычного полочного стеллажа и при этом является мобильным. Основание стеллажа может быть использовано как мобильная платформа для паллеты, так и для мобильного полочного стеллажа.
В один стеллаж войдет несколько разных SKU, которые будут структурированы. Мобильный стеллаж позволяет создать временное структурированное хранение мелких (вплоть до штучных) партий товара и осуществить комбинированную сборку коробками и штуками. Так достигается повышенная гибкость при комплектации.
Плюсом является относительно дешевая замена тяжелого и громоздкого шаттла. Мобильность роботизированной системы означает, что ее можно взять и перевезти на другой склад, в отличие от шаттловой системы, которая остаётся на складе раз и навсегда. Для роботизированной системы понадобится только пол и место, куда роботы будут выезжать. Скорость разворачивания такой системы на объекте многократно выше, чем аналогичные решения. Весь проект можно реализовать в течение 3–4 месяцев, включая производство оборудования.
Гибкость достигается благодаря простому интерфейсу программирования и возможности интеграции с текущей WMS системой. Масштабируемость обеспечивается путем добавления новых роботов и стеллажей, причем в случае поломки добавляется еще один робот без необходимости остановки остальных роботов. Роботизированные платформы ездят со скоростью до 2 м/с по гибким перепрограммируемым маршрутам. Роботы не отвлекают людей, подвозят стеллажи, сортируя их по маршрутам отгрузки.
При таком подходе бизнес-процессы РЦ организованы настолько оптимально, что могут позволить за несколько часов переработать и отправить продукцию ее потребителям за несколько часов. А это крайне важно для комплектации скоропортящейся продукции «ультрафреш».
Благодаря технологии «товар к человеку» сотруднику склада нет необходимости идти или передвигаться на специальной технике к нужному стеллажу, затрачивая время на ориентирование между рядами и полками. В системе есть рабочие станции для комплектации, где находится работник, и стеллажи, которые робот подвозит по запросу. Очередность и потребность в доставке именно нужных стеллажей задает WMS (Warehouse Management System) через систему управления роботами (RMS). Так же есть возможность замены такого работника на манипулятор (с захватом или присосками), который будет выполнять эту рутинную работу с меньшим количеством ошибок и без перерывов. Система работает в связке с существующей WMS системой, хотя может работать и без нее, выполняя функции данной системы самостоятельно.
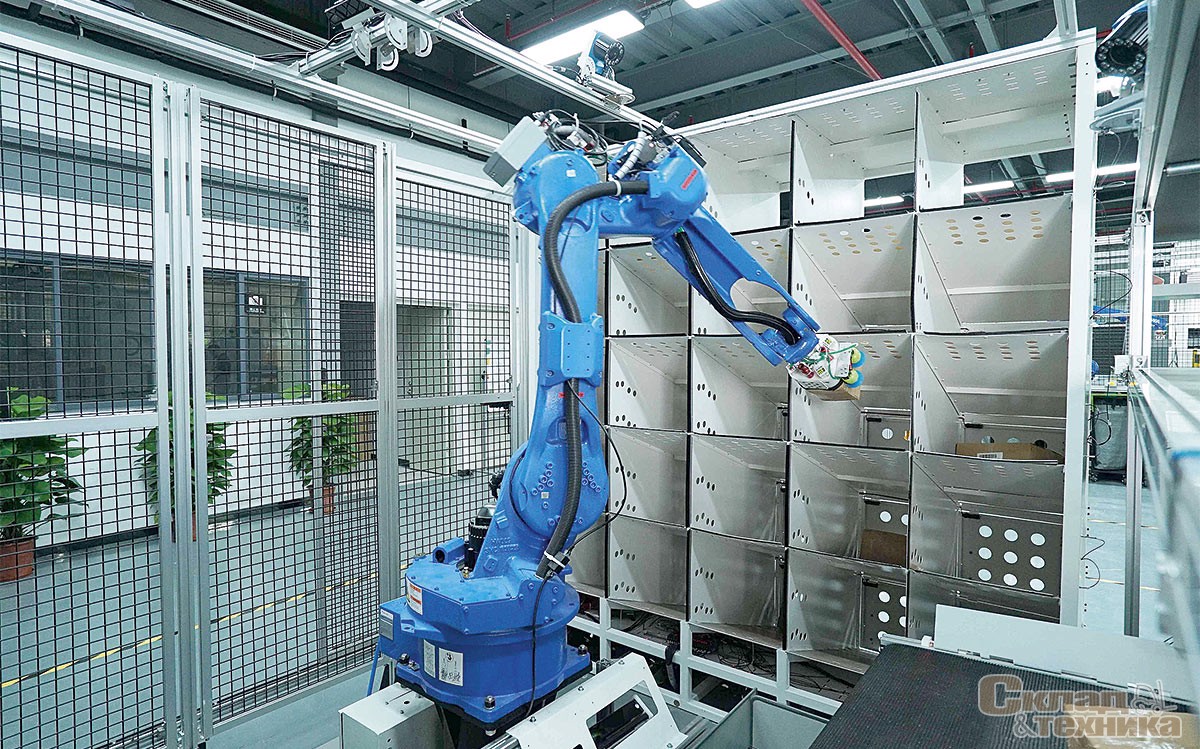
Как можно реализовать такой проект?
Предположим, что крупная сеть магазинов решила организовать такой распределительный центр. Для этого она принимает решение либо о модернизации старого склада, либо о строительстве нового. Это нужно для того, чтобы роботы могли «чувствовать себя, как дома». Мы привыкли, что склады ориентированы под людей, там есть широкие проходы как для них, так и для техники. Однако, роботизированное хранение предполагает установку мобильных стеллажей плотно друг к другу с расстоянием между собой 10-15 см.
После расчистки склада ставятся укрепленные мезонинные системы, выдерживающие нагрузку в 1500 кг на 1 м2 (с бетонным покрытием твердостью В30 по DIN, покрытым обеспыливающим слоем), пол маркируется QR кодами, собираются мобильные стеллажи, рабочие и зарядные станции, устанавливается и настраивается сетевое оборудование, обеспечивающее свою защищенную Wi-Fi сеть.
После запуска и обкатывания роботизированных систем в холостую с виртуальными товарами, настает очередь для физических товаров. Возможно развернуть небольшой участок с малым количеством стеллажей и роботов и на нем проверить слаженную работу всей системы. А после тестового периода развернуть систему уже на всей территории склада.
Чтобы все это внедрить нужен как поставщик, так и интегратор, последний ориентирован на результат. В его интересах организовать грамотную поставку и безошибочную интеграцию с существующими системами. К счастью, на рынке уже имеется российские компании, у которых есть опыт реализованных внедрений, а что самое главное, опыт недопущения сложных ошибочных ситуаций. При потребности в дополнительной информации они консультируются напрямую с производителем роботизированных систем. Также идеальным вариантом является референс-визит к одному из клиентов, у которого это уже внедрено, или же в специальный демо-зал.
Экономический эффект от внедренного решения
Как правило, стоит рассчитывать на выход на окупаемость на срок в 2-3 года в зависимости от интенсивности использования системы. Система будет долго окупаться на небольших предприятиях где особый эффект замечен не будет, поэтому стоит ориентироваться на большие склады. Если со временем понадобится масштабирование всей системы, то оно не будет сложным, так как останется только добавить дополнительные стеллажи и роботы. Вся производительность роботизированной системы просчитывается с помощью математических моделей, где эмулируются реальные процессы, включая пробеги, доставки, комплектации, пополнения. Система моделирования сама подскажет, сколько потребуется роботов для обеспечения заданных показателей. Убрав человеческий фактор, будет возможно сэкономить не только на ФОТ, но и на компенсации за человеческие ошибки и порчу товаров.
Подводя итоги, можно предположить, что как бы сильно не менялись условия рынка, всегда найдутся решения для поддержки его участников. Это могут быть разные технические решения, однако правильность выбора во многом влияет на то, кто будет завтра лидером рынка. Роботизация – всего лишь инструмент, которым предстоит рационально и вовремя воспользоваться.